CJD
Yoda

Offline
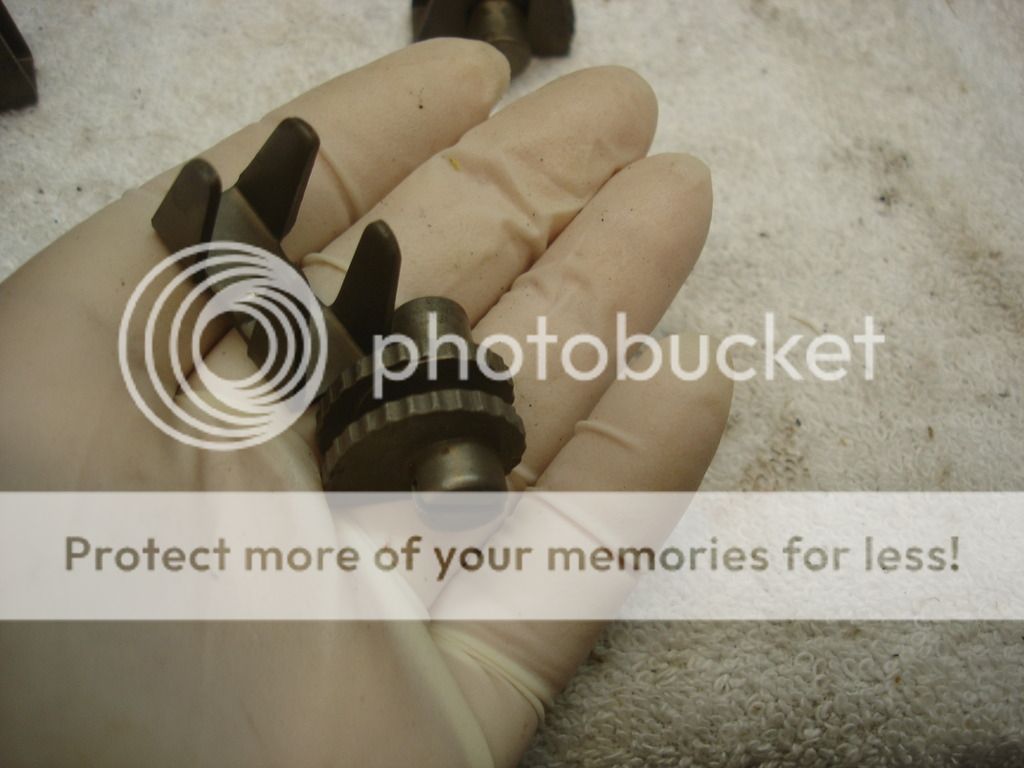
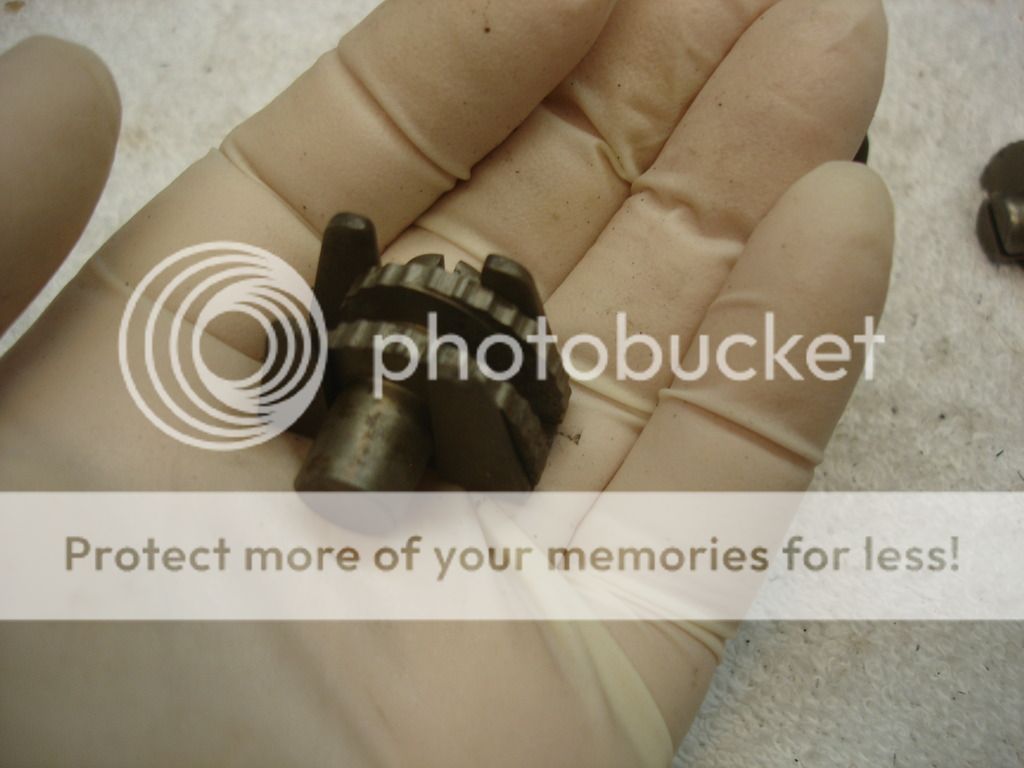
This odd little device is one of the 4 brake adjusters. What can I say, but, odd.
This brings up a point...the 2 cylinders with 2 adjusters up front leave a lot of possible issues with the TR2 brakes. You could lock up 2 cylinders (one left and one right) and still get brakes up front! You could also have a mechanic that thinks there is only one adjustment, and find your pedal goes to the floor even after he adjusts the brakes...
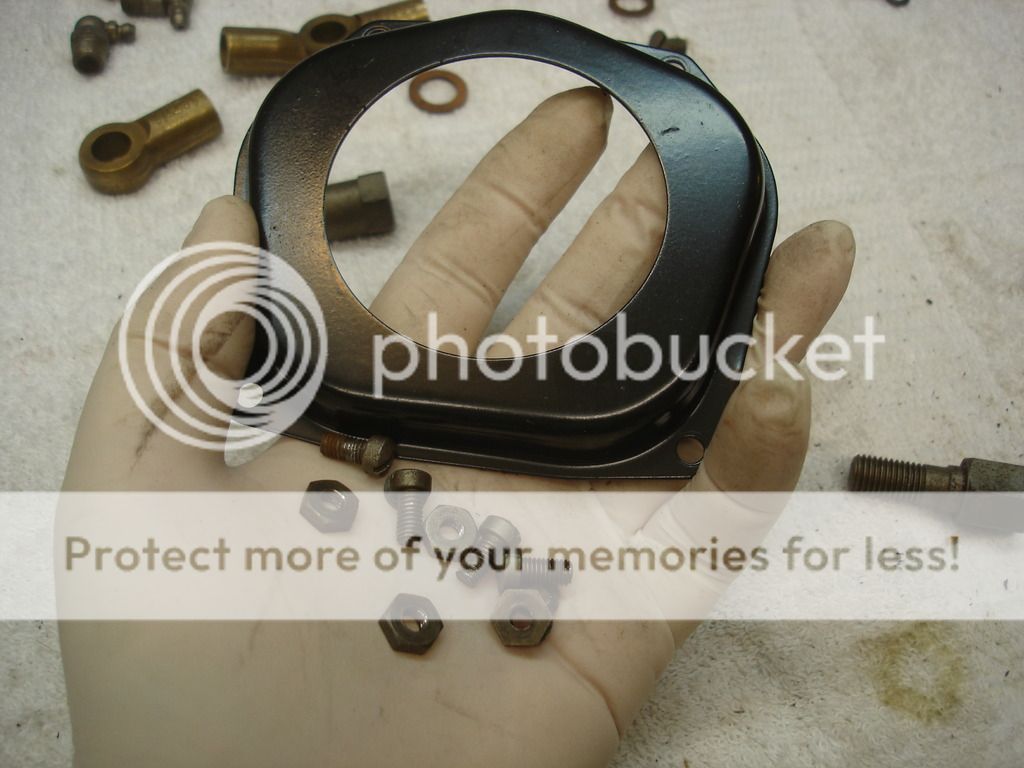
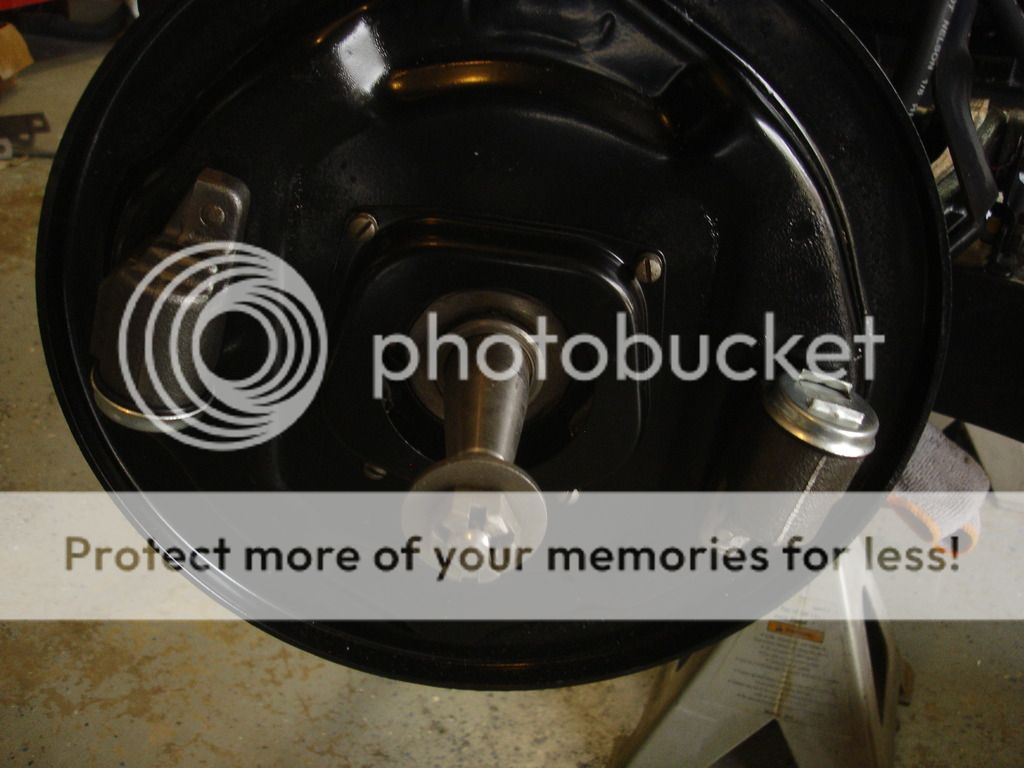
This is a grease catch. I guess they didn't trust the grease seal up front??

So, compared to single cylinder brakes, the TR2 brakes are a snap. Each shoe gets an adjuster, like so.
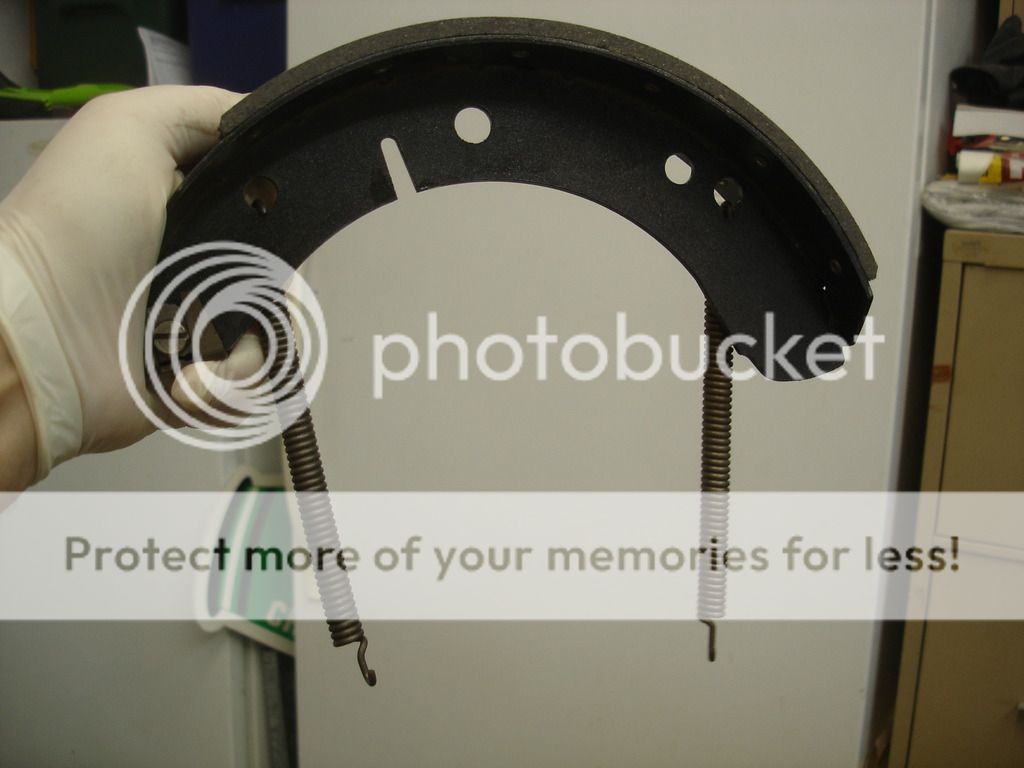
Now hang the springs down from a top shoe...rather a shoe you plan to use at the top, as they are all 4 the same.
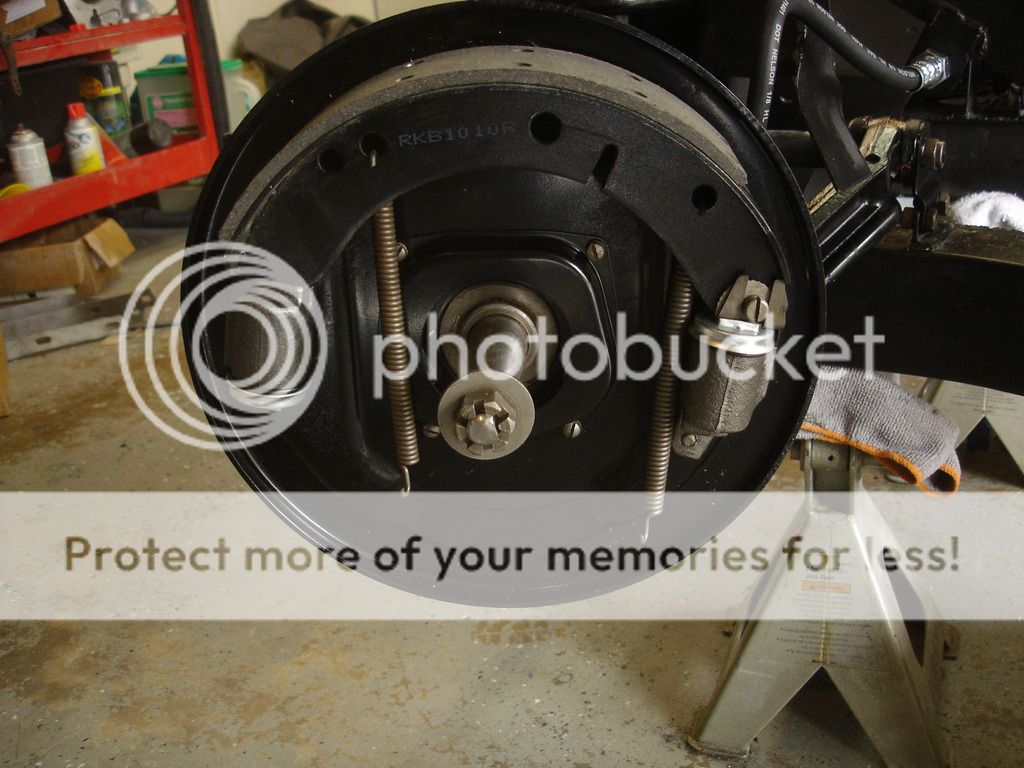
And set the assembly resting on the 2 cylinders.
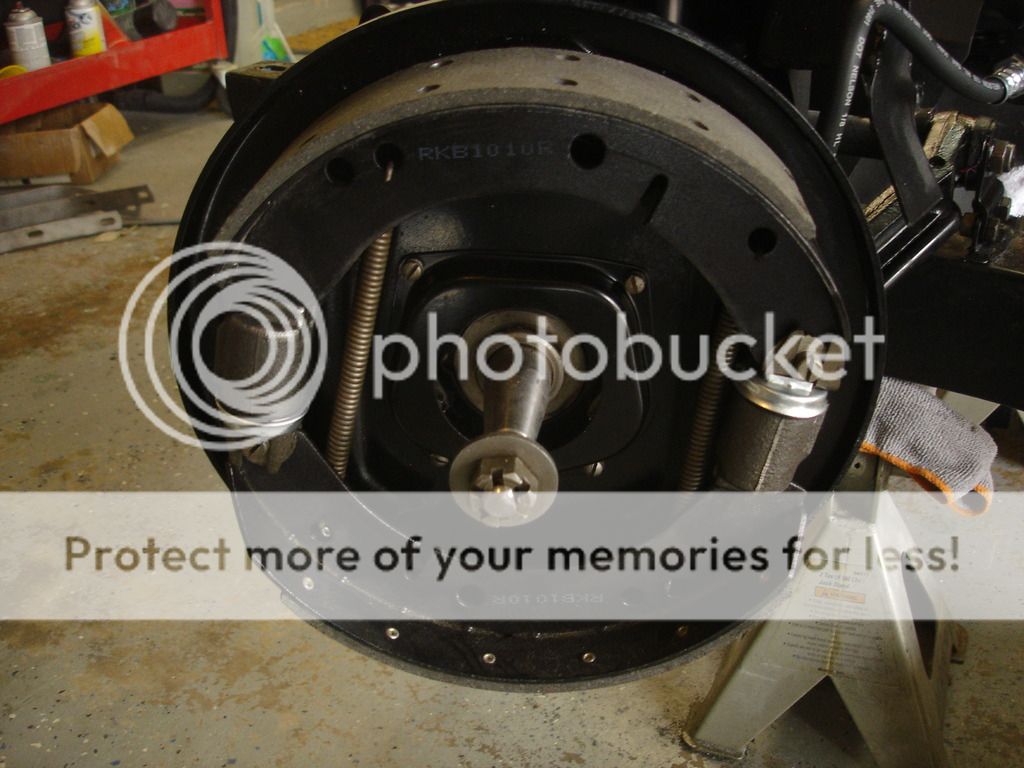
Then hook the bottom shoe to the springs...and push it into place. You're done! At this point the springs are pretty loose, until we adjust the play out with the adjusters.
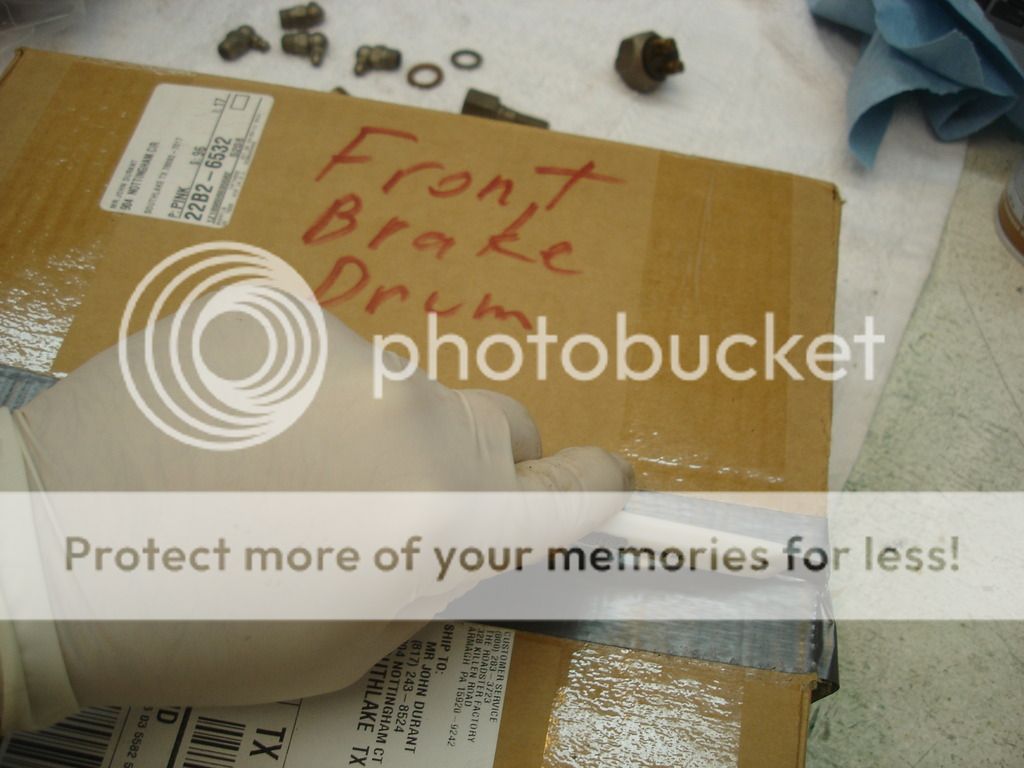
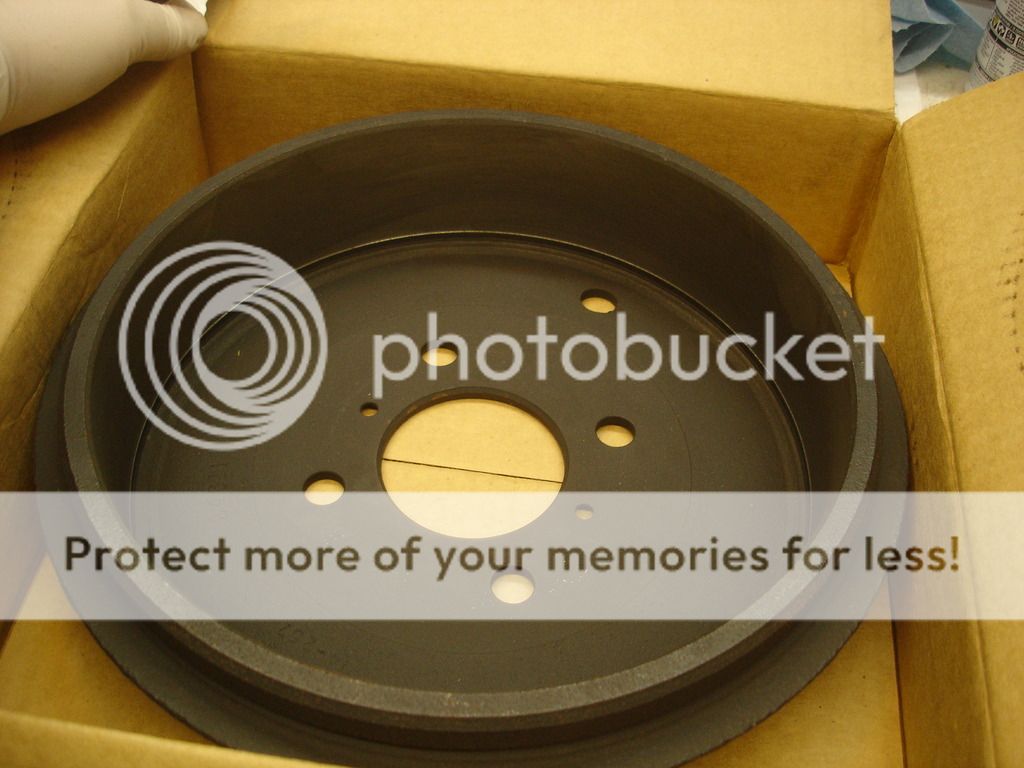
Another 60 year old new part!
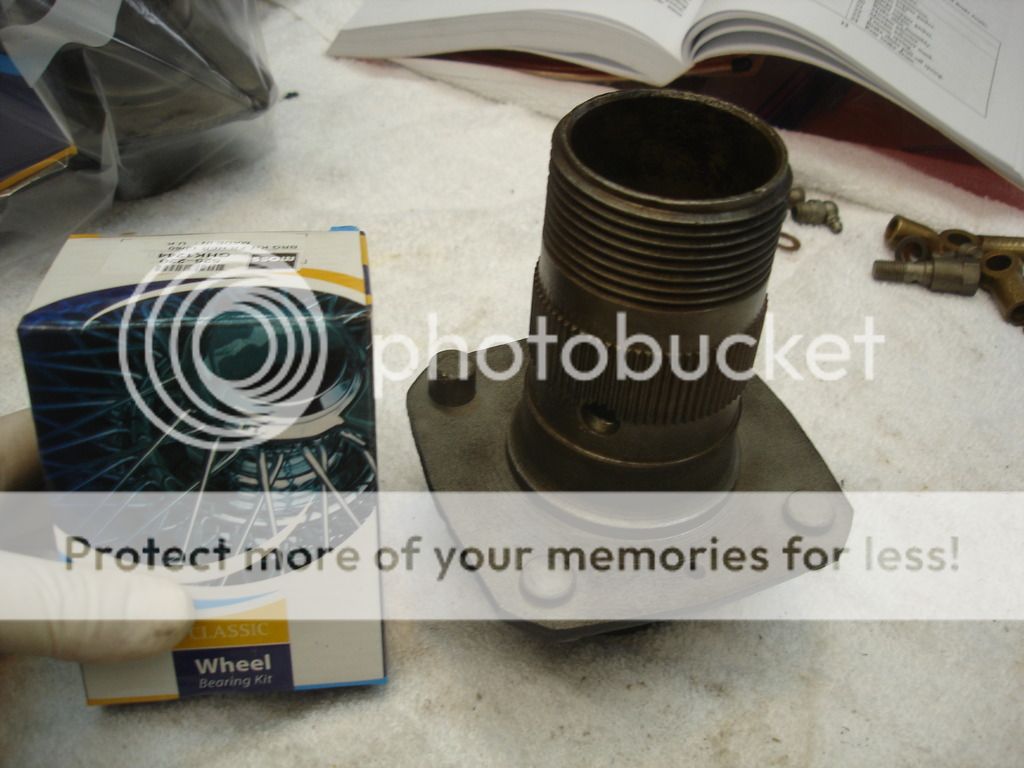
Here's another unique part...the wire wheel TR2 front hub. Remember they have unique sides too! I forgot and had to do the first hub twice! RH threads go on the left side, and LH on the right. Very important.
I'll be quiet and let you follow along for the assembly...
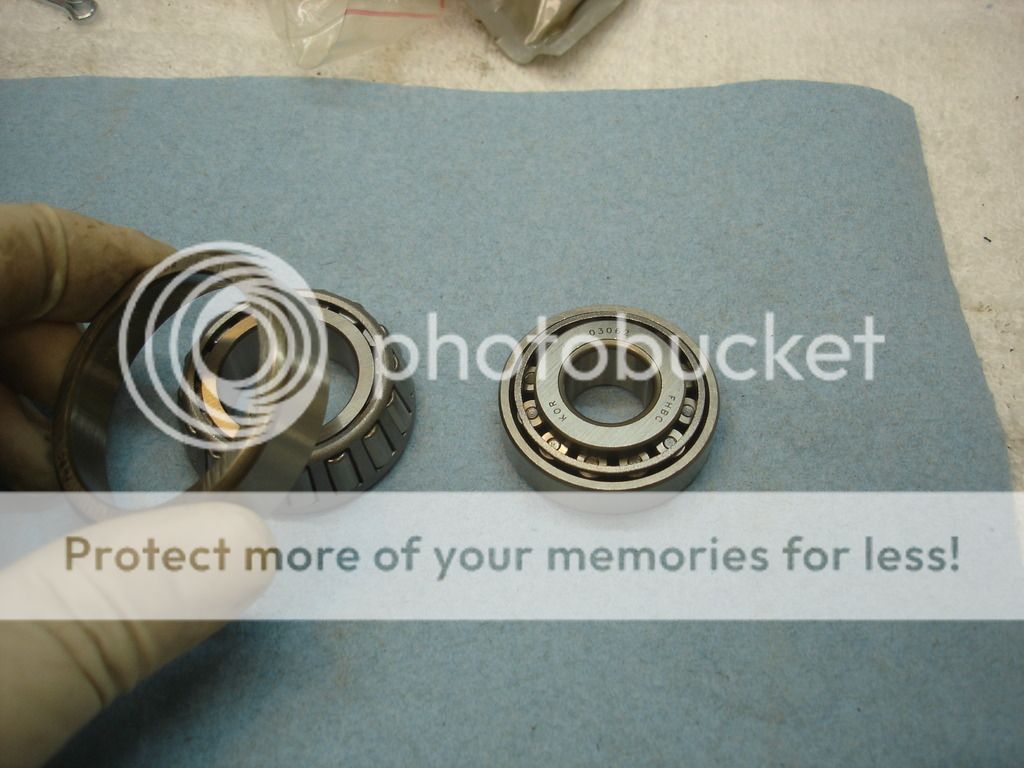

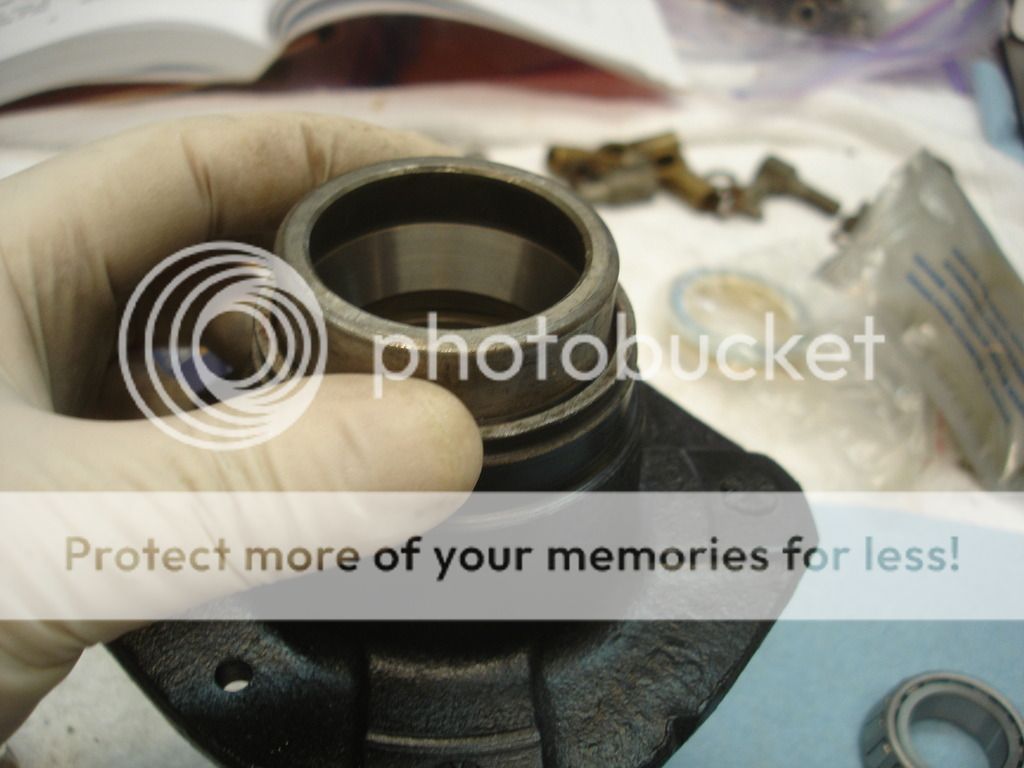
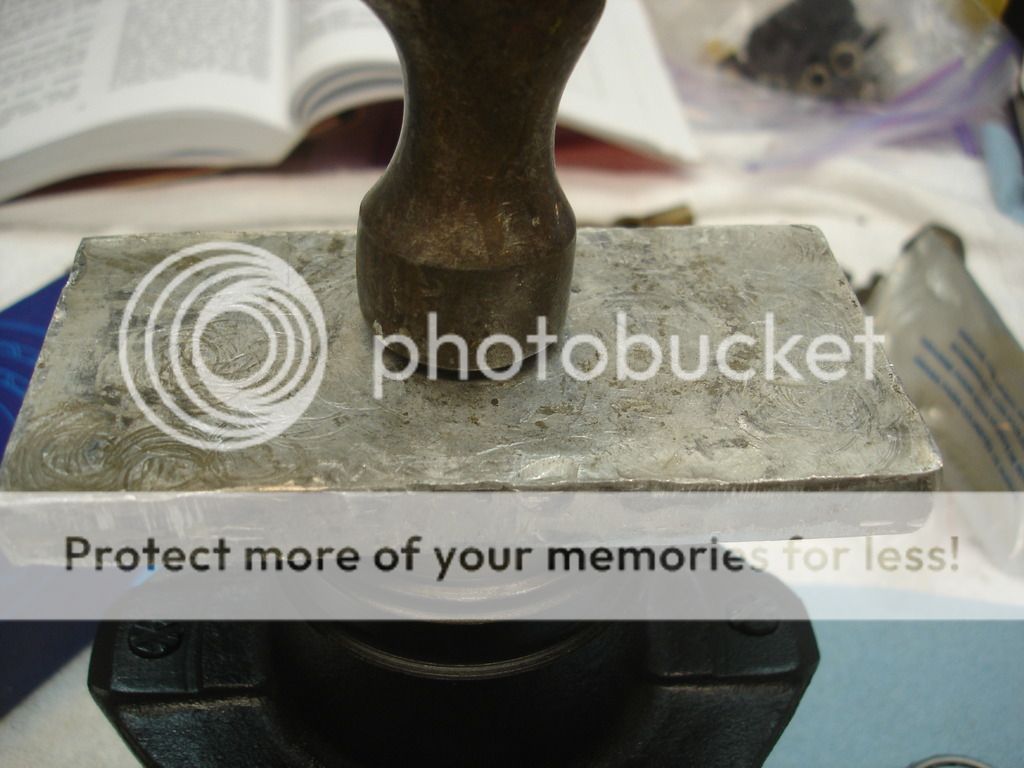
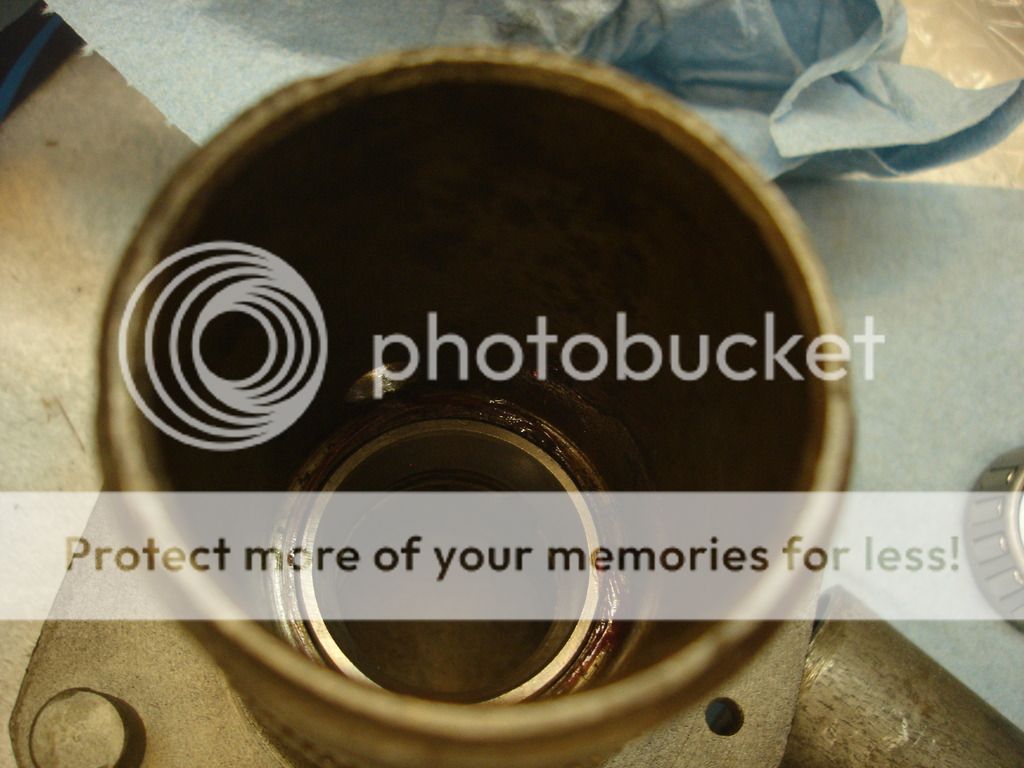
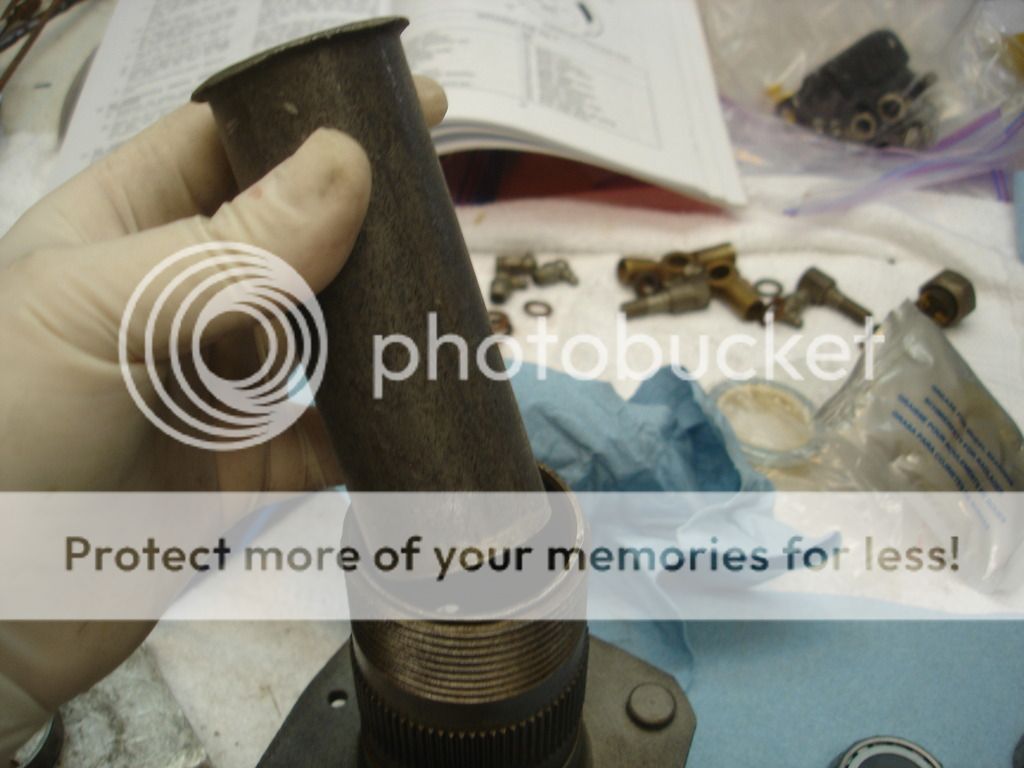
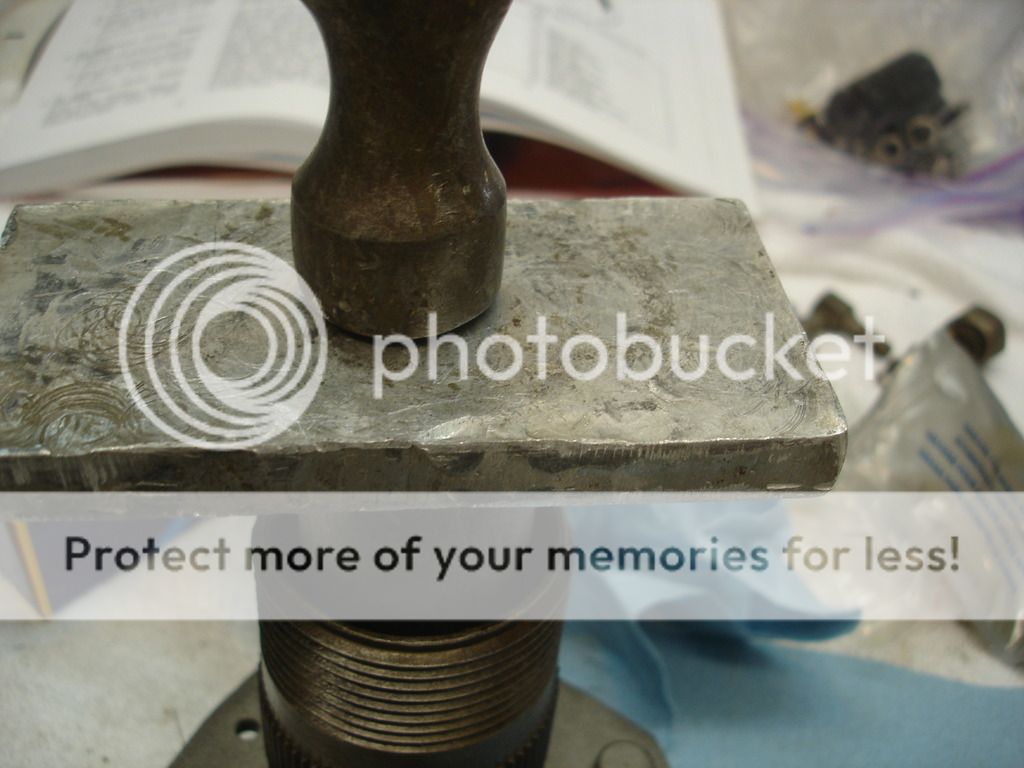
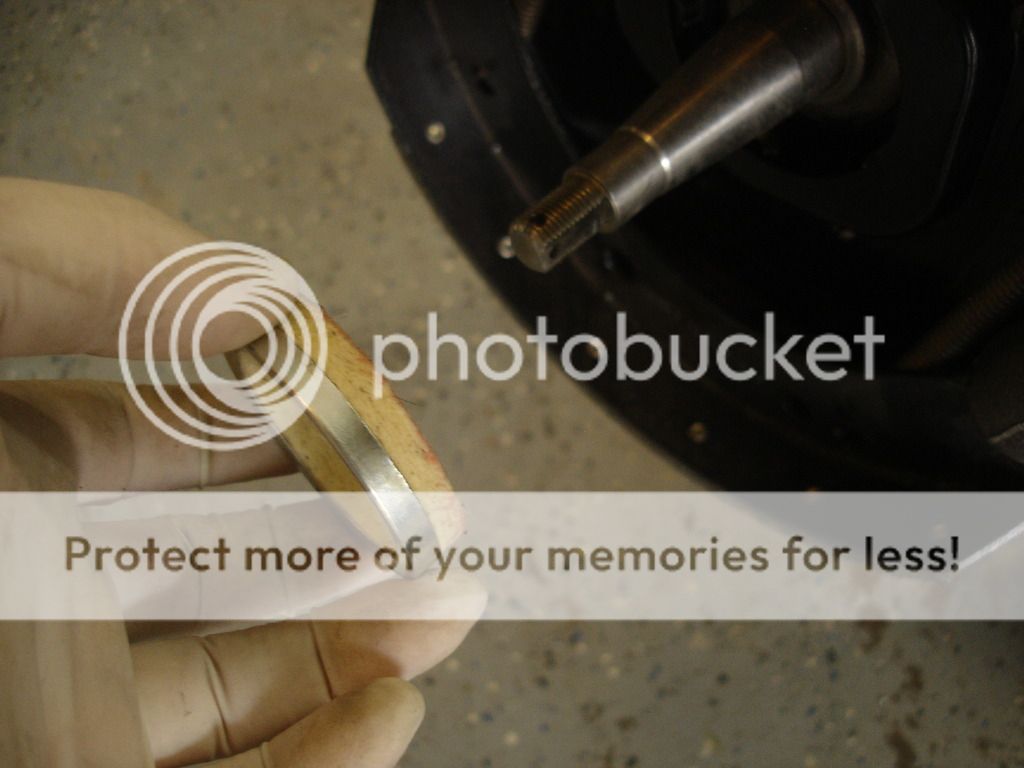
OK...can't be quiet here. I've read many, many posts complaining about the felt seals being to thick. Nonsense. If you follow the instructions in the manual, the felt will comply and fit right in...just as it is supposed to.
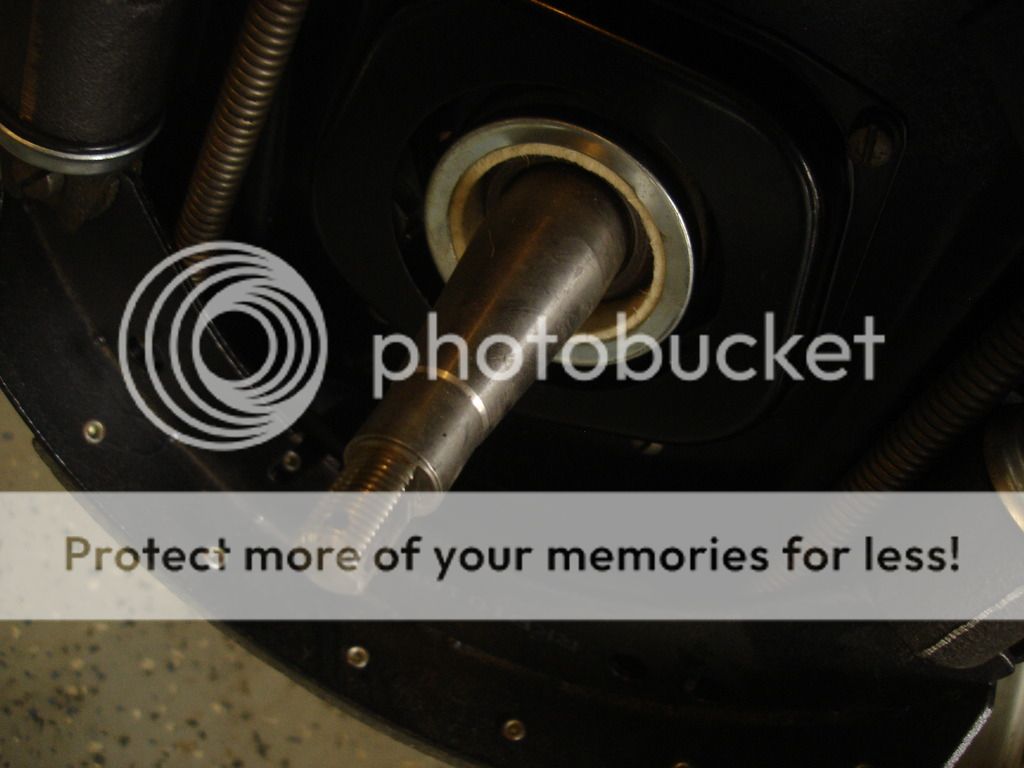
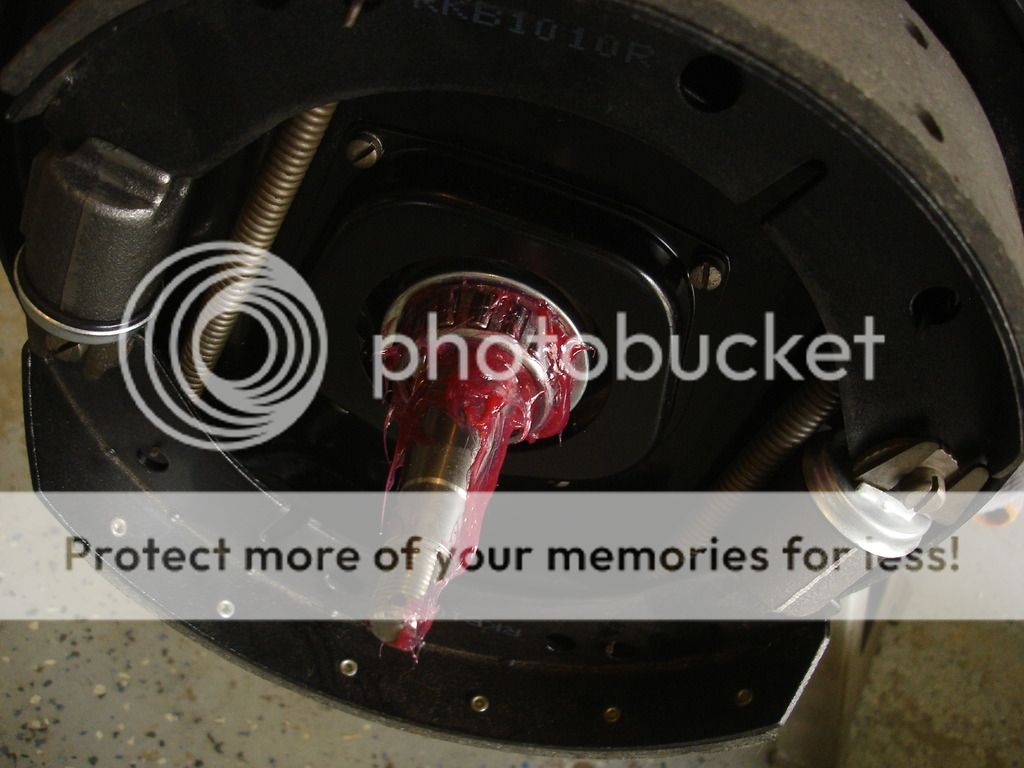
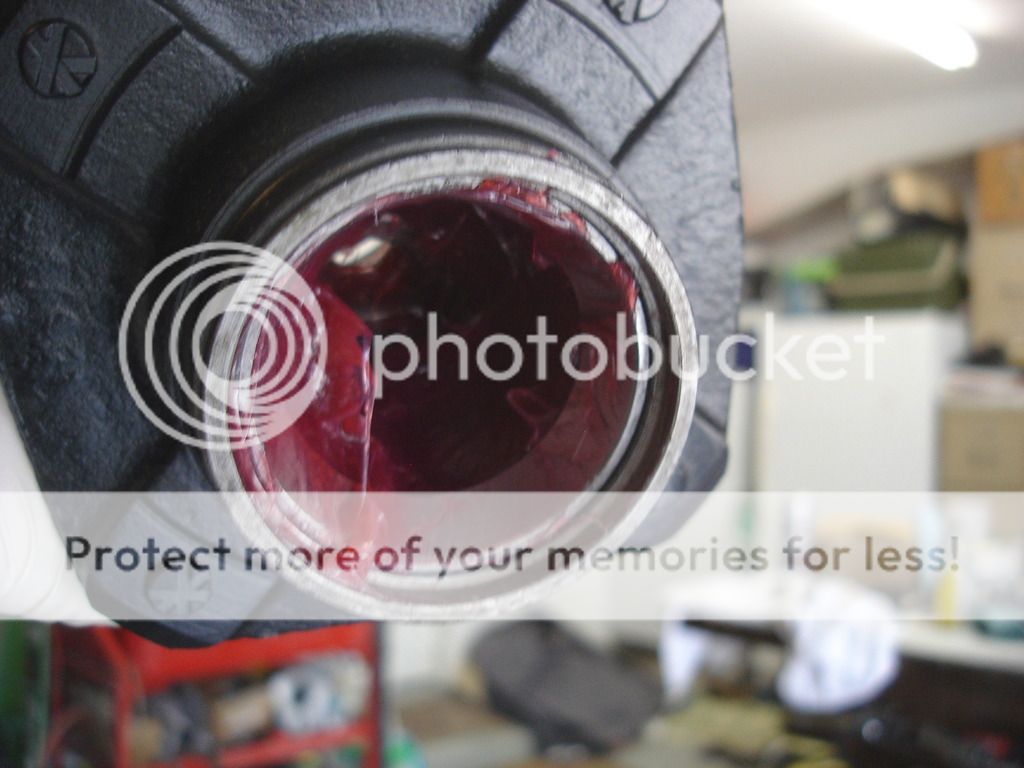
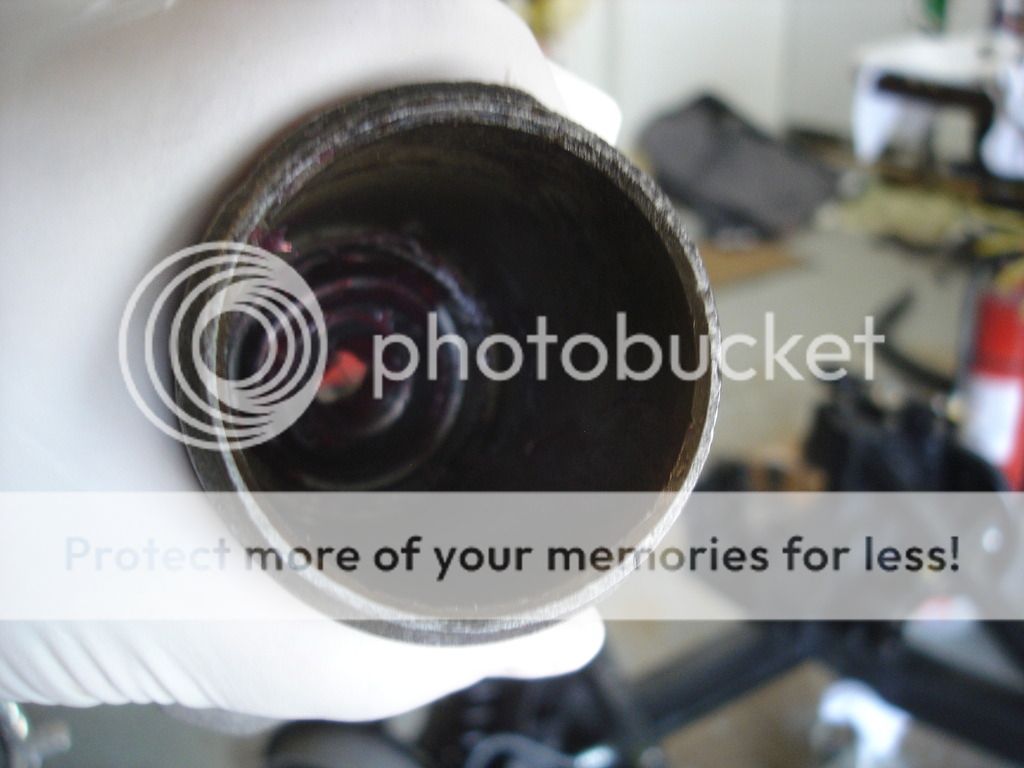
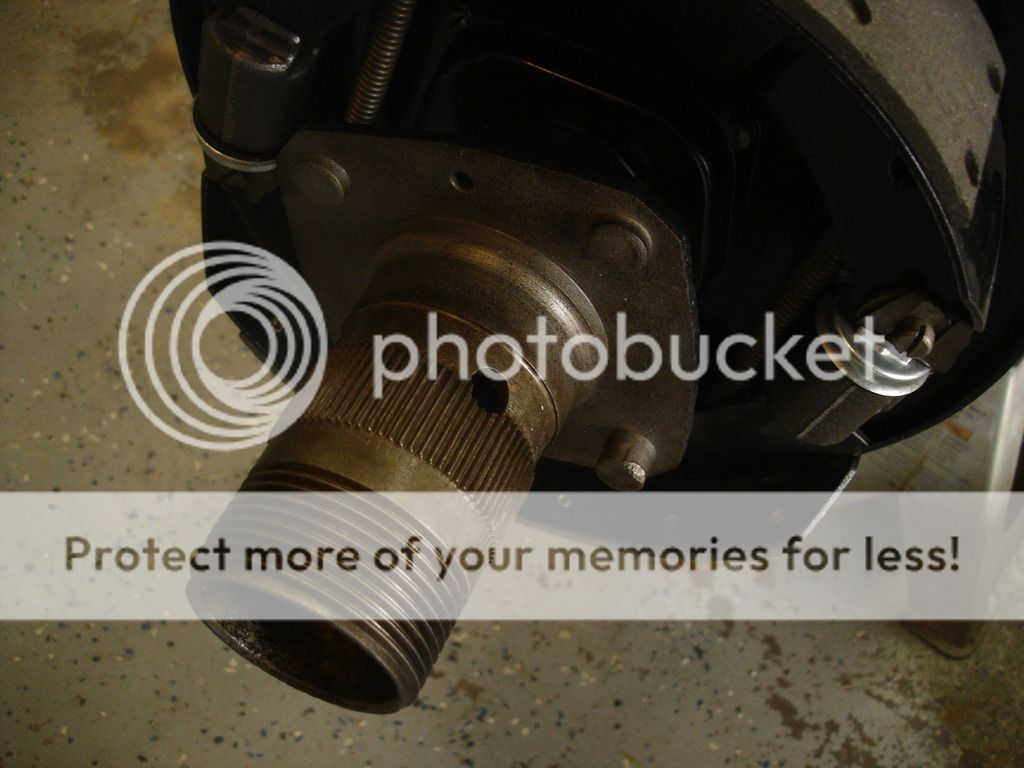
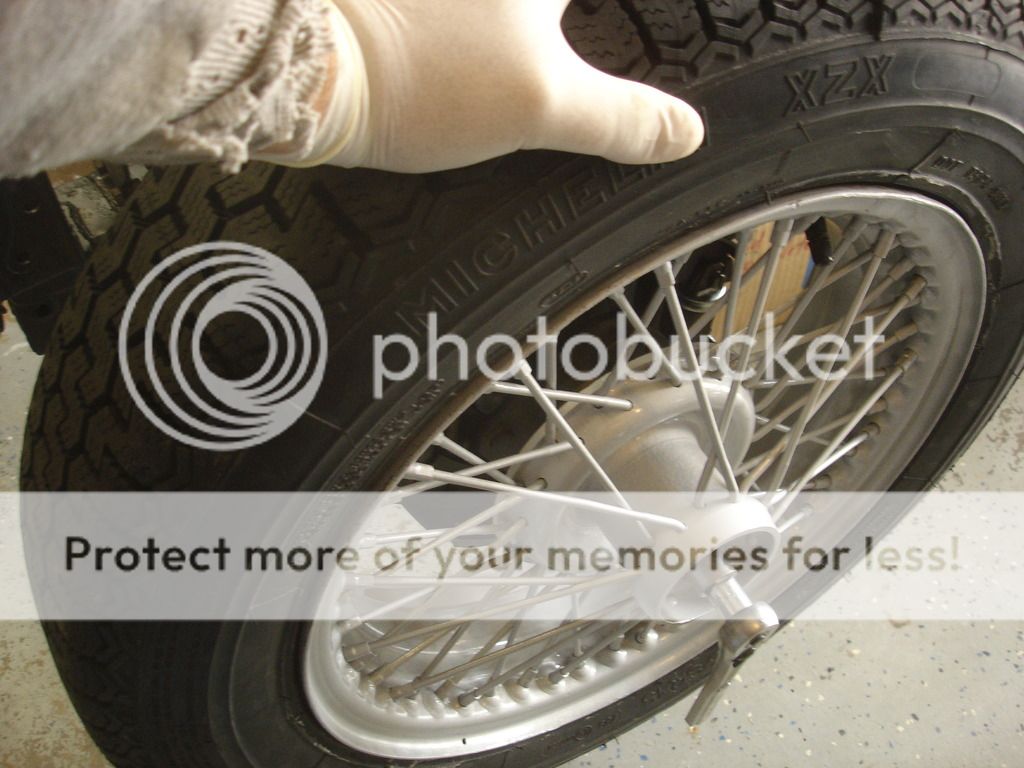
Stop here for a second...this applies to all TR's!! If you read the manual, it tells you to torque the nut to 10 ftlbs. Notice I put a wheel on to do this. Straight from basic high school shop class...always rotate the bearing while you tighten it!! This does several things at once. Namely, it allows the bearings to seat without catching on any ridges, it allows the grease to displace so you don't get a false torque reading, AND...most importantly...it collapses the felt seal!!
The seal starts so tight that it makes it impossible to turn the hub while you are torquing the bearings to 10. Thus the need for the wheel. Of note...once I finished the process, I can hand spin the wheel and it will turn for 3 turns, no problem. The felt seal complies to the metal...as it was intended to do.
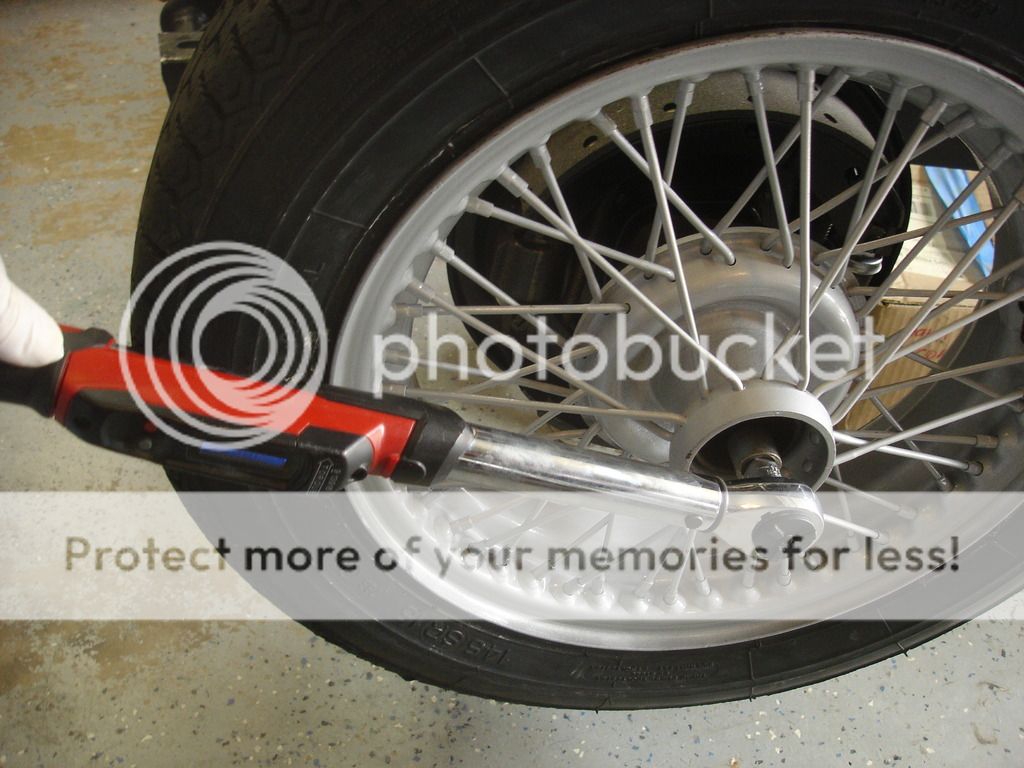
So, I turned the wheel, and the wrench, slowly...until I got the click.
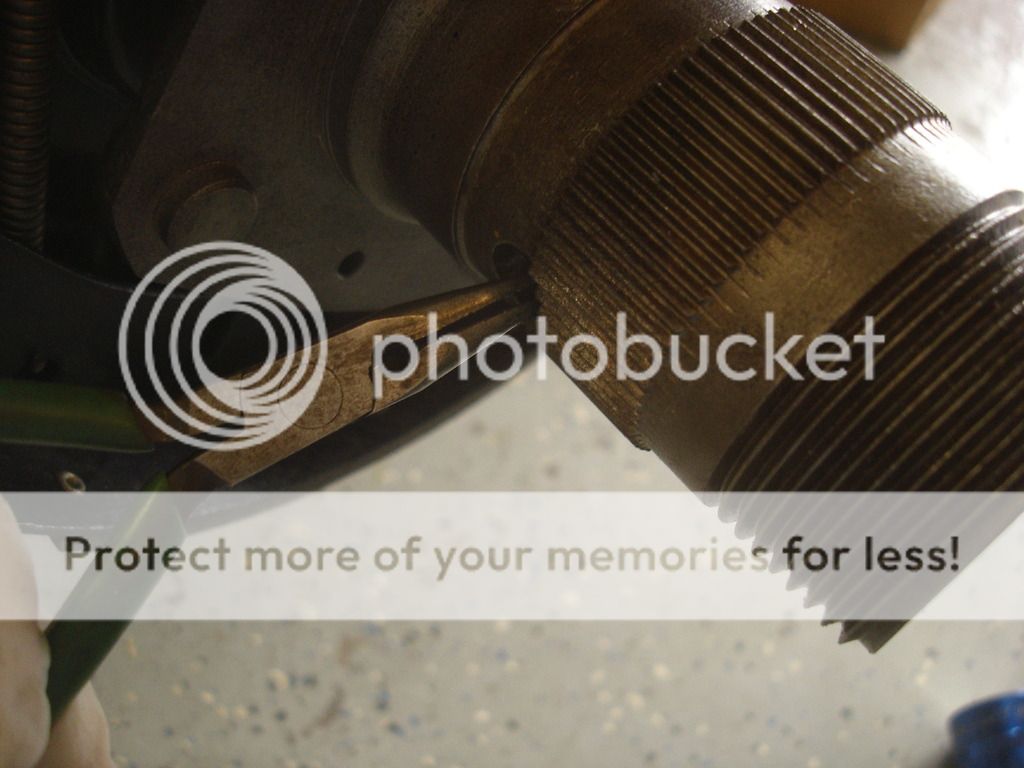
Once the torque is set, back off the nut 1-1/2 flat, and look for the cotter key hole through this little hole Triumph provided in the hub. Turn the nut up to another 1/2 flat until the holes line up.
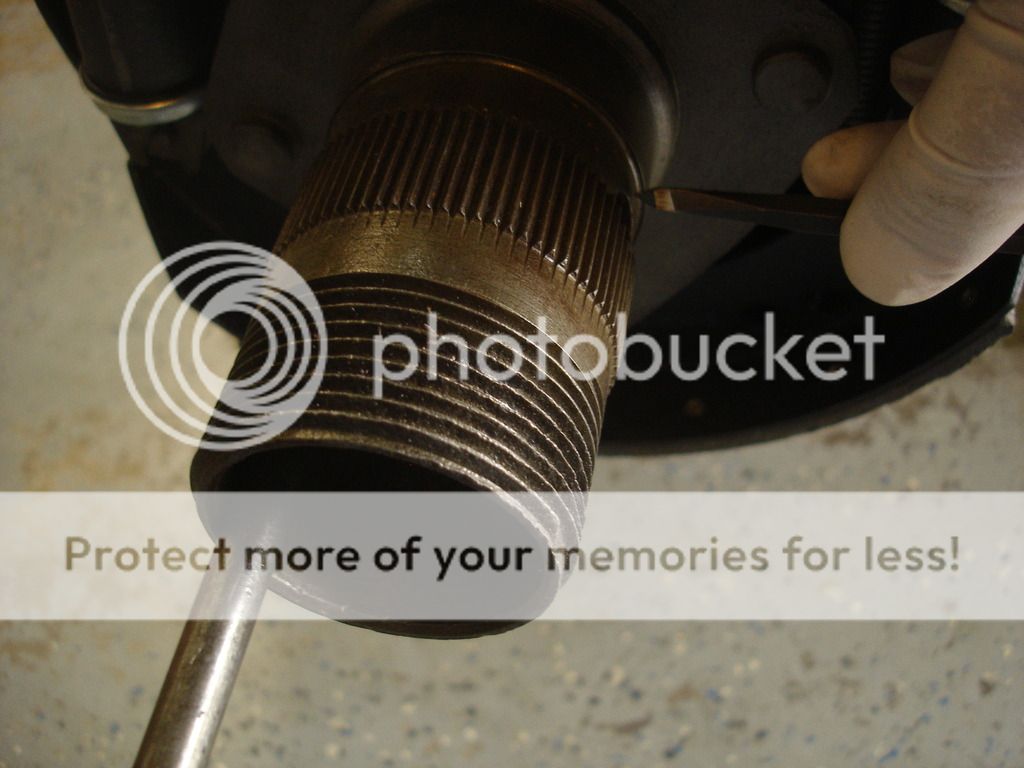
Here I am holding the key in the nut with a large screw driver while I use a chisel to spread the key.
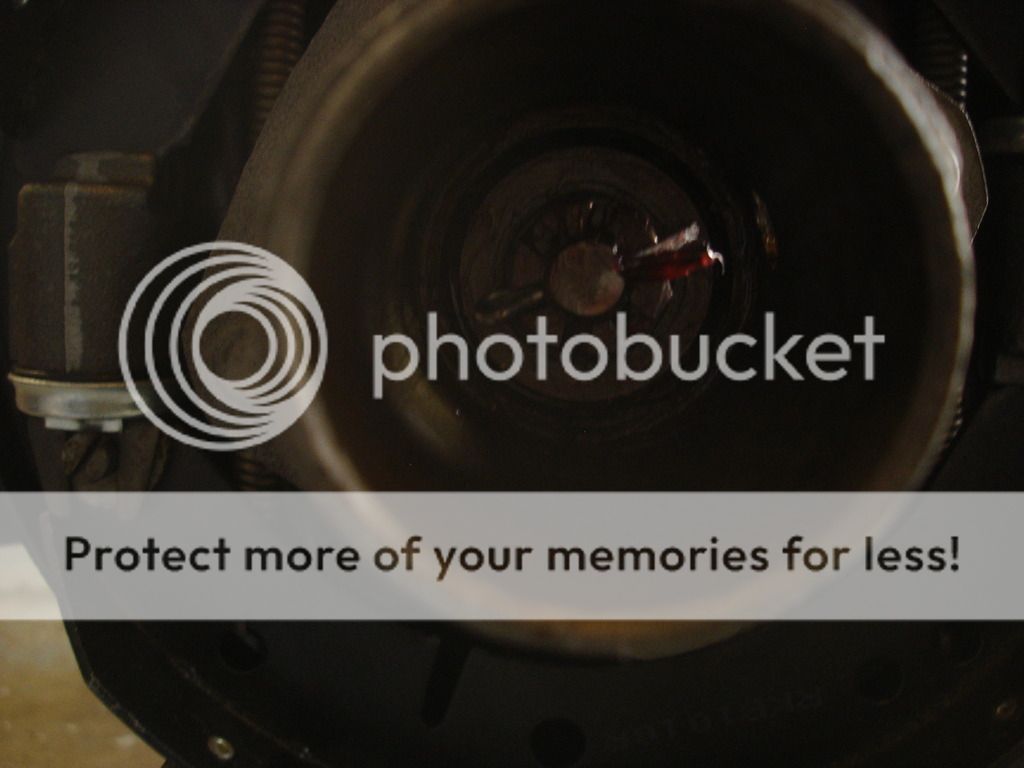
Notice I don't care that the key is not bent all the way over. Just open is enough, as the key does not turn and therefore has no force trying to sling it outward. Plus, when bent over getting it back out of this tight hub would be near impossible!
Gotta stop here, as I have to go to work...real work. I know. I hate it when real work gets in the way of fun work.
More soon.