bthompson
Jedi Warrior
Offline
I spent another couple hours before work today, to separate tranny from engine.
The first thing to do is take the bellhousing off. This is really straightforward: take the starter out, and about 10 bolts around the circumference...
...and then pull it straight out. I didn't know what to expect, so I was surprised at how easy this part was.
Hmm. Looks like some wear around the clutch fingers. New clutch is a good idea, it seems.
Peeking at the clutch face shows some thickness. I don't know how much there's <span style="font-style: italic">supposed</span> to be, but the finger wear is hinting to me that it's time for new stuff anyhow.
Inside the bellhousing, showing the five bolts that hold it onto the transmission. Apparently, I have a roller release bearing?
The bellhousing did <span style="font-style: italic">not</span> want to come loose. Resting it upright on its input shaft and tapping the bellhousing helped, (although I was very uneasy about doing it.) Expect an oily mess if you do this. :laugh:
Ooooh, a bad sign. Mangled bearing race.
The gearbox is <span style="font-style: italic">literally</span> as big as my hand. Everything about these cars are <span style="font-style: italic">cute</span>--even the grimy bits.
And that's all I had time for today. The transmission is sitting in my trunk right now, waiting for a leisurely inspection.
The first thing to do is take the bellhousing off. This is really straightforward: take the starter out, and about 10 bolts around the circumference...
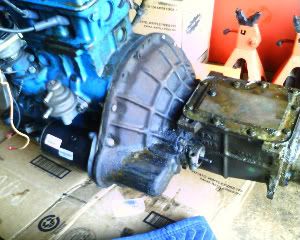
...and then pull it straight out. I didn't know what to expect, so I was surprised at how easy this part was.
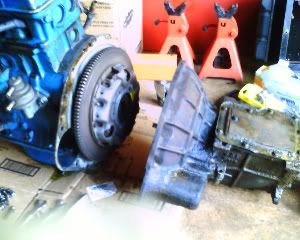
Hmm. Looks like some wear around the clutch fingers. New clutch is a good idea, it seems.
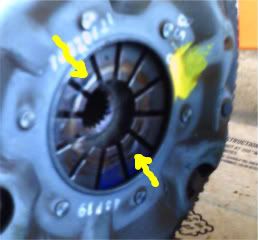
Peeking at the clutch face shows some thickness. I don't know how much there's <span style="font-style: italic">supposed</span> to be, but the finger wear is hinting to me that it's time for new stuff anyhow.
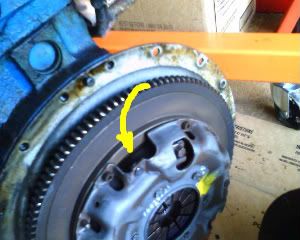
Inside the bellhousing, showing the five bolts that hold it onto the transmission. Apparently, I have a roller release bearing?

The bellhousing did <span style="font-style: italic">not</span> want to come loose. Resting it upright on its input shaft and tapping the bellhousing helped, (although I was very uneasy about doing it.) Expect an oily mess if you do this. :laugh:
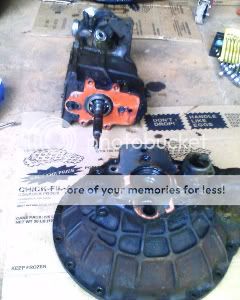
Ooooh, a bad sign. Mangled bearing race.

The gearbox is <span style="font-style: italic">literally</span> as big as my hand. Everything about these cars are <span style="font-style: italic">cute</span>--even the grimy bits.
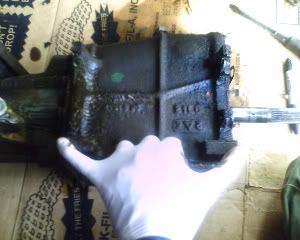
And that's all I had time for today. The transmission is sitting in my trunk right now, waiting for a leisurely inspection.