CJD
Yoda

Offline
Here's this week's update. Moving along with the left door, as I "left" it last week, the upper forward edge is still mangled from the 2 accidents. I decided to cut a good section from another skin that was rusted at the bottom, but this section was good.
This drastically improved the shape of that corner, but when held up to the actual body, the contour was still off in this area. Steve, this is the question you asked in an earlier thread, about what to do to get the door gaps even and correct. Well...here's the process:
This is the door held in the opening. The bottom and rear look good.
The problem is shown here. Remember the fender is not mounted back far enough, so I am not concerned with the size of the forward gap...but I am about it being even from top to bottom. As you can see...it is not.
Here I am welding beads on the edge that is gapped to far. I am using .023" steel wire. On my Millermatic 185, the setting is at 1 (the lowest), and feed at 40FPM. Just add bead upon bead until you extend the edge a bit farther than you need it.
Note...don't pick too much on the ugliness of these welds...and I fully know they are terribly ugly! You will note the weld on the left side went well and looks decent. The area currently being worked is not going that well...not pretty but functional. The reason for the difference? Remember when I said if you braze body work someone will be cussing it in the future. This is another example. The brass and brazing flux will never completely come off once you put it on, and it screws up any welding you try anywhere near it. The brass boils and spatters, making striking an arc tricky and the results splotchy. Welding is so easy...I just cannot fathom why you see so much brazing in body work!?!
Once the bead is on, grind it to shape, so it cannot be detected at all once the primer goes on.
Door is back on. Note the bottom edge should align with the relief in the sill.
It's better, but you can just see it is still a bit to large.
And up here is too close.
As it gets close, you are best to mark what you need. Funny how fast you can forget where and how much by the time you move the door from the car to the bench!
And the gap is good.
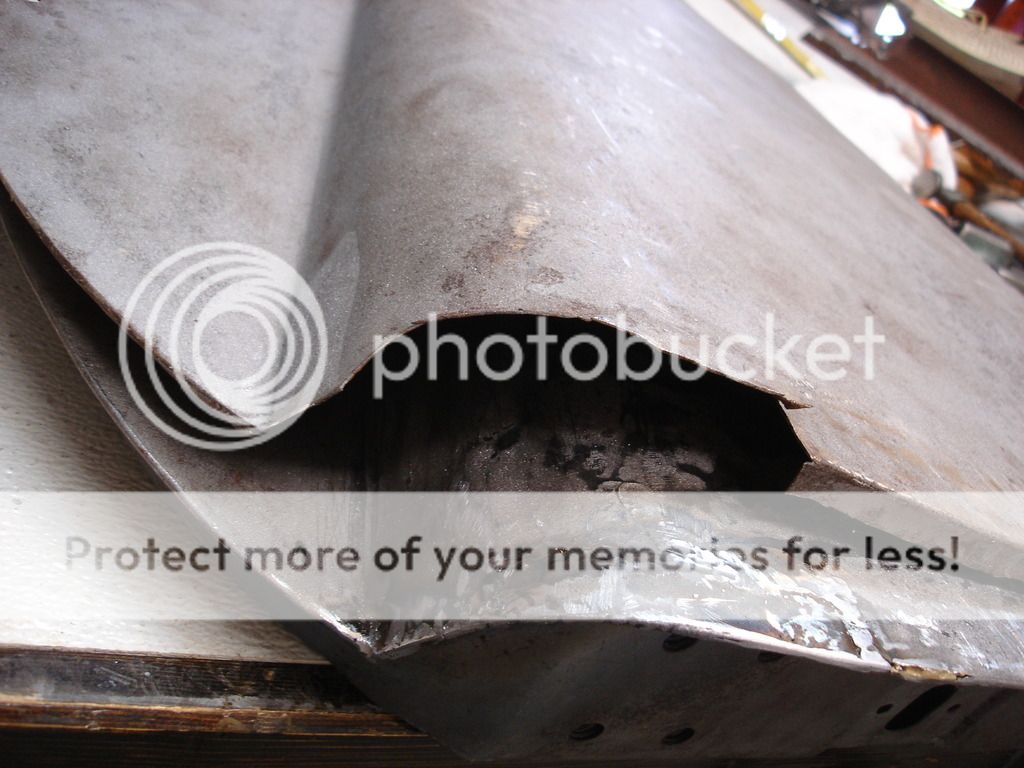
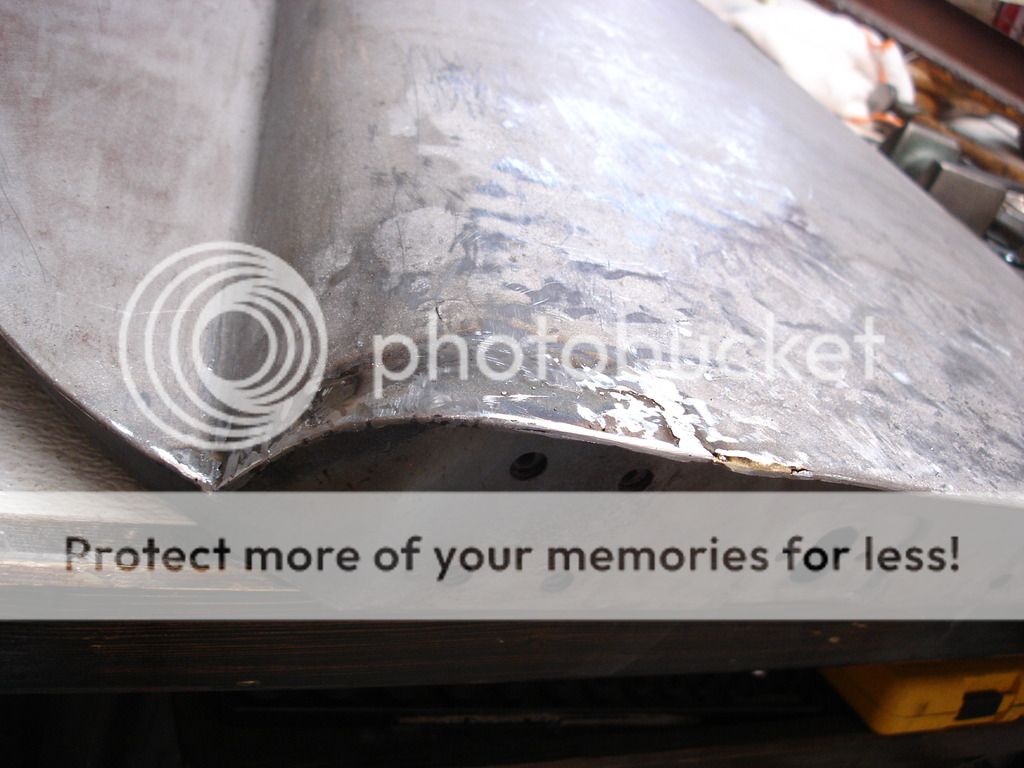
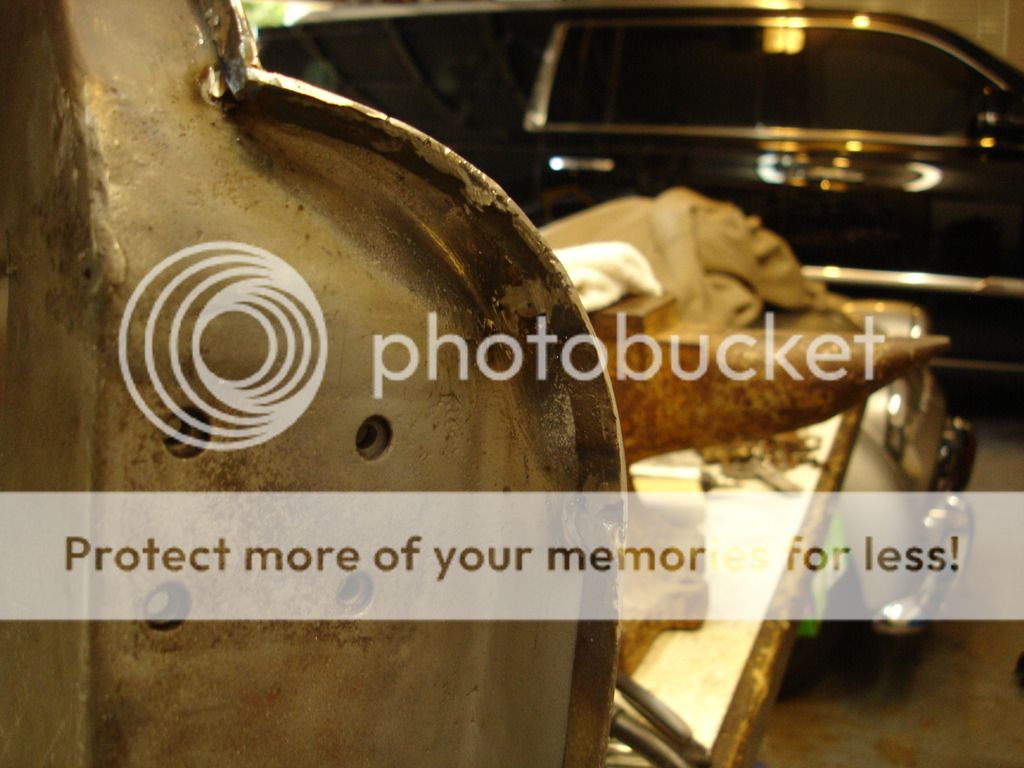
This drastically improved the shape of that corner, but when held up to the actual body, the contour was still off in this area. Steve, this is the question you asked in an earlier thread, about what to do to get the door gaps even and correct. Well...here's the process:
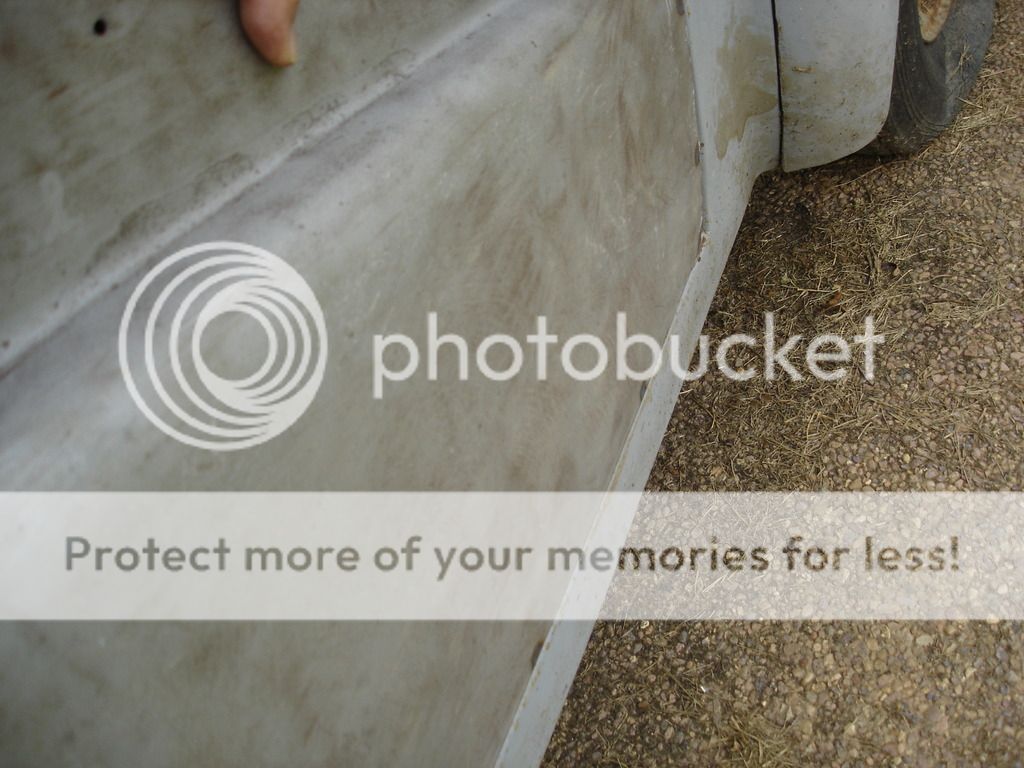
This is the door held in the opening. The bottom and rear look good.
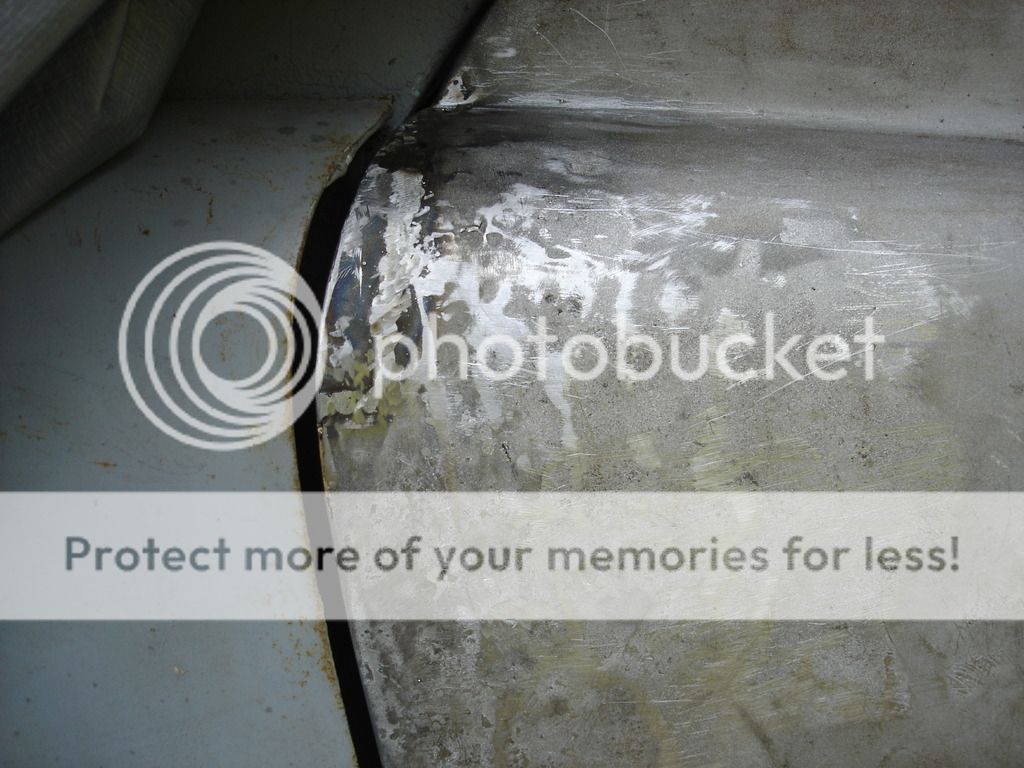
The problem is shown here. Remember the fender is not mounted back far enough, so I am not concerned with the size of the forward gap...but I am about it being even from top to bottom. As you can see...it is not.
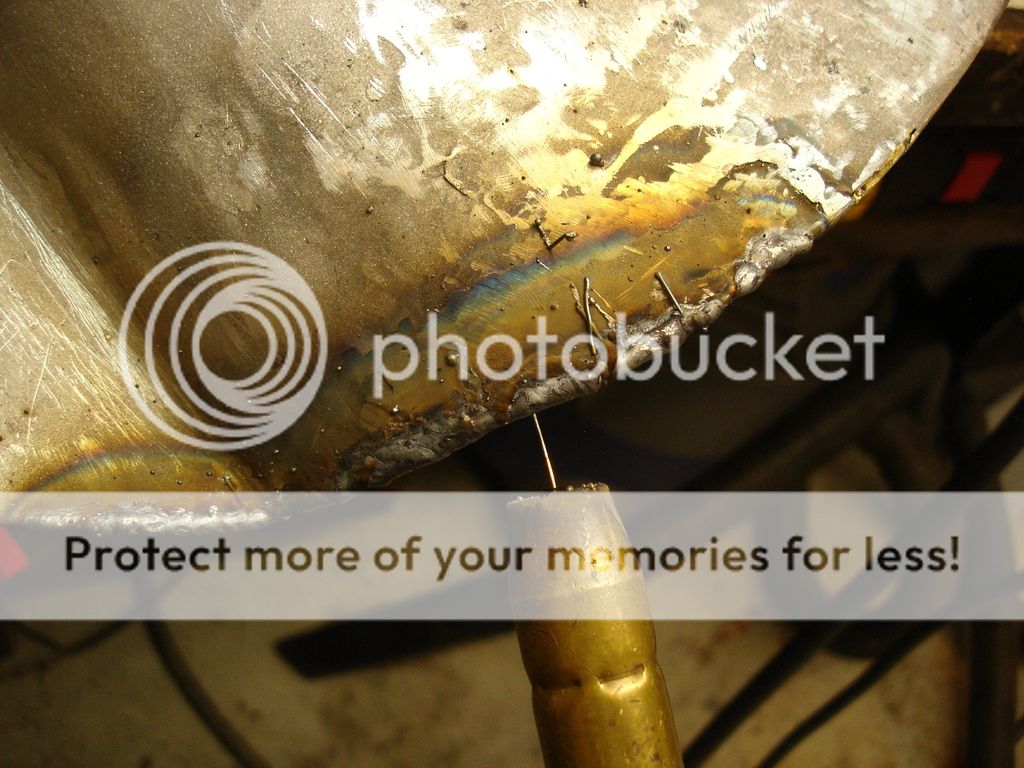
Here I am welding beads on the edge that is gapped to far. I am using .023" steel wire. On my Millermatic 185, the setting is at 1 (the lowest), and feed at 40FPM. Just add bead upon bead until you extend the edge a bit farther than you need it.
Note...don't pick too much on the ugliness of these welds...and I fully know they are terribly ugly! You will note the weld on the left side went well and looks decent. The area currently being worked is not going that well...not pretty but functional. The reason for the difference? Remember when I said if you braze body work someone will be cussing it in the future. This is another example. The brass and brazing flux will never completely come off once you put it on, and it screws up any welding you try anywhere near it. The brass boils and spatters, making striking an arc tricky and the results splotchy. Welding is so easy...I just cannot fathom why you see so much brazing in body work!?!
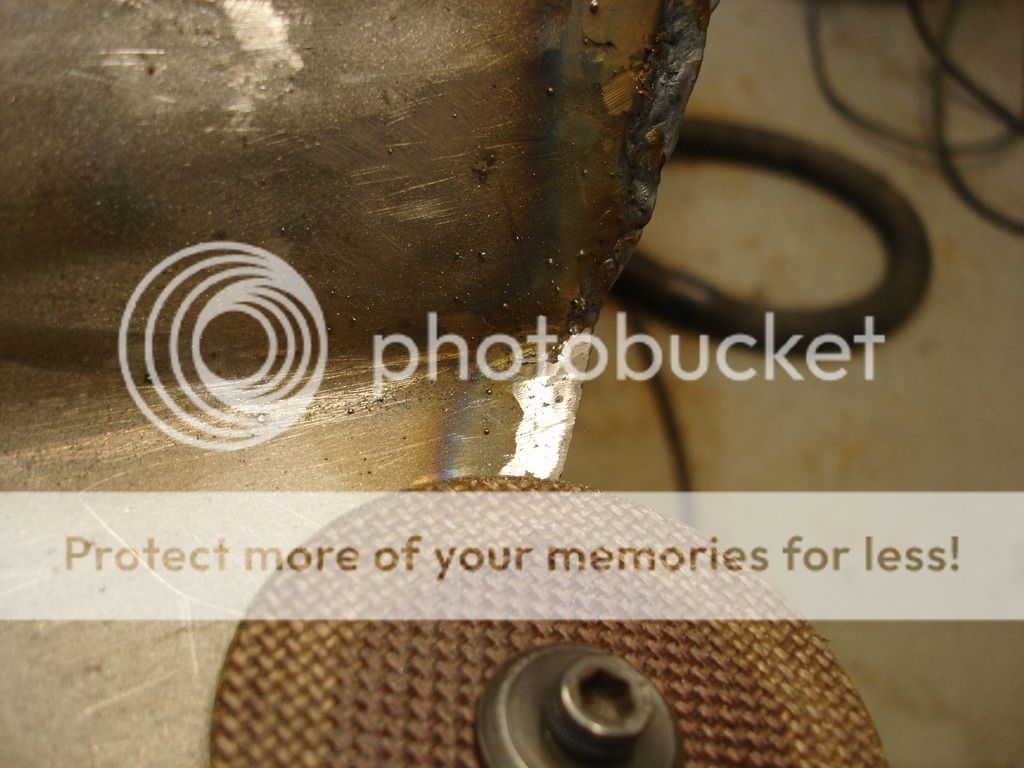
Once the bead is on, grind it to shape, so it cannot be detected at all once the primer goes on.
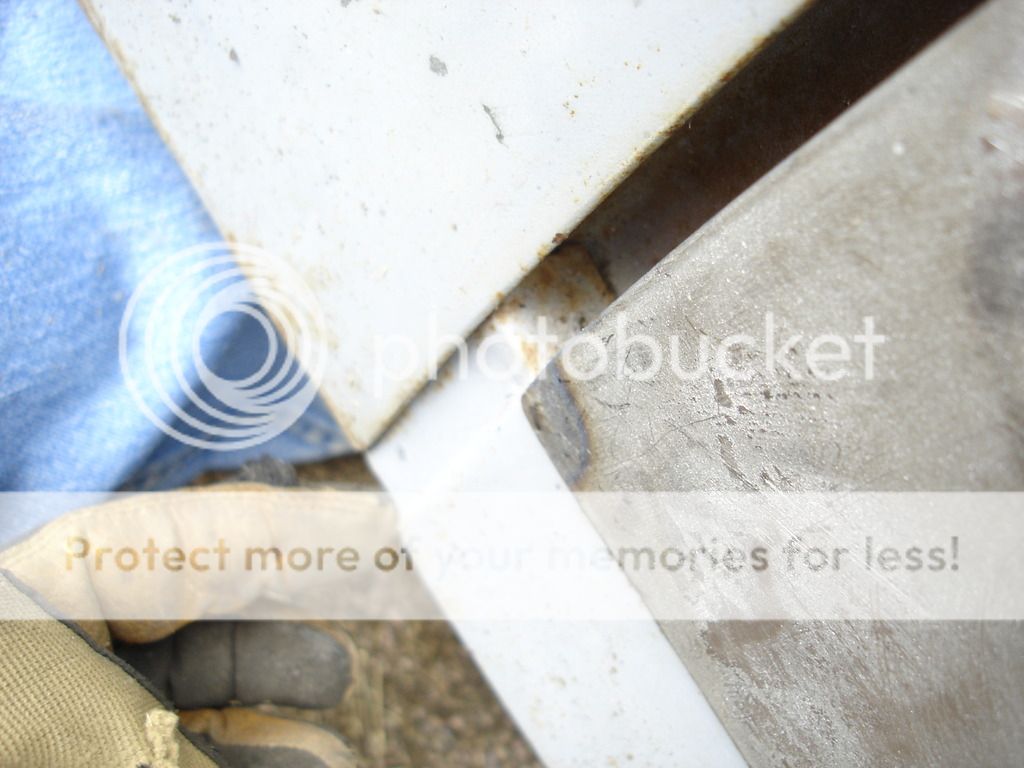
Door is back on. Note the bottom edge should align with the relief in the sill.
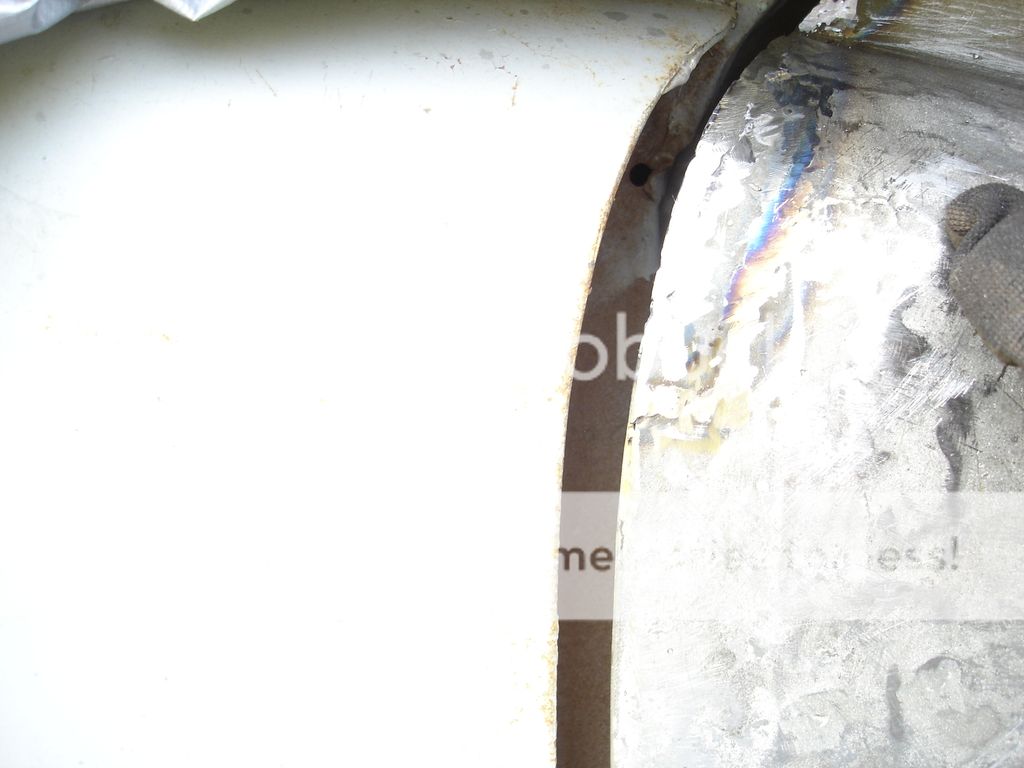
It's better, but you can just see it is still a bit to large.
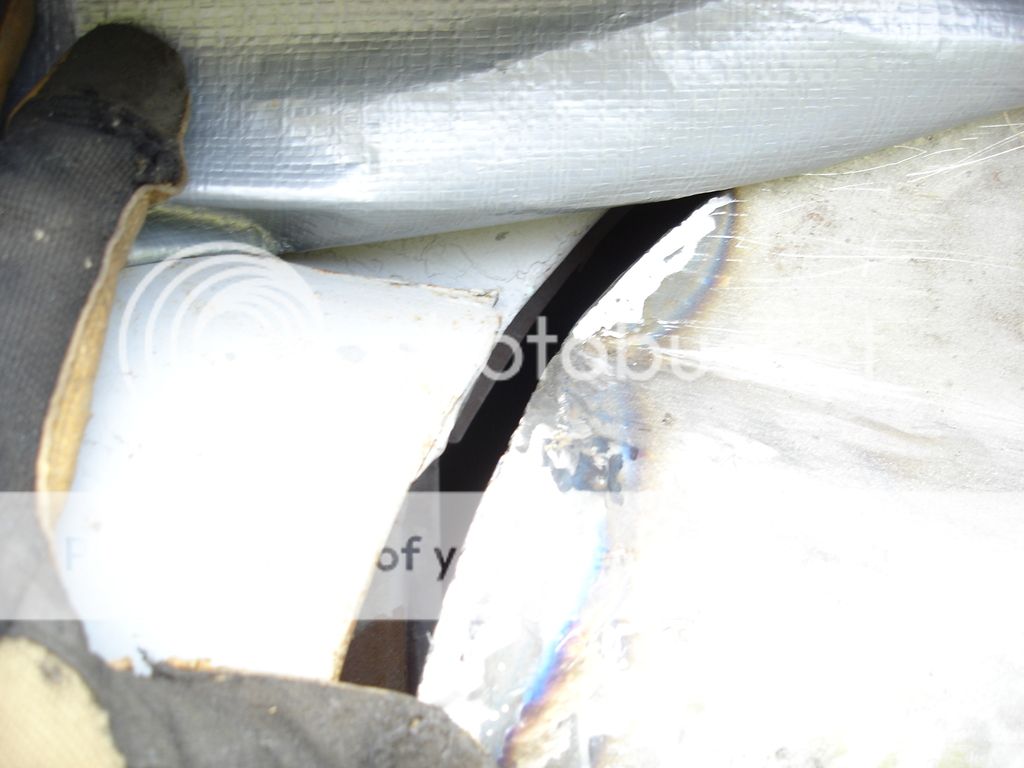
And up here is too close.
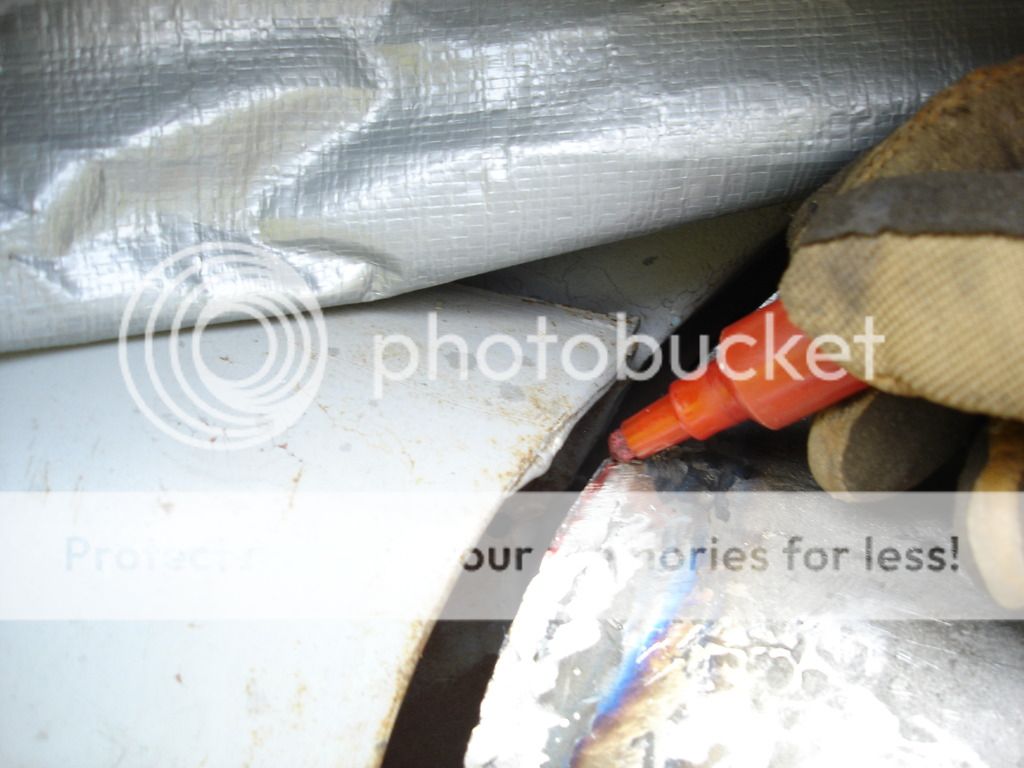
As it gets close, you are best to mark what you need. Funny how fast you can forget where and how much by the time you move the door from the car to the bench!
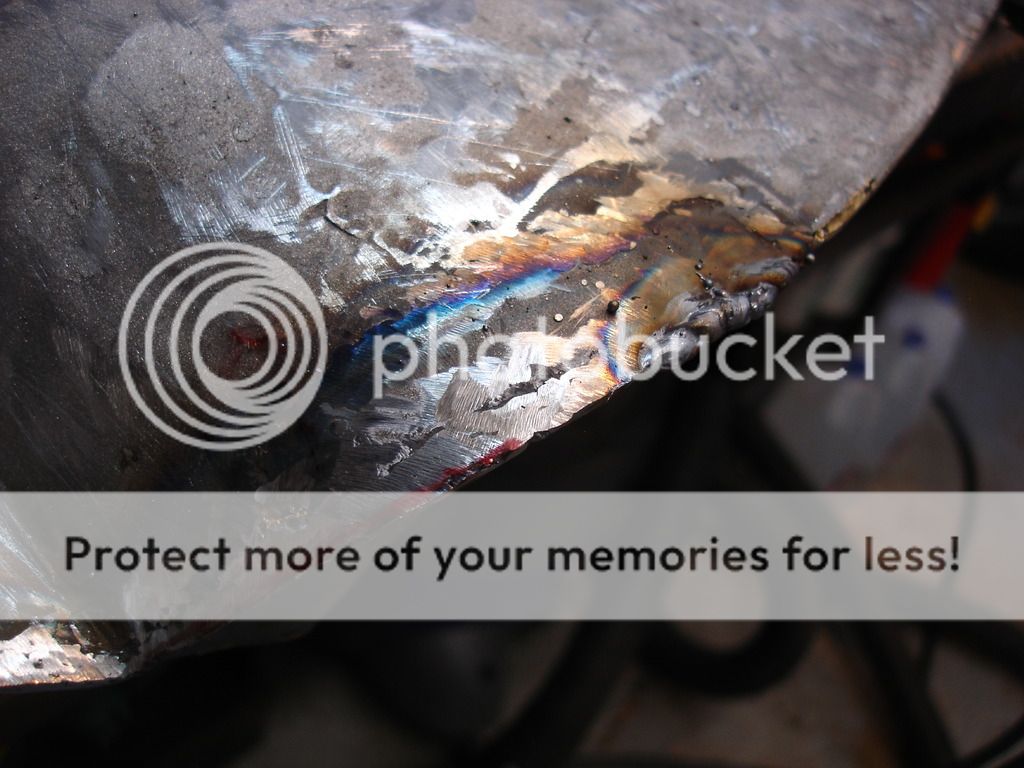
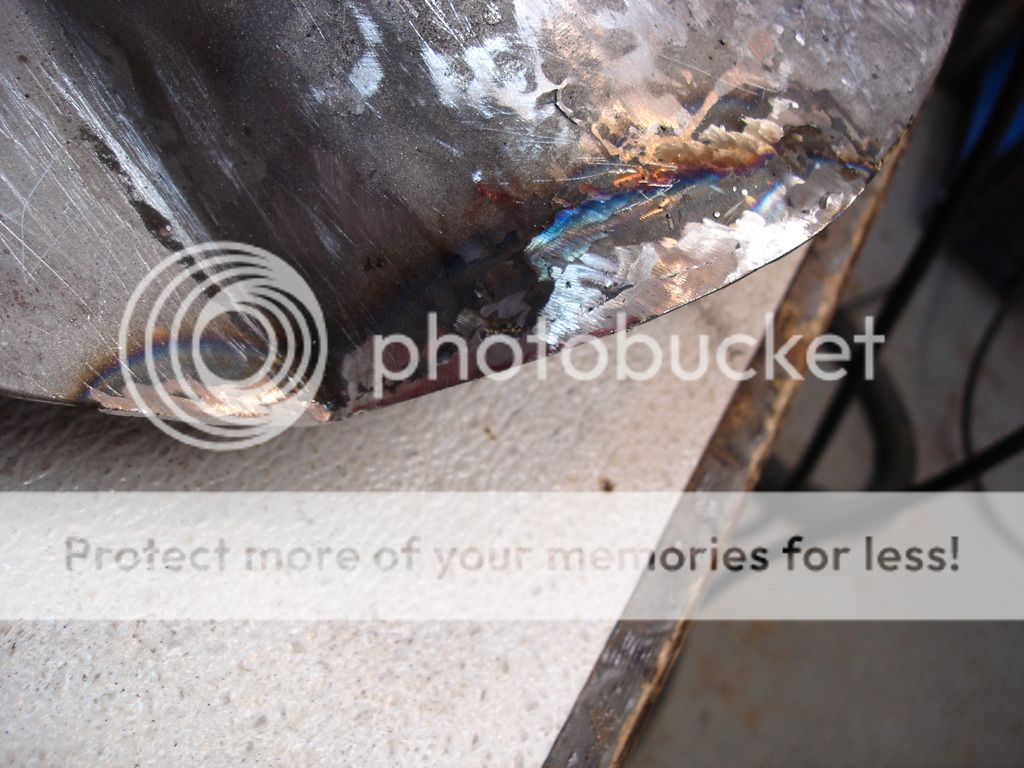
And the gap is good.
Last edited: