David, Art. I am going to need about 100 cage nuts since I have fabricated new inner rear fenders, firewall, rear floor panel, rear side panels and will be replacing the outer edge of both inner front fenders. Where they are available, I will re-use the nuts but many have the bolts broken off in them.
Art, I like the cage nuts from Mcmasters and Macys. They are a quality product. A shame things have happened that now make it unviable for Macys to supply internationally.
As an exercise I thought I would have a go at making the cages. I have a cheap HF type bench shears and thought I might be able to adapt it to punch the sheet metal. To cut the whole cage would take to much force so I opted to punch the edges out of a strip. I used an old file to make the cutting die and the female form it punches through. The die was set into a blade I copied from the original blade in the shears. The die and the form were fabricated with an angle grinder and bench grinder. I clamped the cutter between several heavy pieces of metal as heat sinks while I tigged it into the shear so the strength of the cutting edge would not be harmed. The shear is simply a length of 3/8" flat bar. The female form is welded to a length of angle bar which bolts to the frame of the shears. There is a fixed fence to set the depth of cut in from the edge of the strip of sheetmetal. The blade has a detent at the back which sets the position of the cut so I can feed the sheetmetel in and the next cut is set up ready.
Sorry but still can't make sense of which way a photo taken on my iPad will upload.
The head of a punch for shaping the cages over the pedestal. A perfect example of the angle grinder as a precision milling machine. (It does the job! Happy to accept donations of a milling machine for my next project)
Resulting strip after punching and drilling the bolt hole. Initially I anticipated making a punch to press the holes but found marking, centre punching and drilling the holes didn't take much time. Since the bench shears are currently re-employed, I separated the cage blanks with hand shears.
Half inch square pedestal to shape the cage over.
First bend with punch
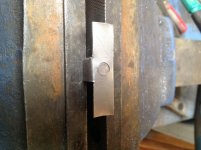
Second bend with the punch.
First two attempts. First one a bit rough as I sorted out the depth necessary to puch the sheet down.
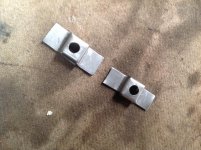
No problem with the nut falling out. 10 done, 90 to go!
Next job is to set up how I am going to make a mass of nuts to go with the cages. My lathe has been put on notice!
Lionel