Week 18
This week was dedicated to beginning the right wing. Once again, no breaks for the weary. This one is even worse than the left side.
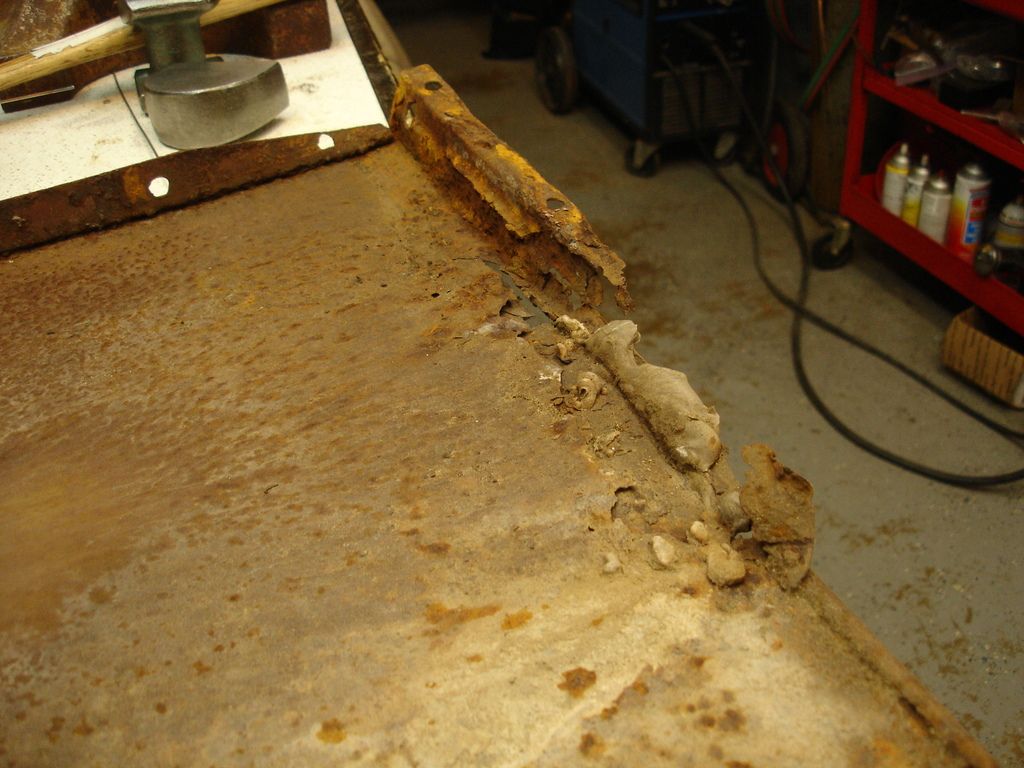
This is the inside of the lower area of the right wing. Lots of bondo shoved through rust holes. The lower mounting flange is half gone, and the rear one is not great either. The mounting hole to the farthest right in pic was drilled by the PO. Not sure what for??
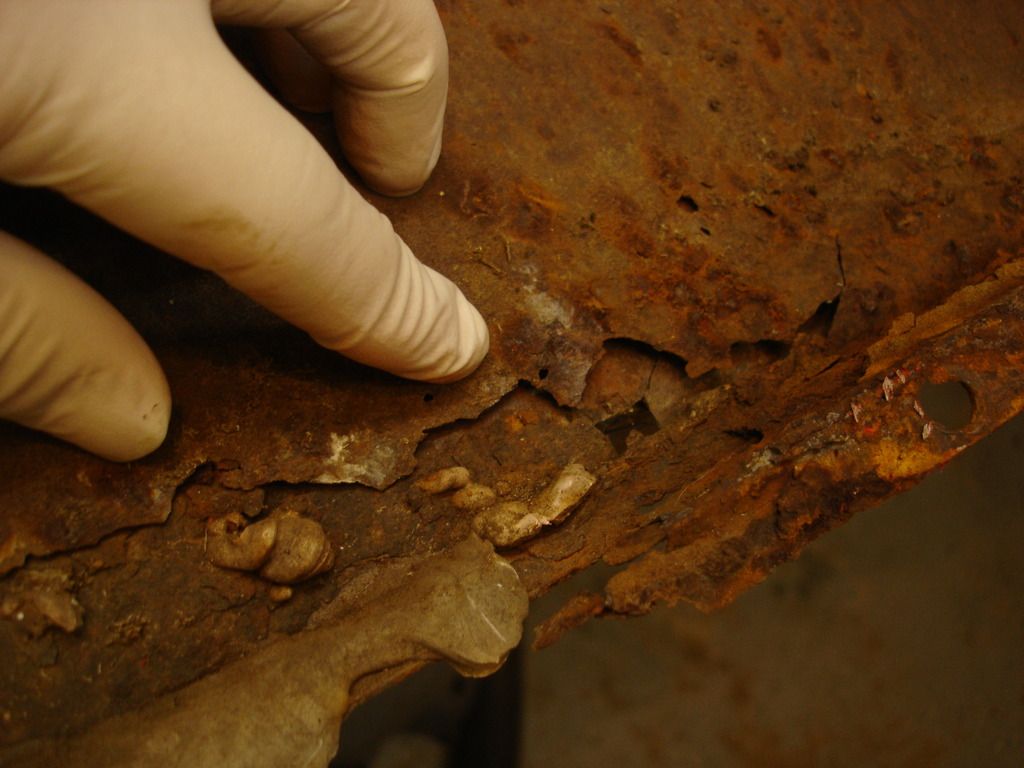
Close up of the "missing" metal. Nothing but bondo holding this puppy together.
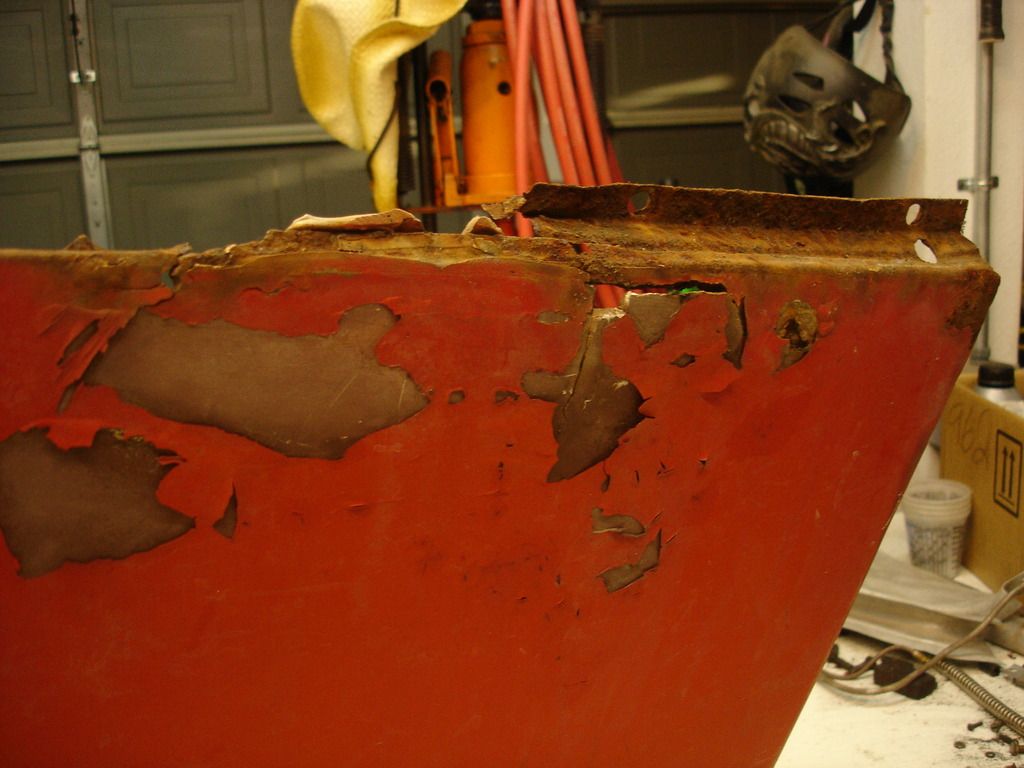
View of the outside of this area. Anytime bondo is cracking, it's a sure sign it's ugly underneath.

This rust is showing through on the very top of the wing, in the area that meets the scuttle and bonnet. This is not normally a rust-prone region, so I have no idea what the story is on this rust.
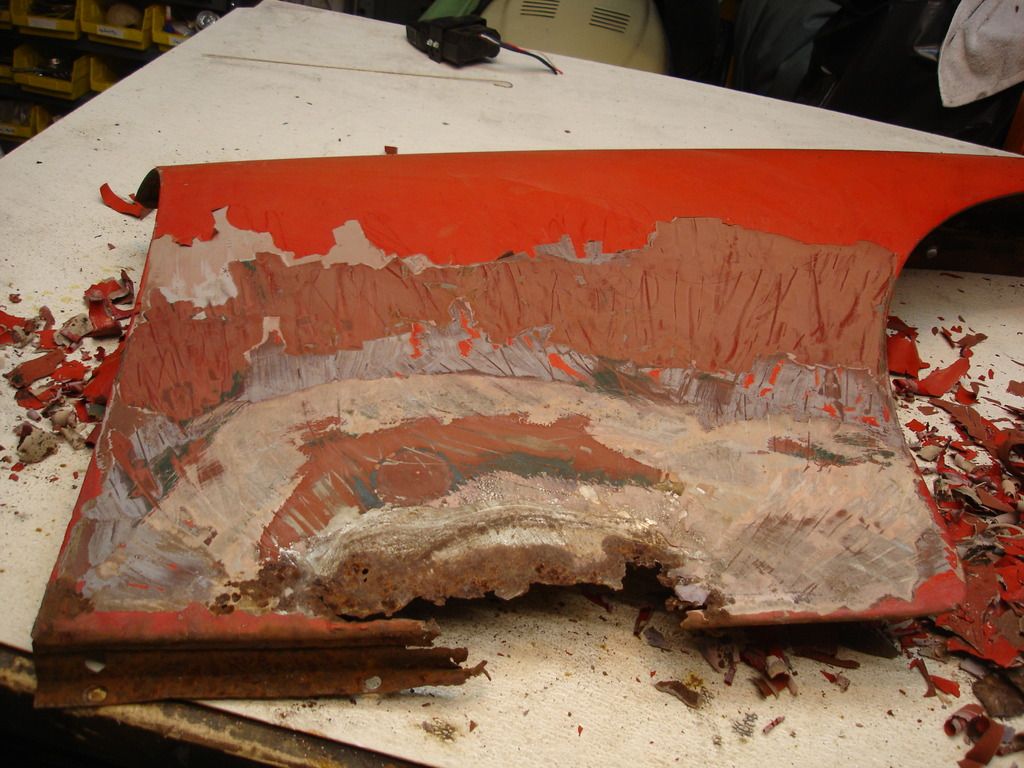
Getting to work. This is the wing after hitting it with mild heat from a torch and scraping all the putty off. 3 layers of paint and 2 of bondo.
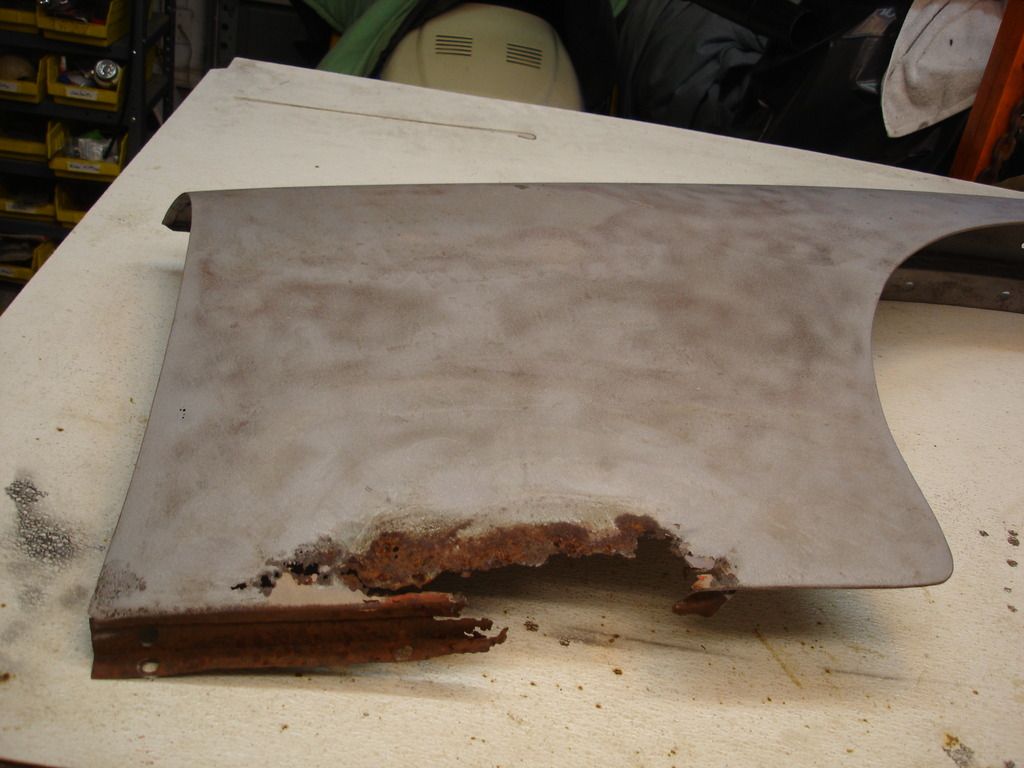
And...after a quick trip to the backyard for sand blasting, we're down to the basics. Of course, the lower section is going to have to come off...

These pin-holes opened up with the blasting. They are up along the rear edge of the panel where it meets the front of the door. I will have to plan the patch metal to be large enough to remove this area too...
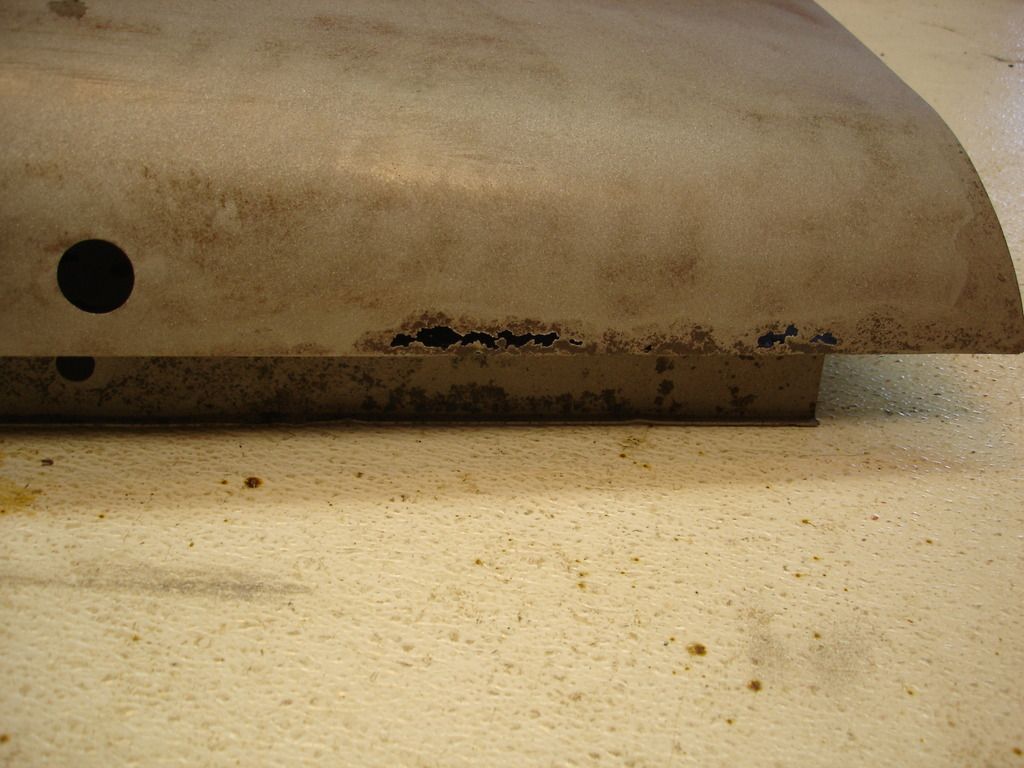
...and...the top of the wing where it meets the scuttle. Bummer! But, I actually like working on this area more than the large flat areas. The curvature prevents major warpage that has to be hammered out.
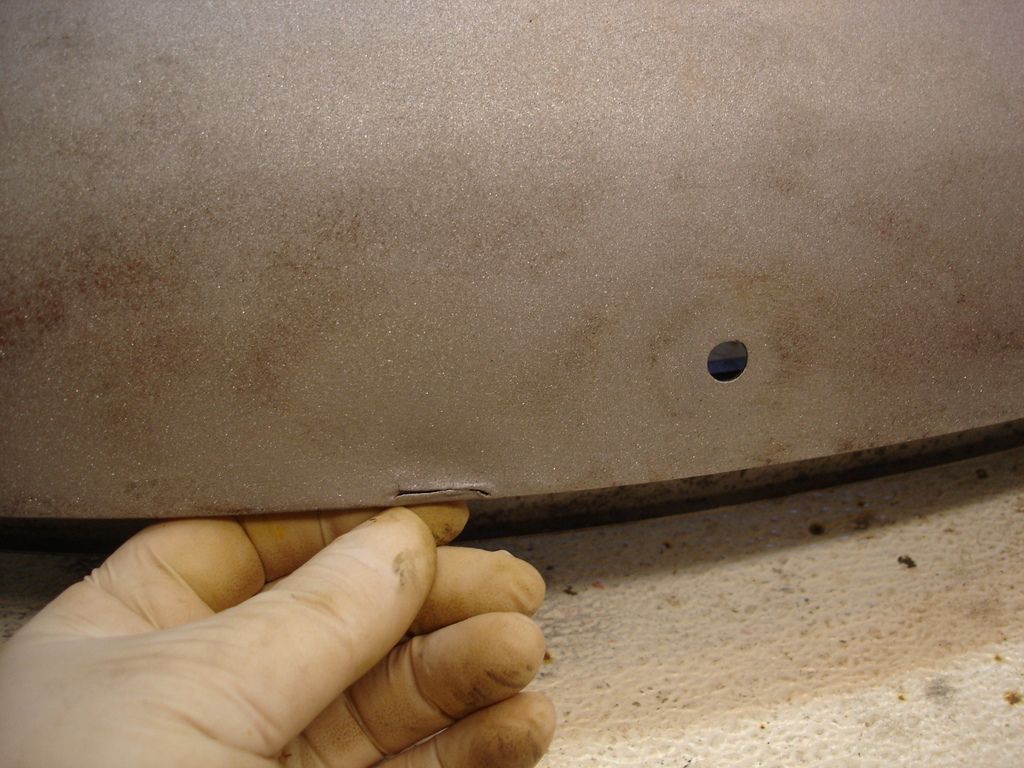
Farther forward, another one of those blasted 1/2" holes the PO put in just to annoy me! Also a small slice along the edge of the wing.
Along the upper mounting flange, there are a handful of pin-holes to be filled or patched.
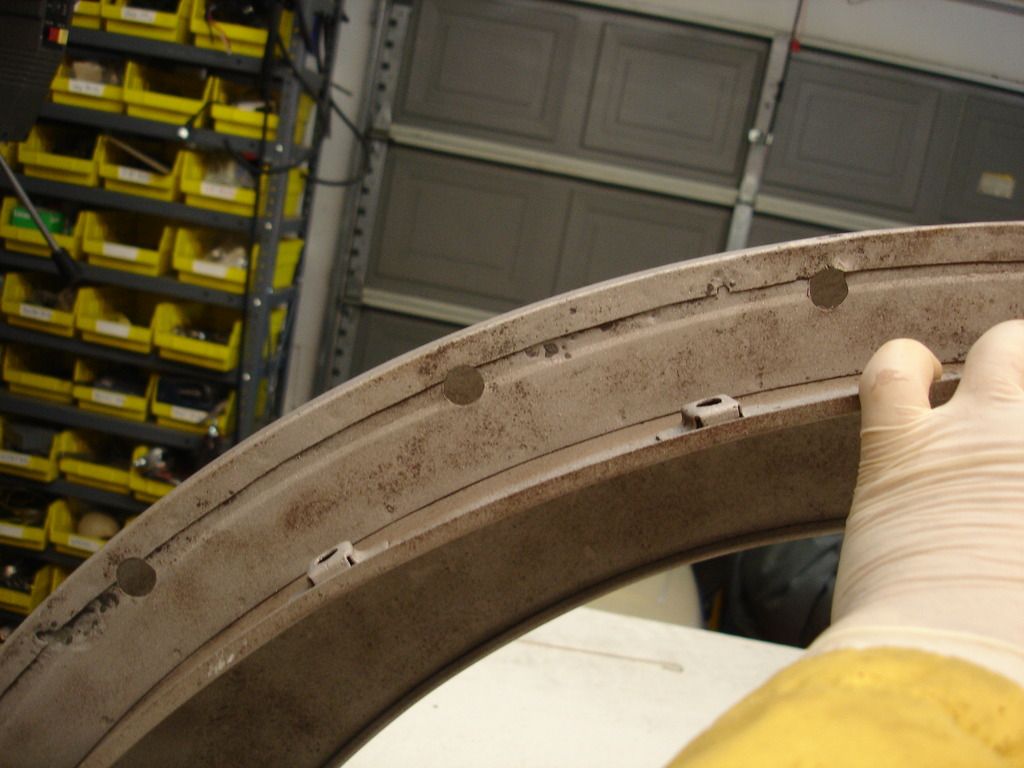
Of interest in this pic...this wing is an original TR2 wing. It is different than the TR3 wings in a couple ways. One is that the front apron mounting holes on the TR2 do not have slots, but only round holes to mount the apron. Secondly, if you notice in this pic, there is a groove that runs along the upper mounting flange on this TR2 wing. The TR3 does not have that notched groove. The slotted holes are mostly hidden in the wheel well, but the flange groove is noticeable any time the bonnet is open...to those few souls that would know to look. I wish I had noticed this when I had the flange removed from the left wing, as I could have easily added the TR2 groove. Oh well. I have to limit my annul tendency or I'll never finish this project!
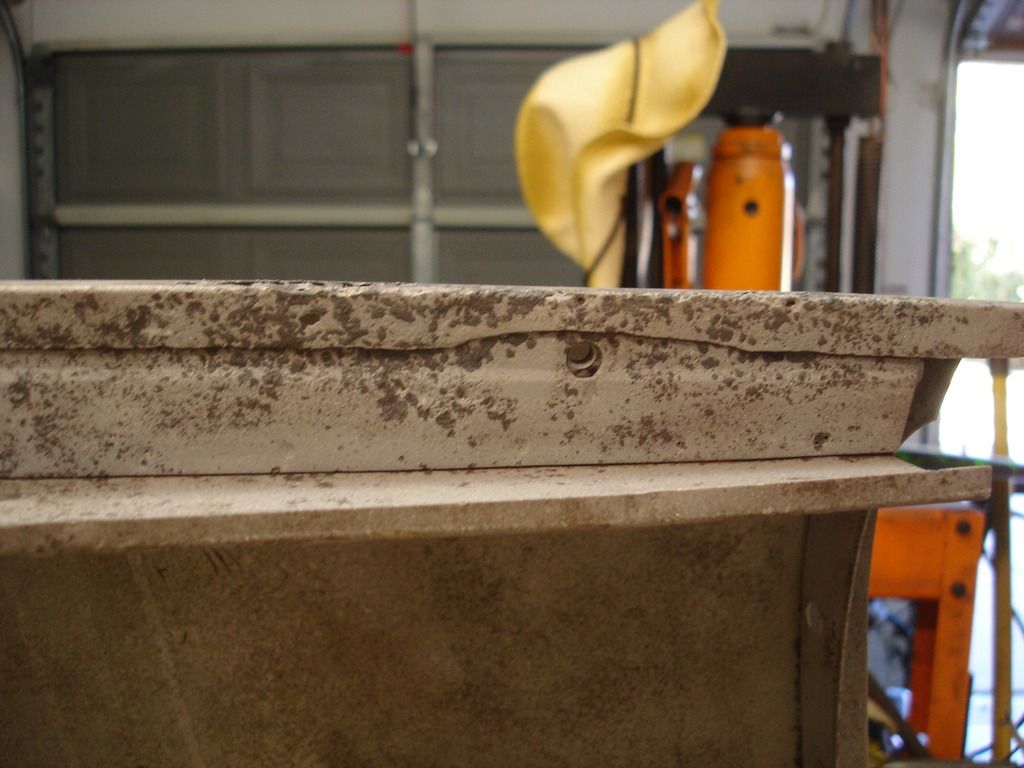
The rear upper flange area. Not easy to see, but there are some pin-holes here to be filled.
I think that about wraps up the problems to be fixed. So time to get to work!