Week 26
Well. This week marks an entire half year, just on bodywork. A milestone, although not a particularly good one.
As I left last week, I managed to come up with a tentative game plan for the tub. It envolves using the front cowl from the original car...since I was raised working on American metal, I'll refer to this as the front clip. Then, I will use the rear clip from the donor car. Finally, most of the metal in the middle will be new.
Sounds simple...if only it were simple.

This is a view of the battery box on the TR2 tub. I started removing it 3 years ago, and was so totally disgusted with the situation that I quit. 3 years later I am finishing the removal. The battery box in the donor car is intact, but it looks like some home made affair, and it was welded in to well to make removal easy. I will spring for the $58 for a new box.
Here, and the next few pics I am taking measurements so I can duplicate the series of holes that are in the original box. Also, the little "T" wire loom holders do not come on new battery boxes, so I am documenting their locations.
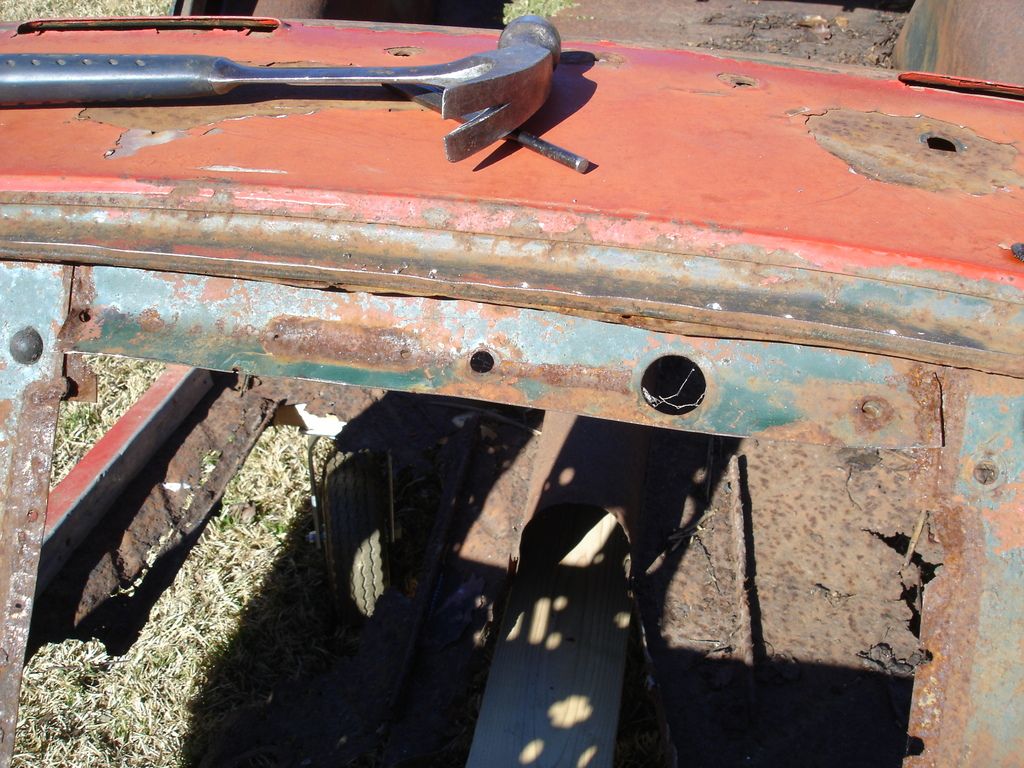
Here I went ahead and cut out the box, leaving just the spot welded top metal to be drilled out.
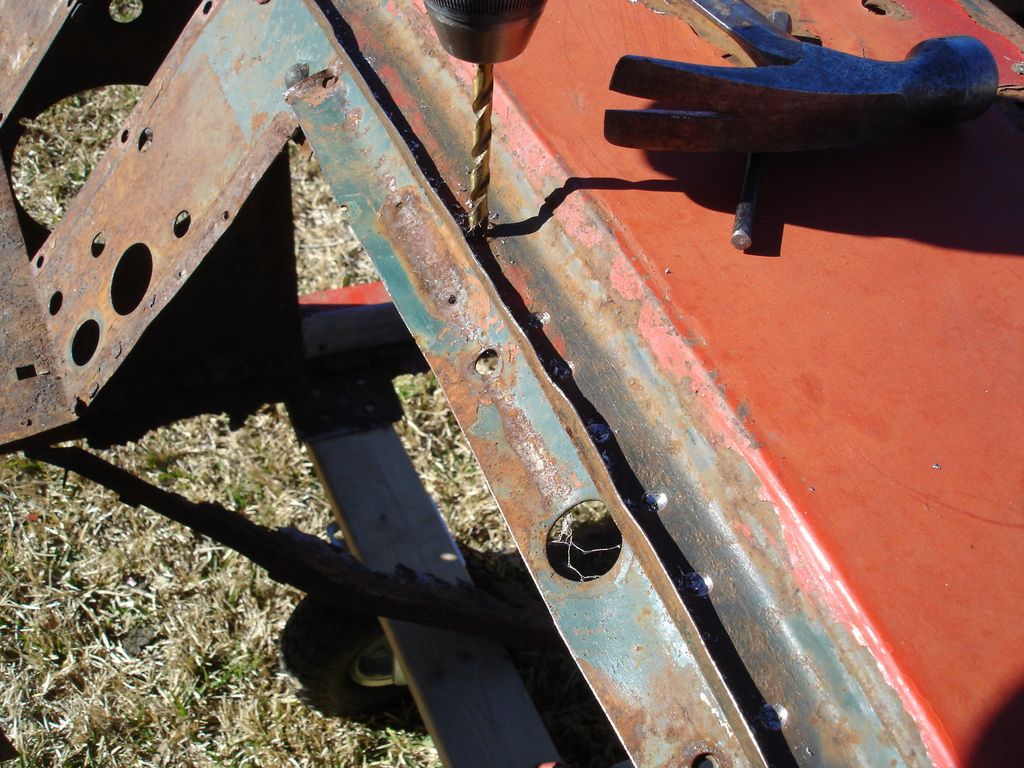
Standard 3/16" drill bit on each spot weld, and then I rapped the plates apart using a 3/16" drift punch. Any problem areas get chiseled. This process wears out drills and chisels fast, so I stop frequently to sharpen them.

The box removed. The tub already looks better, without the mangled box dangling there!
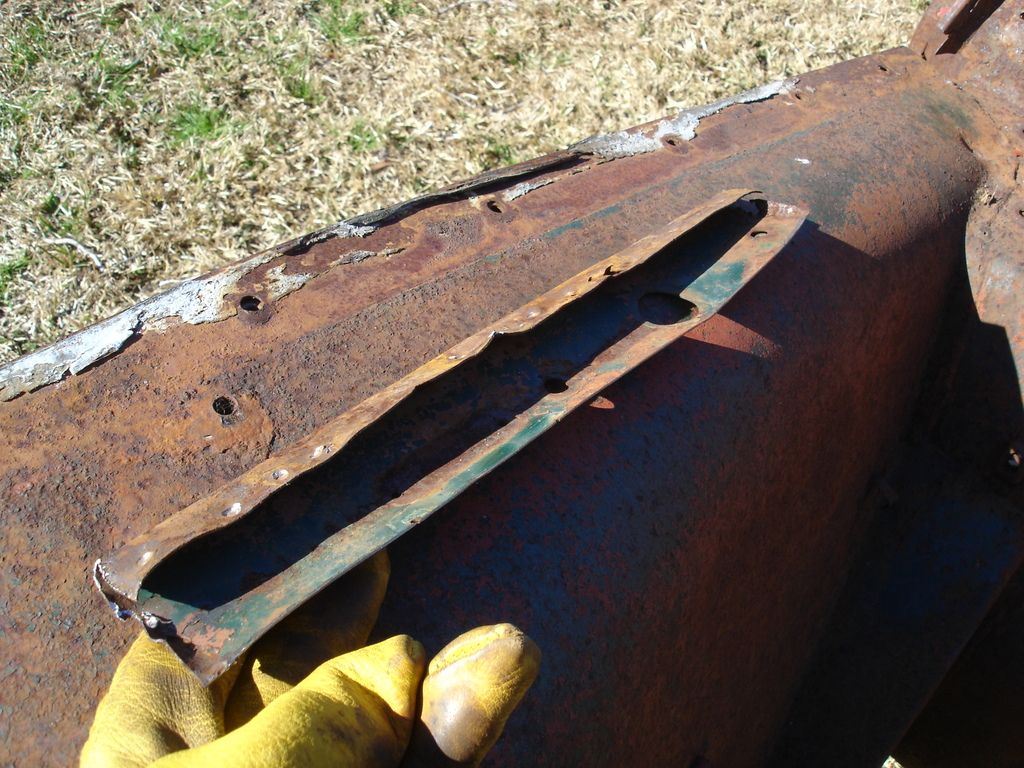
And, Just in case I get confused, I will save the top section with the holes, until I have duplicated them on the new box.
Here is the wire loom "T" on the right side of the box. Also note the angle bracket that attaches the dash brace. These parts do NOT come on new boxes...so they will have to be duplicated later. I will even go as far duplicating the yellow factory markings on the box...when the time comes.
Since this is an overdrive car, the OD solenoid attaches to the left, rear corner. Here I note the spacing and location to duplicate.

This is the left "A" post, to which the door hinges. The post in my TR2 was hit in an accident, and you can see the curve in the post. It should be perfectly vertical and straight. This is the point I will break the front clip from the rest of the tub.
Now, breaking off the front clip sounds envolved, but you will see it is merely a matter of drilling the line of spot welds which are holding the side kick panels to the "A" posts. This is a matter of about a dozen spots per side.
Normally the floor would have to be removed too...but in my particular case..."what floor??"
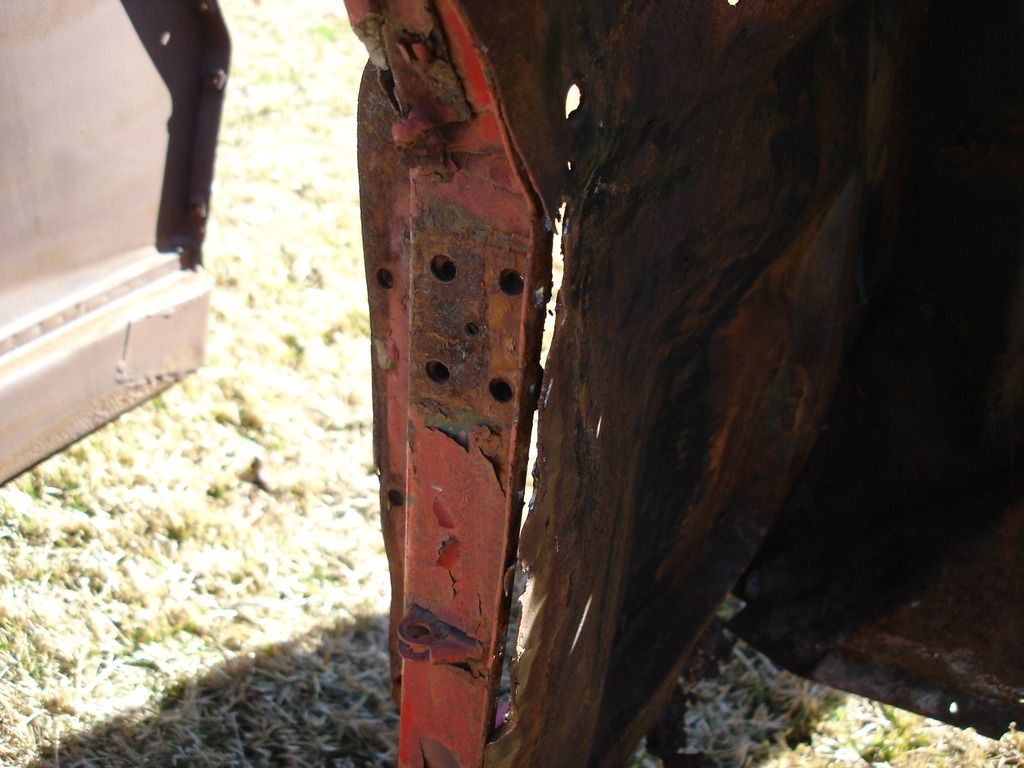
Here I am working my way up the A post drilling out the spots. You can start to see light between the kick panel and A post.
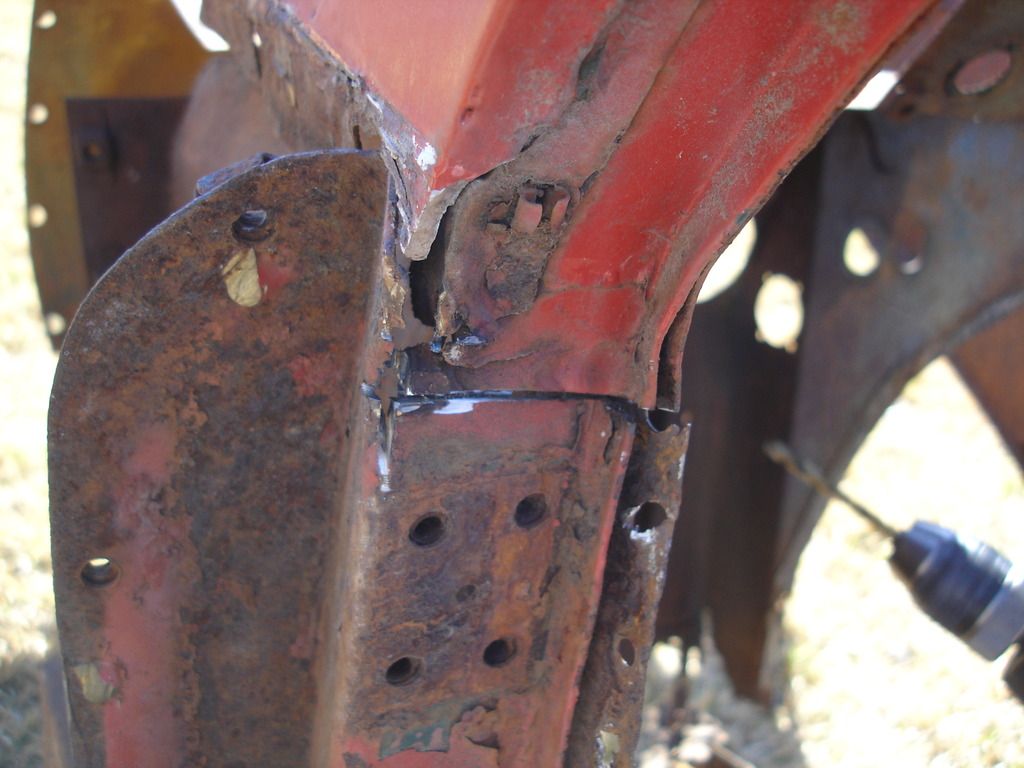
The very top of the post has one long weld, so here I used a cut-off disc to slice through it. I favored the kick panel side of the weld, since I will be re-using the kick panel and NOT the A post.
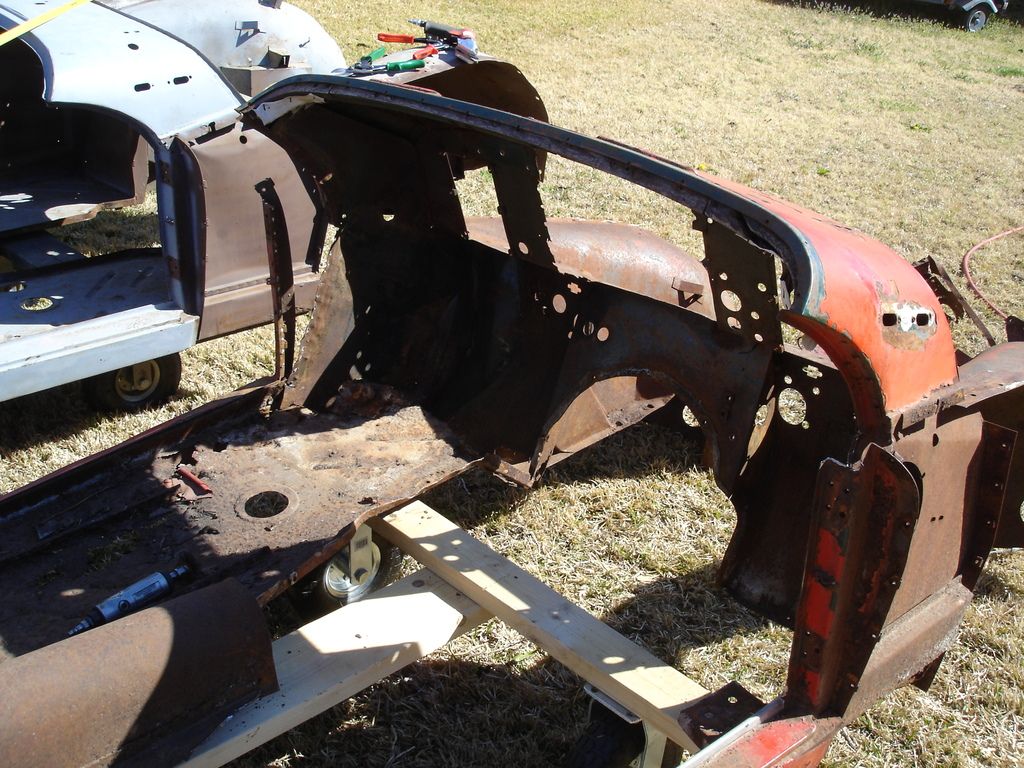
Once the last spot is drilled, the kick panel no longer supports the front clip, so here you can see it is rotating inward. One side down, one to go...
The right side was identical...and here is the front clip removed. I will be able to fit this entire part on my work bench as I patch and straighten it.