CJD
Yoda

Offline
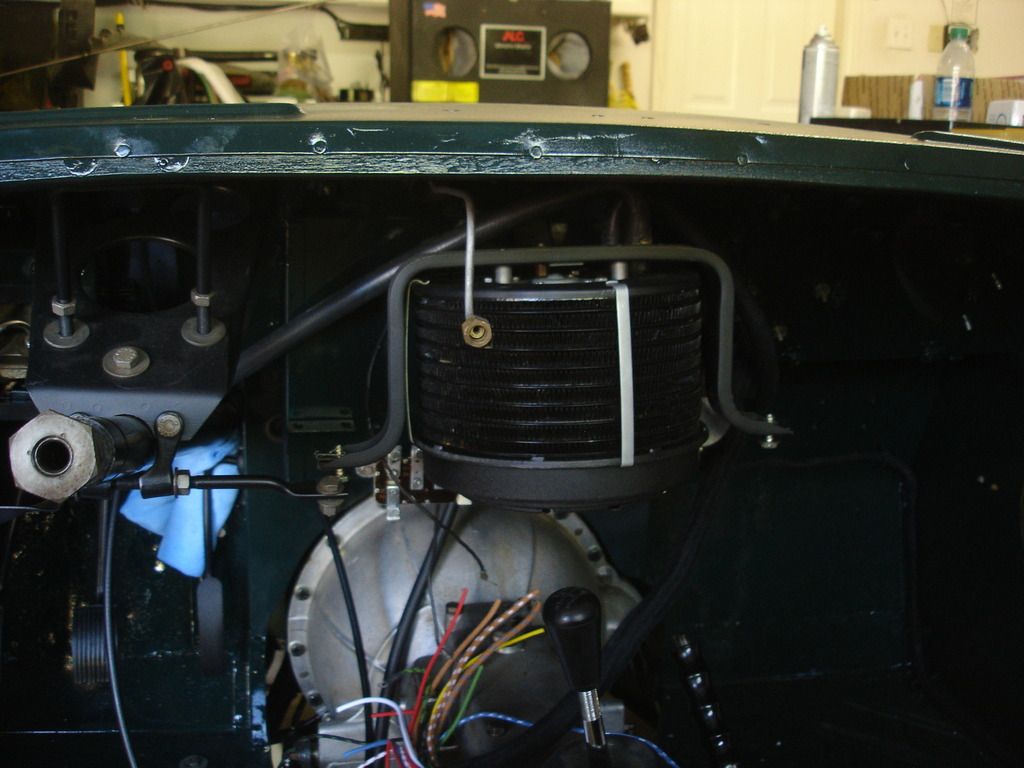
The heater is hung, although not fully secured yet.
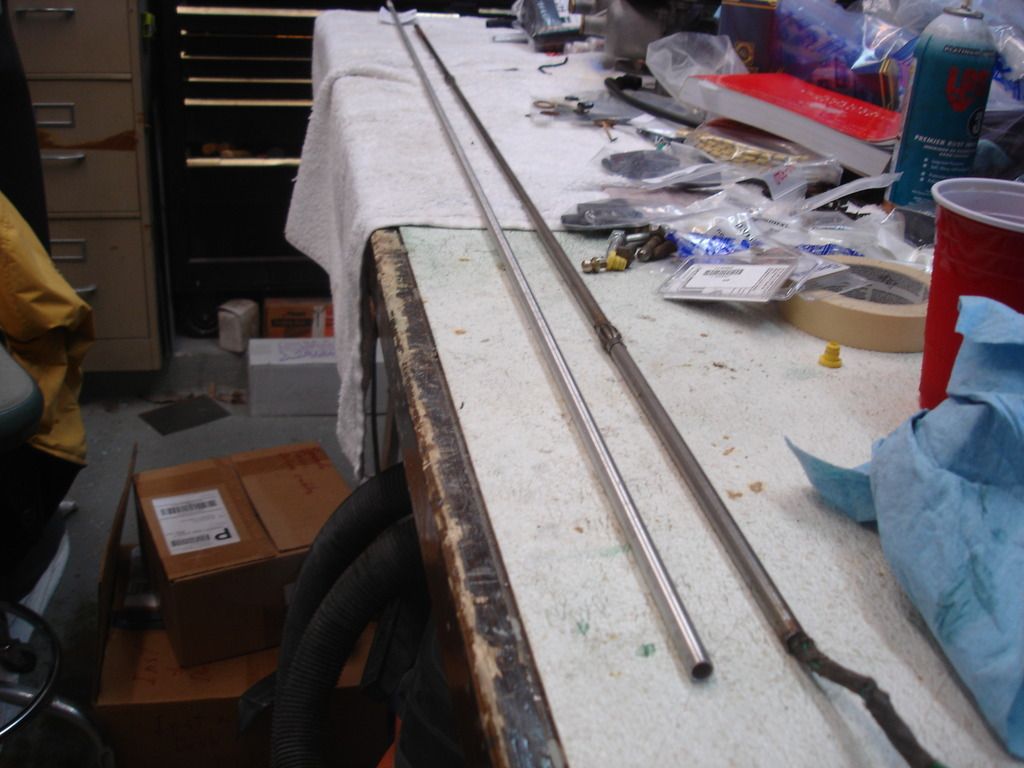
The last couple days were frought with problems. This is the original stator tube on the right. David sent me to Grainger, who carries the similar stainless 3/8", .035" walled, 61.5" long tubing. The original is not stainless, but oh well. I intended to purchase this...but they are currently NLA.
So, let's get to work building a new stator tube.
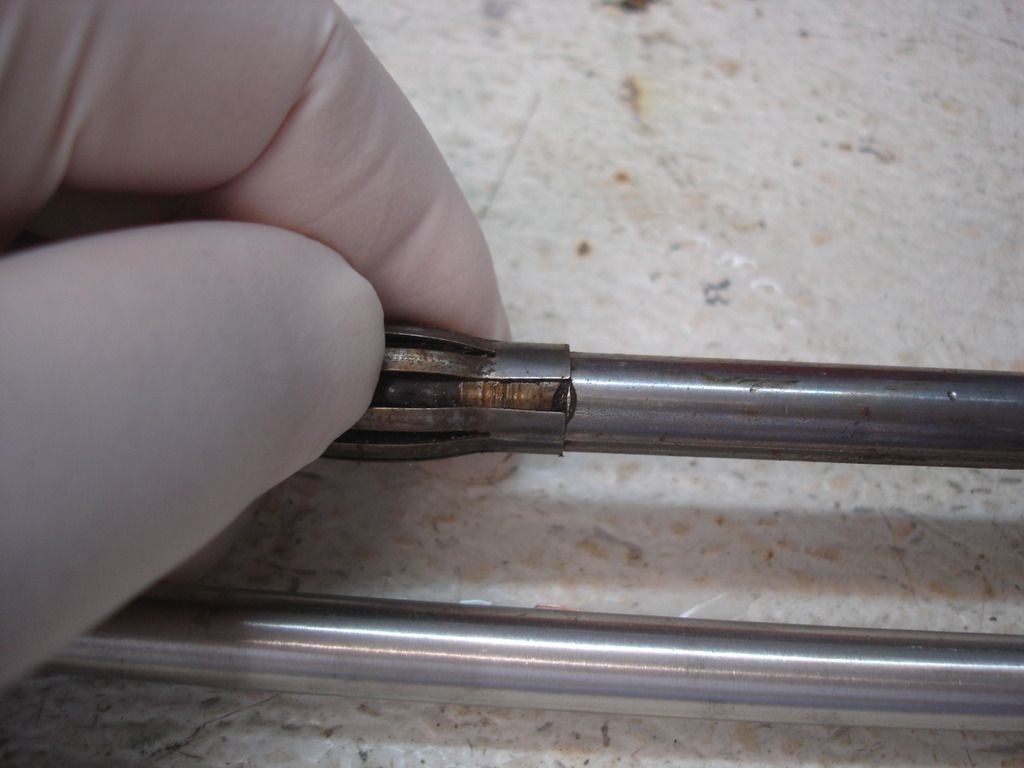
This is one of the 2 support bearing around the tube. Look closely and you see that the bearing is split, and the tube has a notch formed to retain the tube in place. By aligning the notch with the split, the bearing can be slid off.
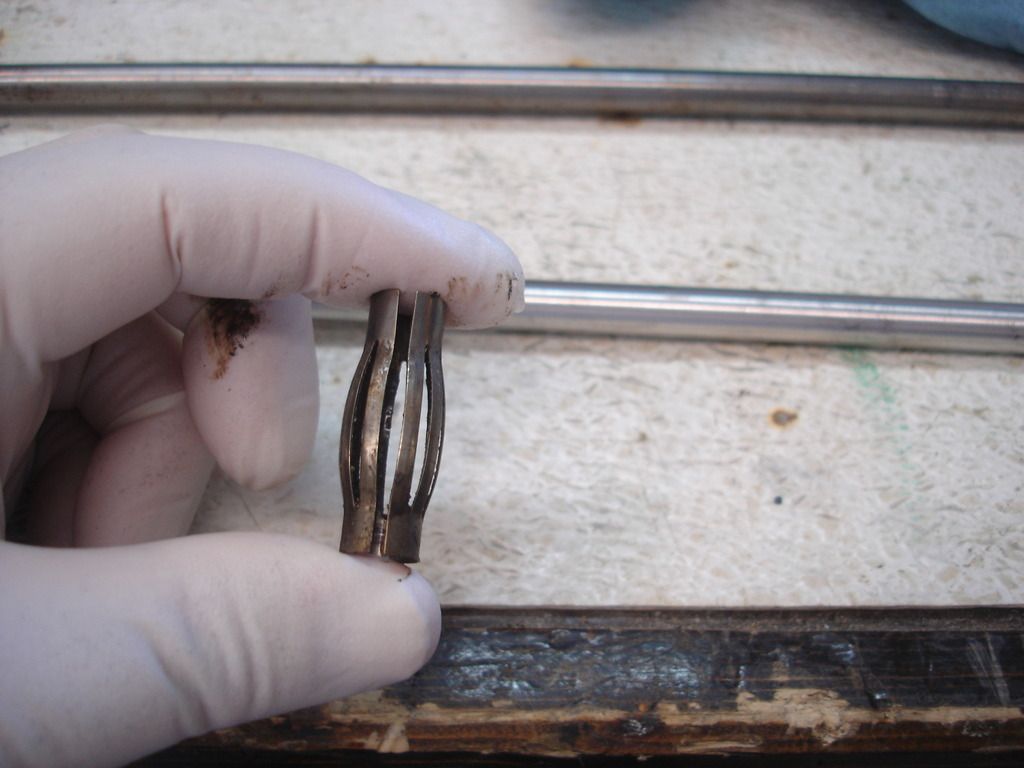
Here is the removed bearing. I learned later that the inside of the column actually has thinner ID sections to support the 2 stator bearings. The bearings lock inside the narrow areas, and then allow the stator tube to turn free of the steering shaft. I guess technically, the stator is stationary and the steering shaft revolves around it...anyway, the point is that the bearing follows the shaft, and holds the stator in place.
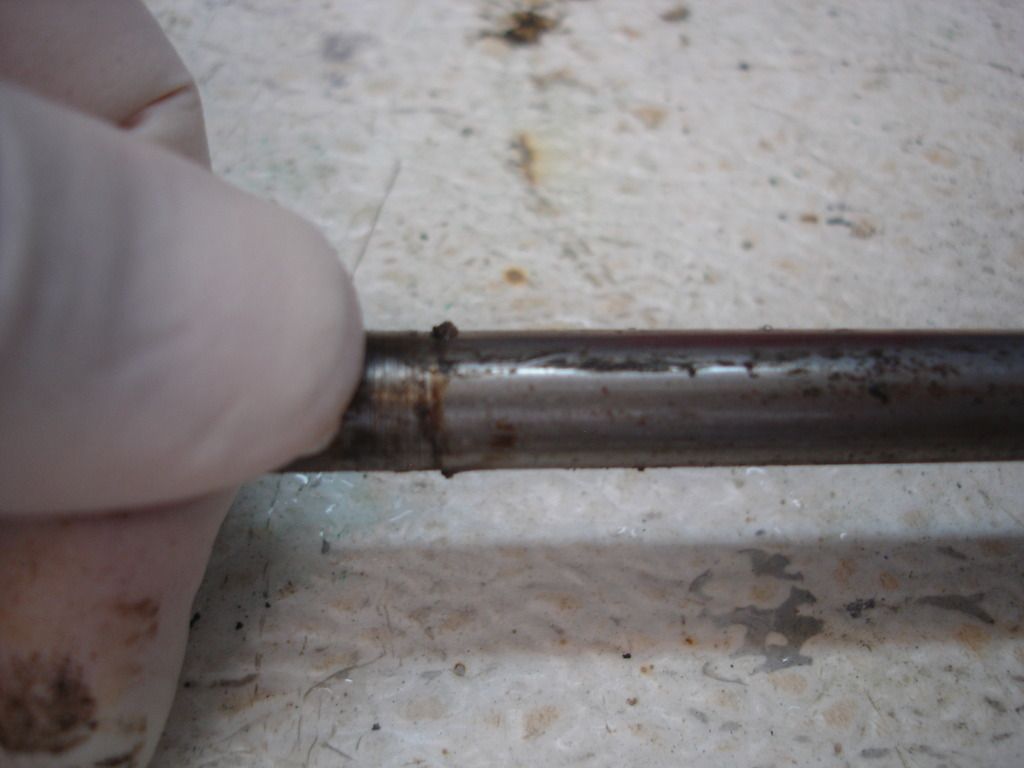
This is a blurry close=up of the notches that retain the bearings in place. They appear to have been made with a heating process, as they are heat colored.
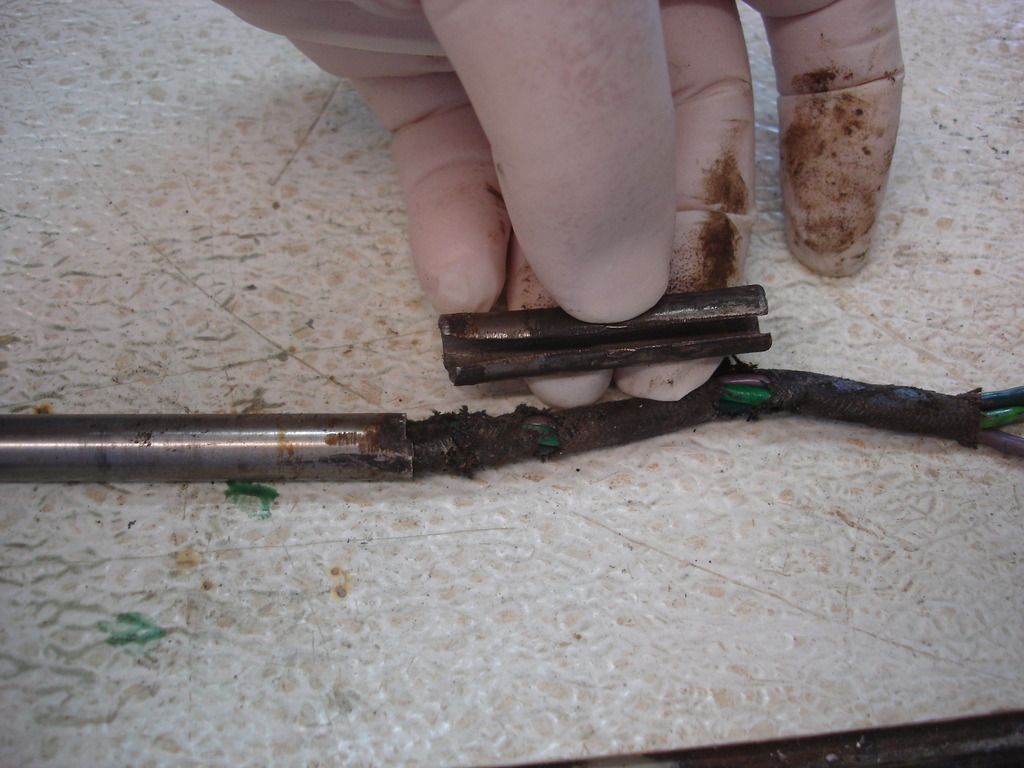
This is the main reason I need a new tube. The slotted end that retains the trafficator was broken off. If the trafficator lubrication gets old and hard...this is the typical failure mode of the assembly. The weakest link is this slot. The secondary reason I need a new tube is that the wires twisted so tightly in the old tube that they are not removable...at least by me.
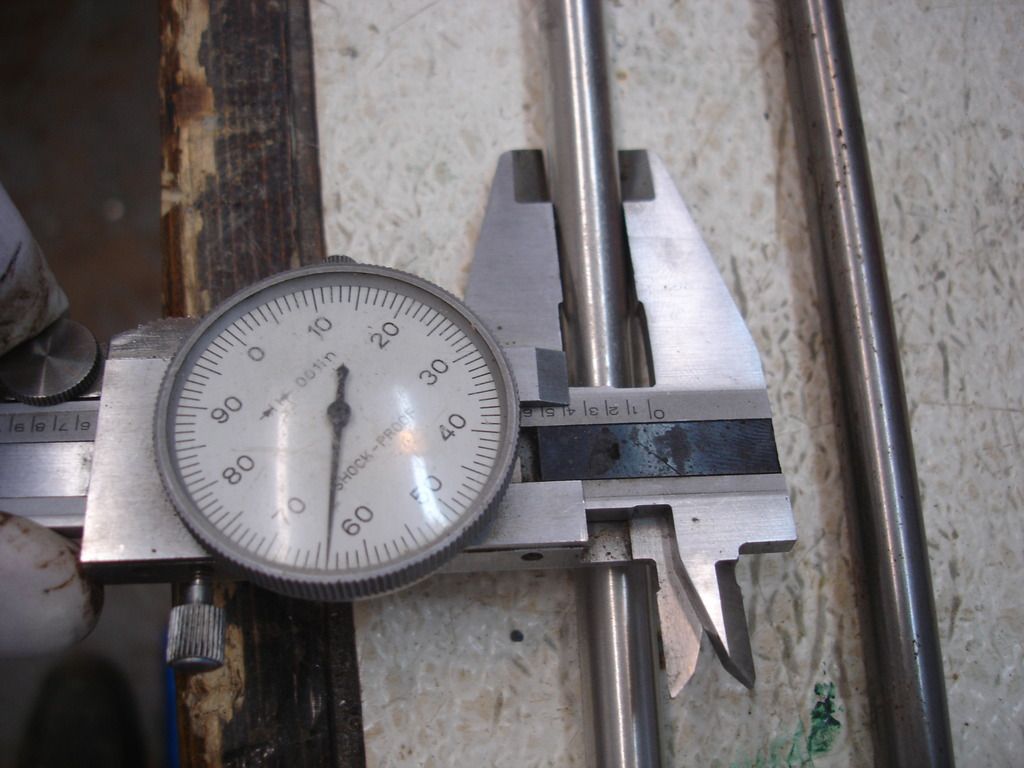
3/8" tubing should be .375". The new tube mics at .364"...exactly what the old tube mics at. So at least something is going my way!?!

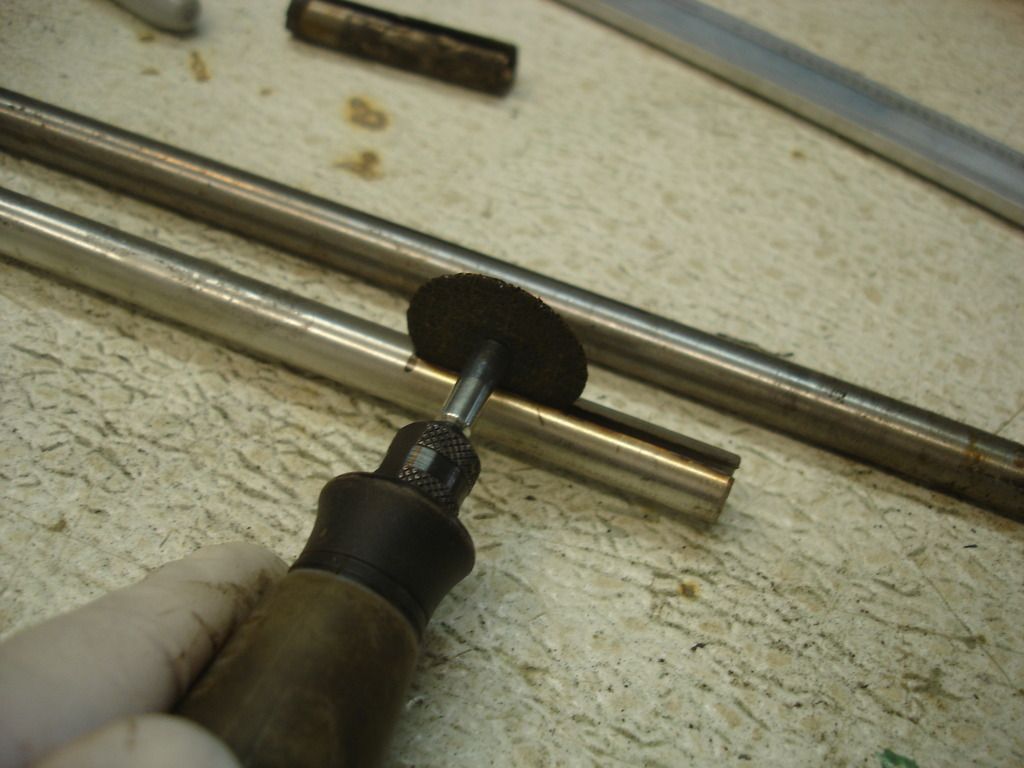

The initial cut was with a Drexel cutoff wheel. I then opened the cut with the larger cutoff disc.
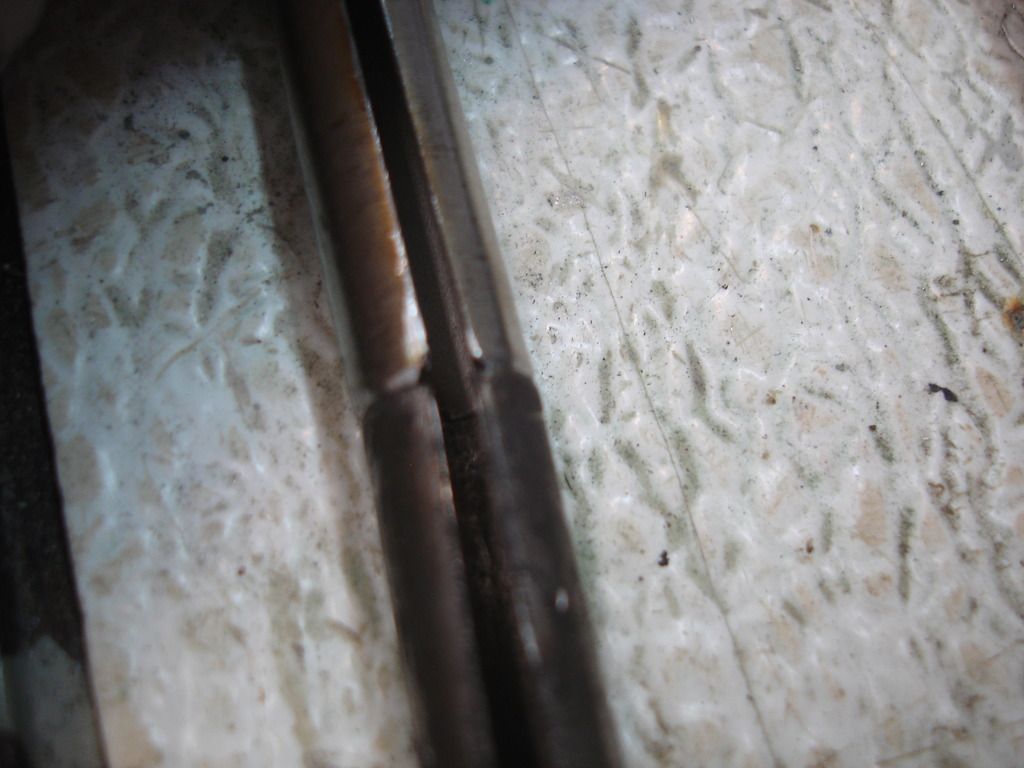
The end result of the new slot held up to the original. Close enough for government work.
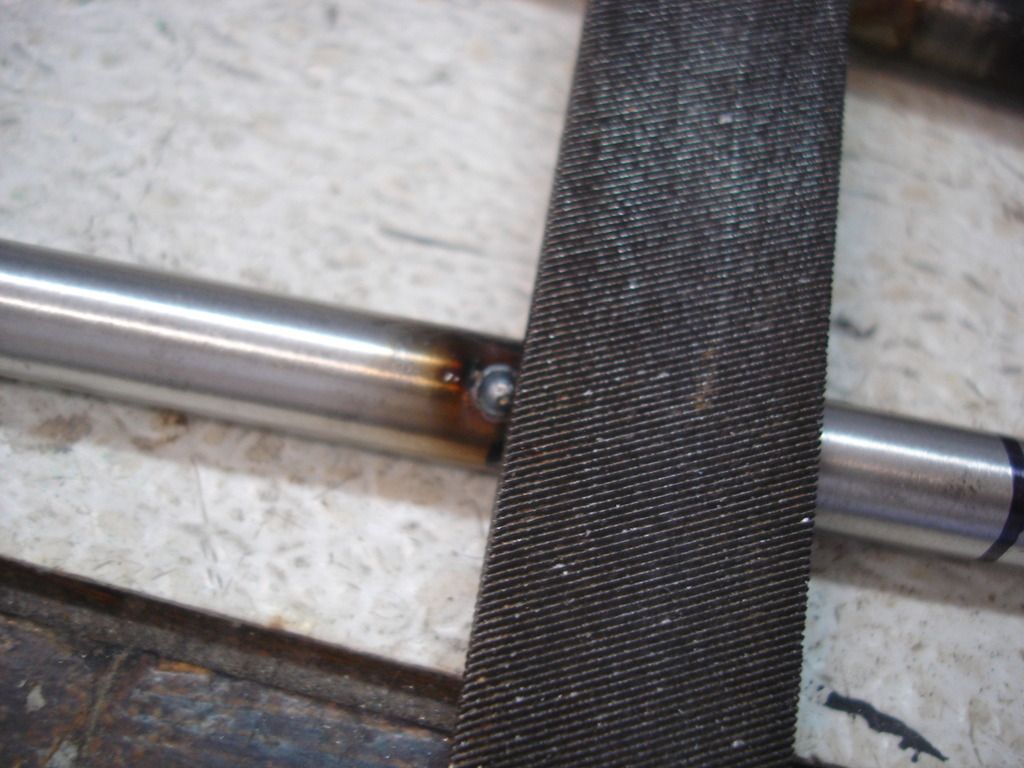
Now for the bearings. I practiced with the extra length of tubing. I wanted to leave a single tack of metal on the tube, but without heating the tube enough that the tack would go to the inside of the tube. Getting the wires through a smooth tube is hard enough. If the tack left a "bump" inside, it would ruin the job. In the pic I am filing a flat for the bearing to ride against.
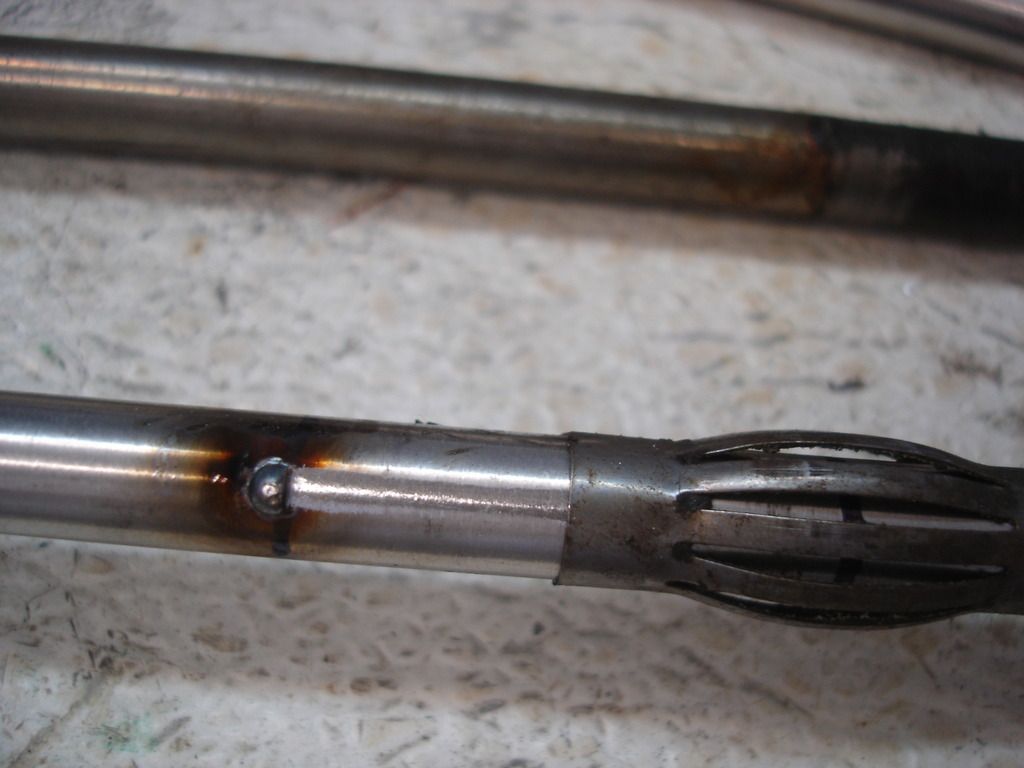
This is the first bearing retaining spot. Once the bearing is slid into place, then I will place the second at the other end.

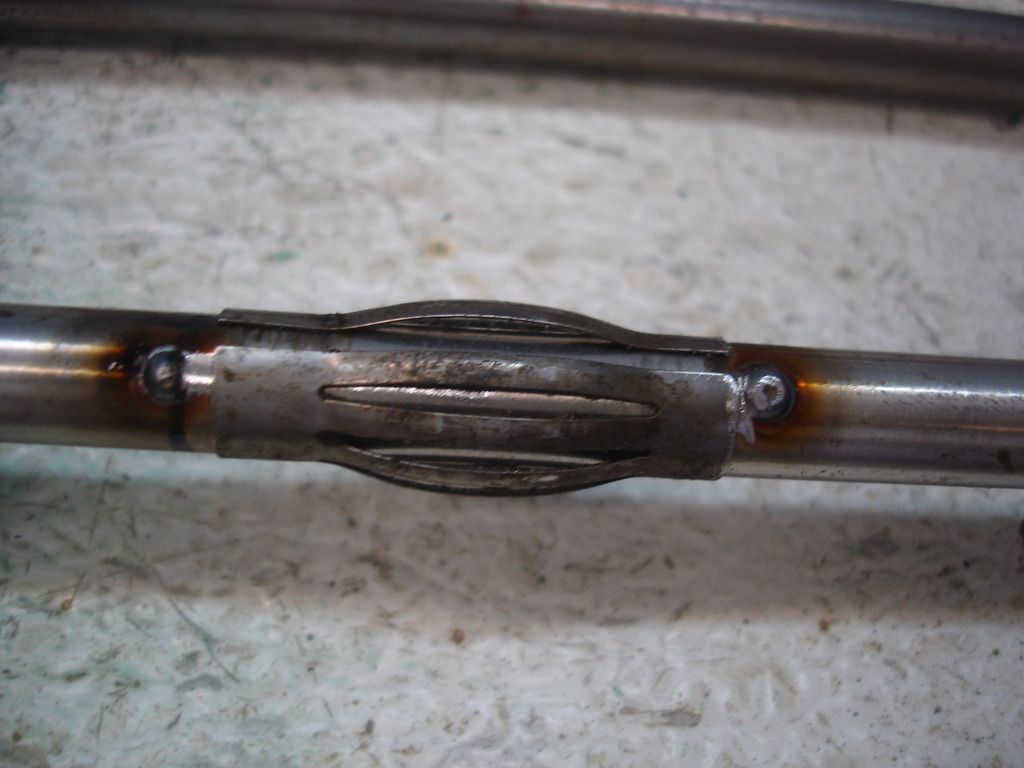
And it's done. Not quite as pretty as the original, but just as functional.
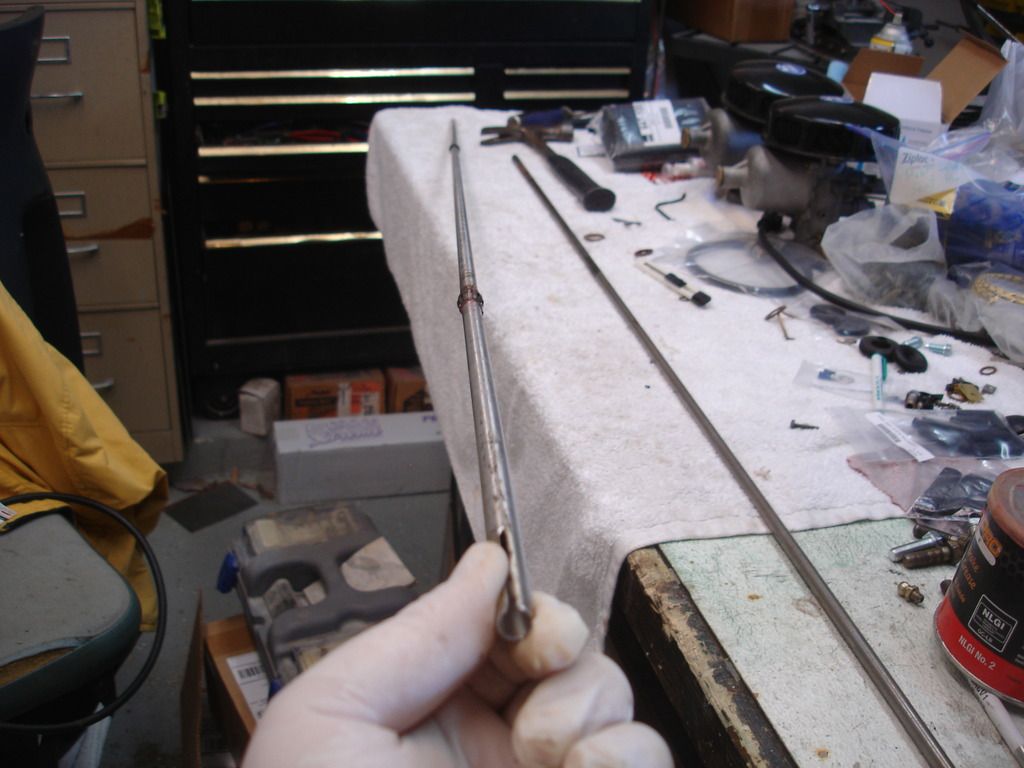
The end is cut to the proper length, and the new tube is ready to install.
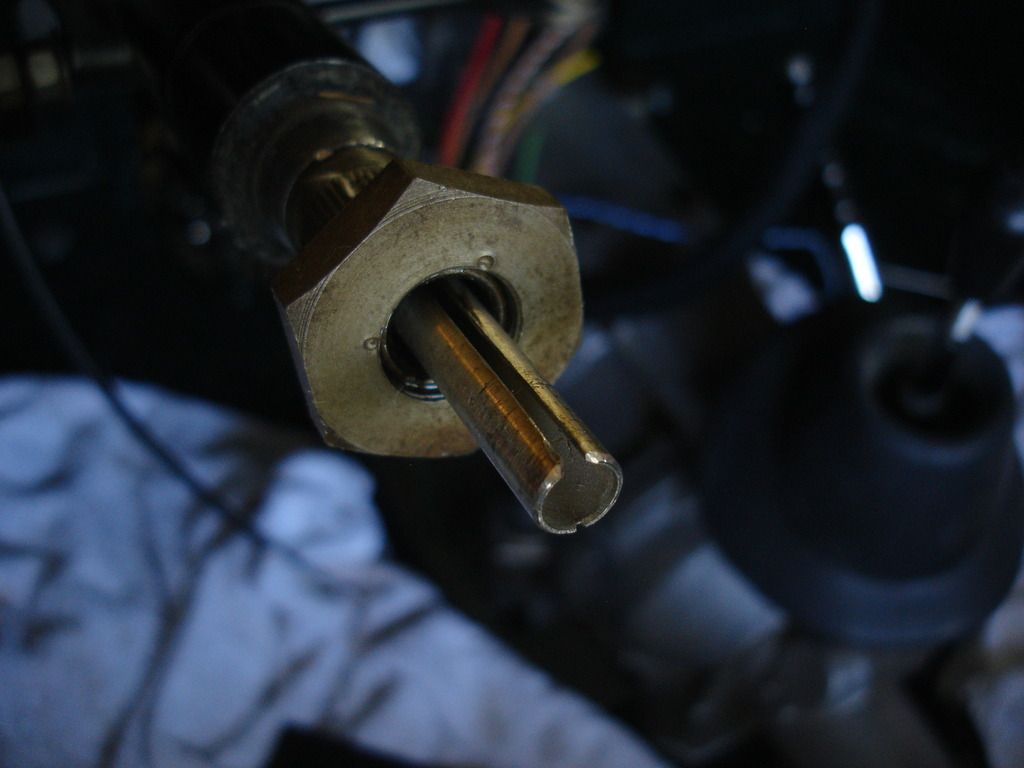

Blurry and dark...this is the steering gear end. I will have to get a new collar and nut once the trafficator is installed.
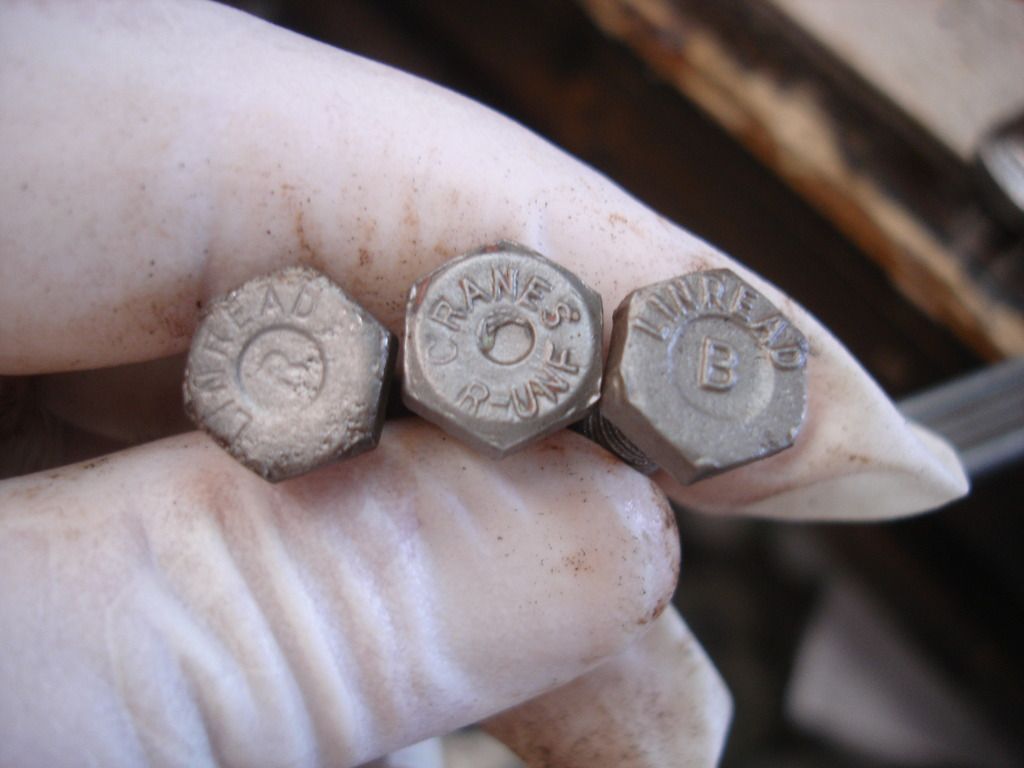
These are the 3 basic brands of bolts I have off TR3's and TR2's. The "B" was the most common on my TR2. I do not have enough of any single bolt brand to complete the entire build...So...my goal was to have the same brand in any area you are looking at. In other words, if you are looking under the bonnet, you will only see the "B" style bolts. Peal back the carpeting and you will see only "R" style bolt heads. OK...I know it's annul. Not to mention it took most of the day to bead blast every bolt, washer, and nut...AND run them through a clean-up die to repair any damaged threads.
I'm out of mechanical parts for a while...going to the bodywork thread for a bit...