CJD
Yoda

Offline
Now I was down to "buttoning up" the tach. After everything else I did, this is both easy and fun. Here is the quick and dirty:
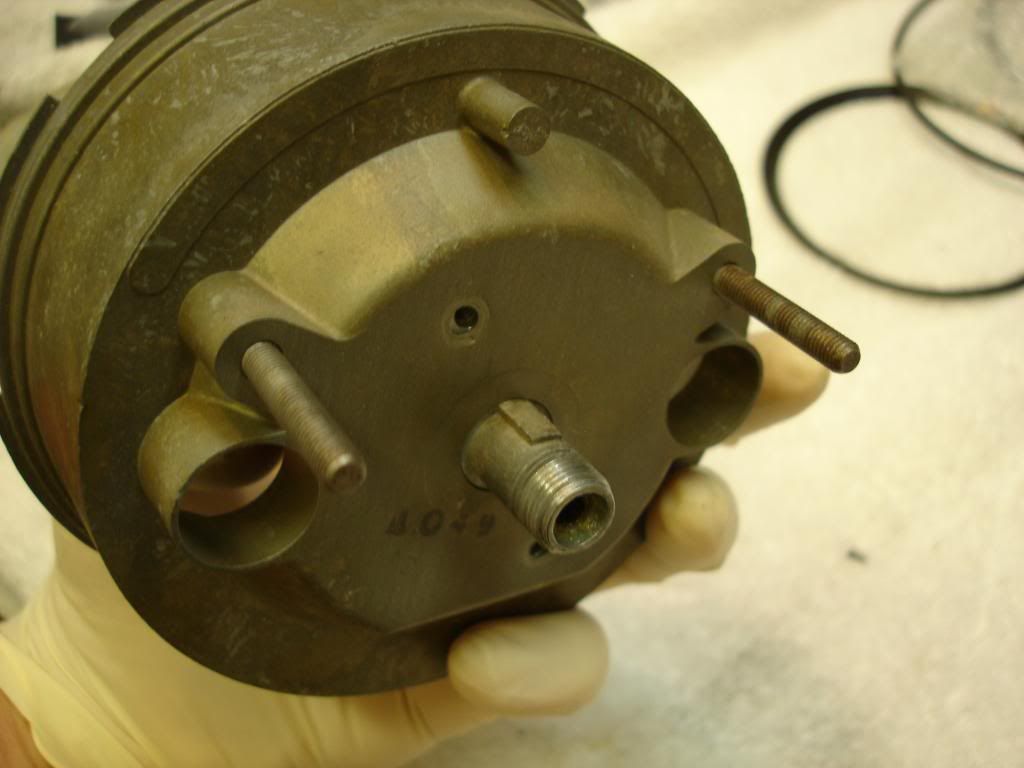
First, the assembly we have been calibrating goes back in the case. You will likely be confused, like me, as it can go in both the right way...and upside down. The key on the drive dog goes upward, as shown. The case mounting studs also go to the top.
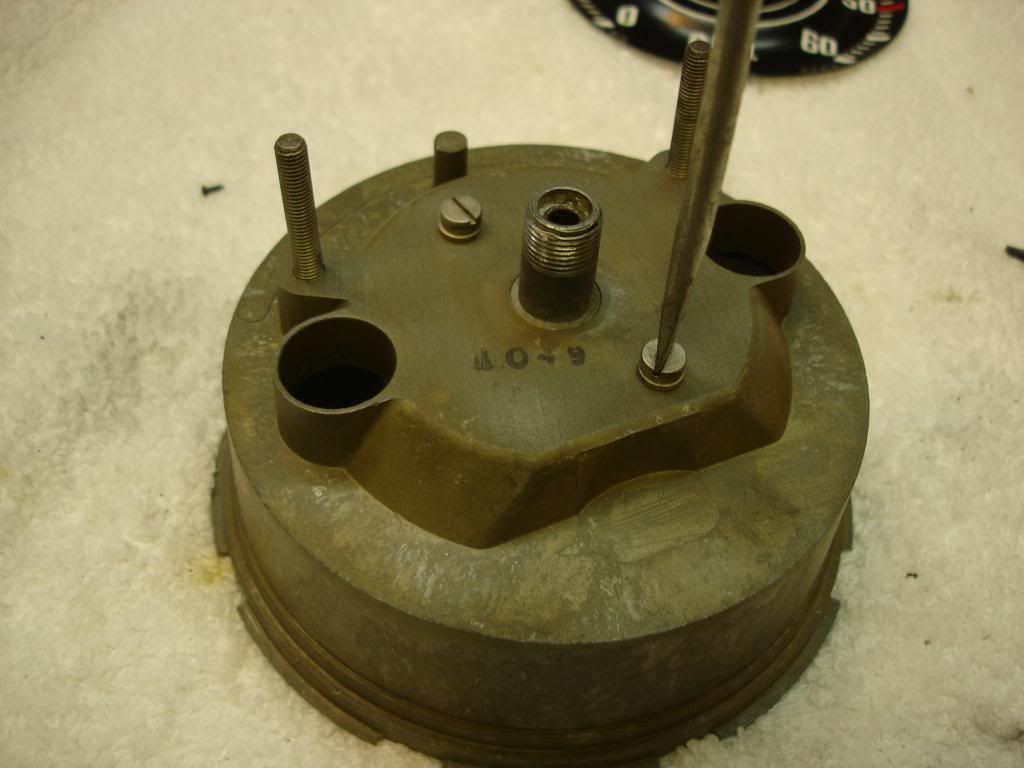
Secure the two screws with washers to hold the frame in the case.
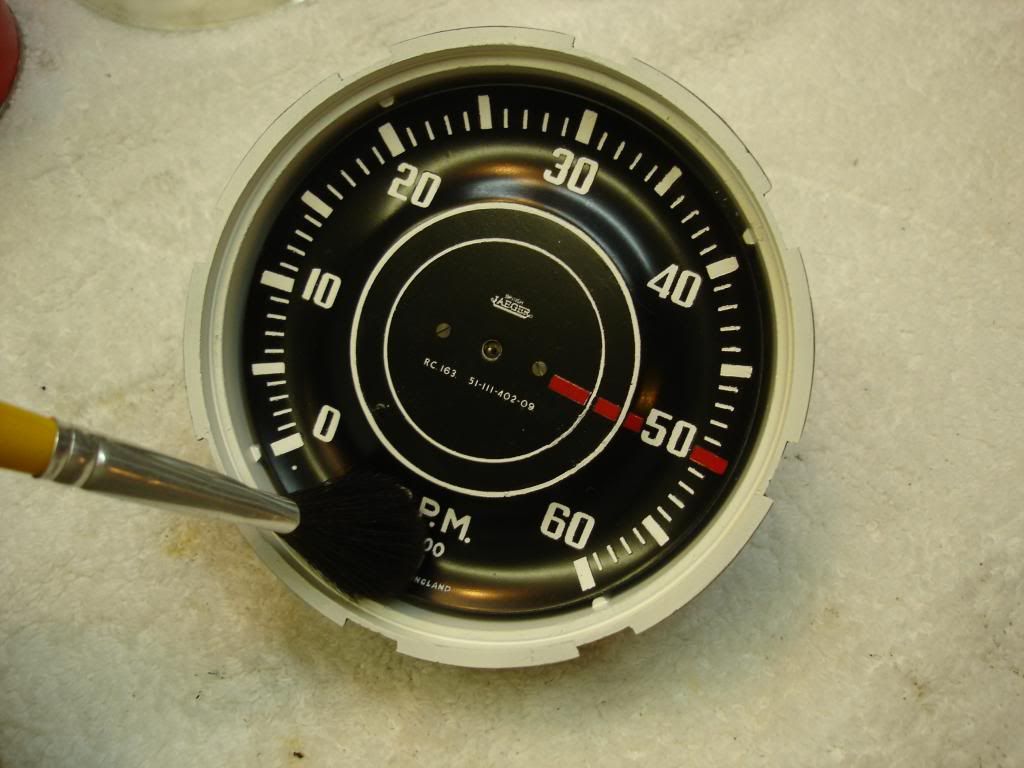
This is the last chance you will have to make sure the unit is dust free. I blew with air and then dusted the face with a very soft brush. Ignore the fact I have no needle on at this point...yours should be on.
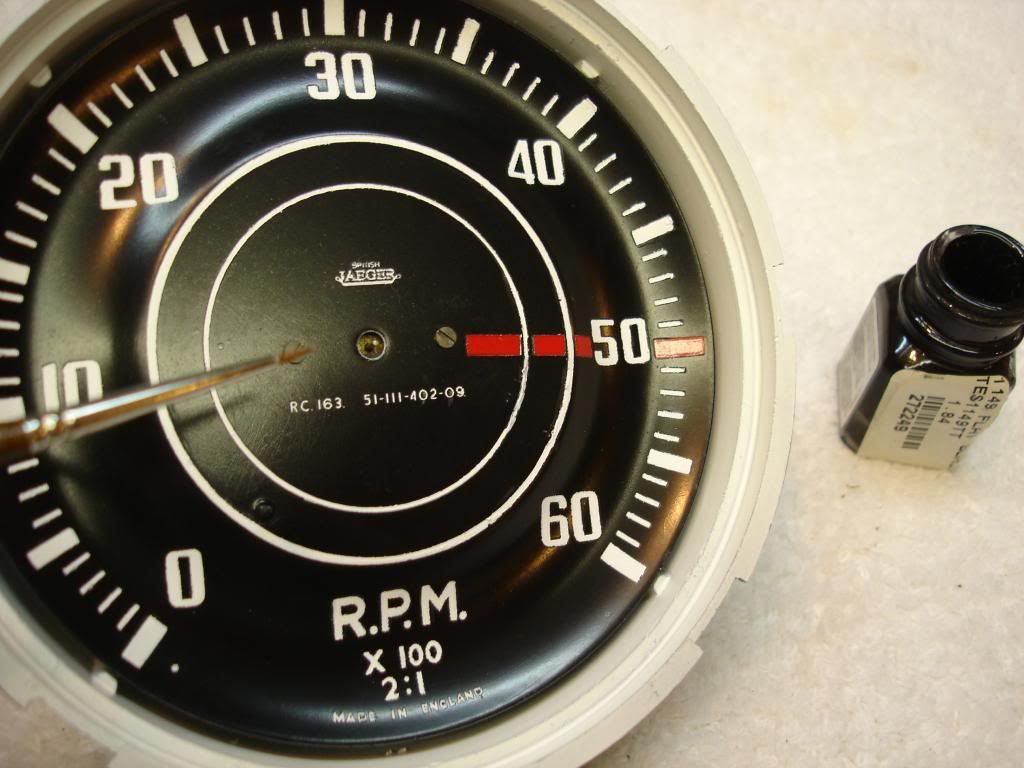
I did a final touch up on anything that needed paint. The face mounting screws were a bit tarnished, so they got a dab of black paint, along with the needle stop post.

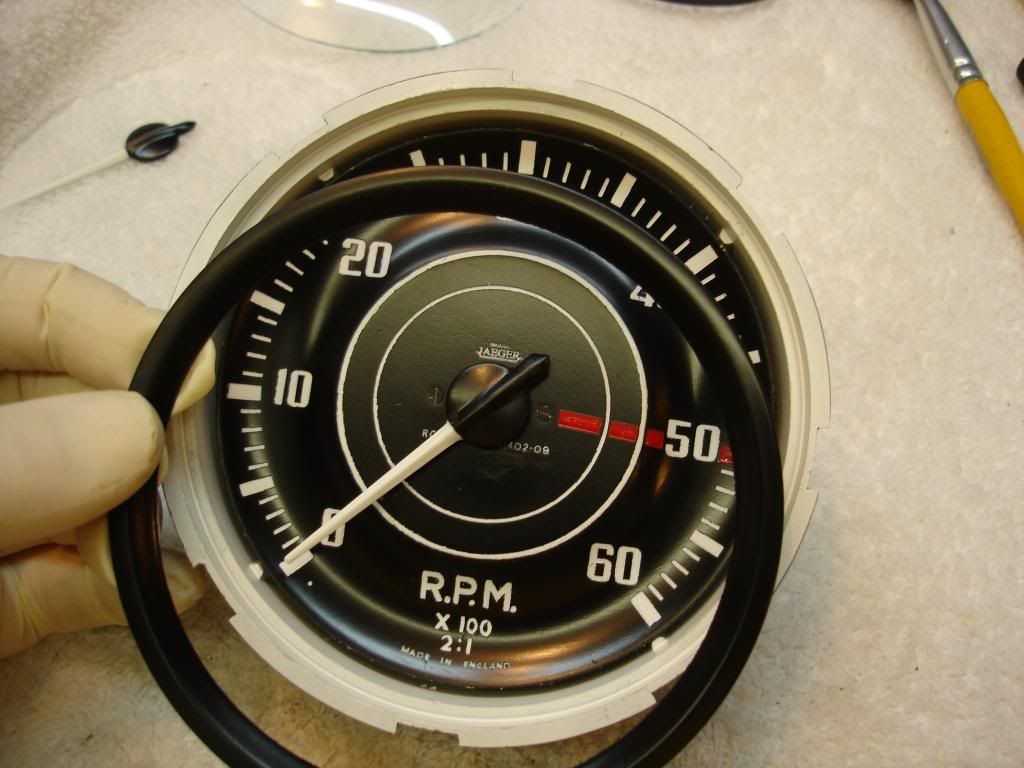

This is the reflector ring that goes in against the face. Make sure the back side is white, or little light will make it to the instrument face. Now we have to clean the glass.
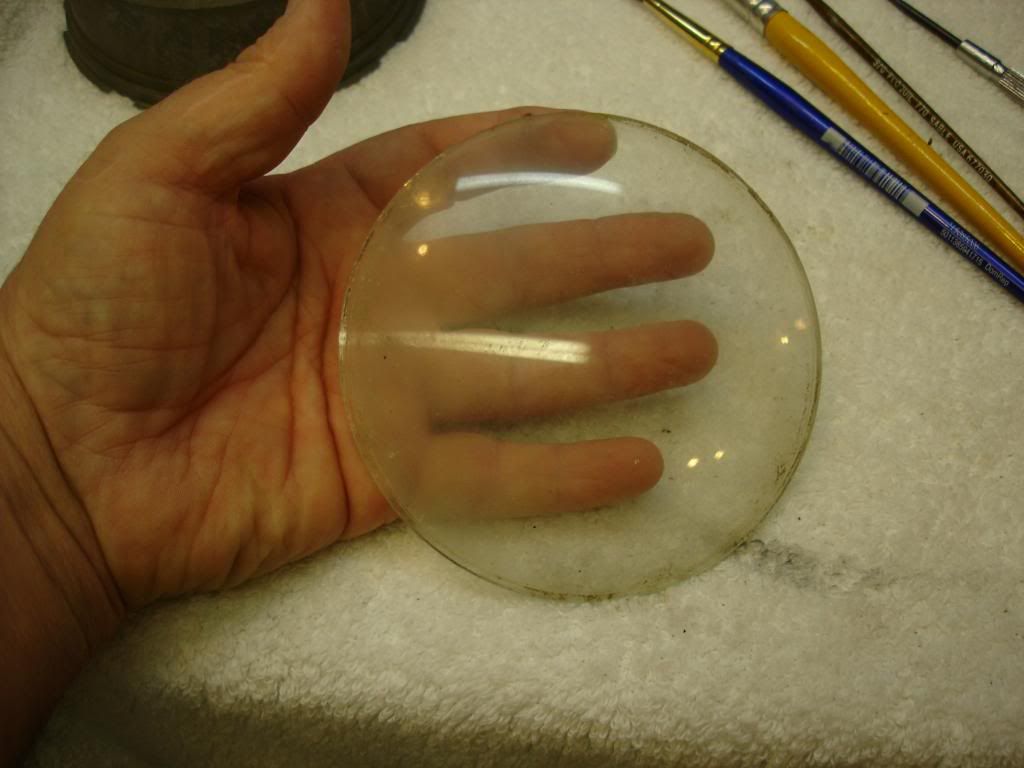
Mine started really nasty. The car sat outdoors for 25 years, and there were water marks showing the tach had filled at some point. I removed the scale with very fine steel wool. I polished a few scratches with a buffing wheel on a drill press, and then finished with windex.

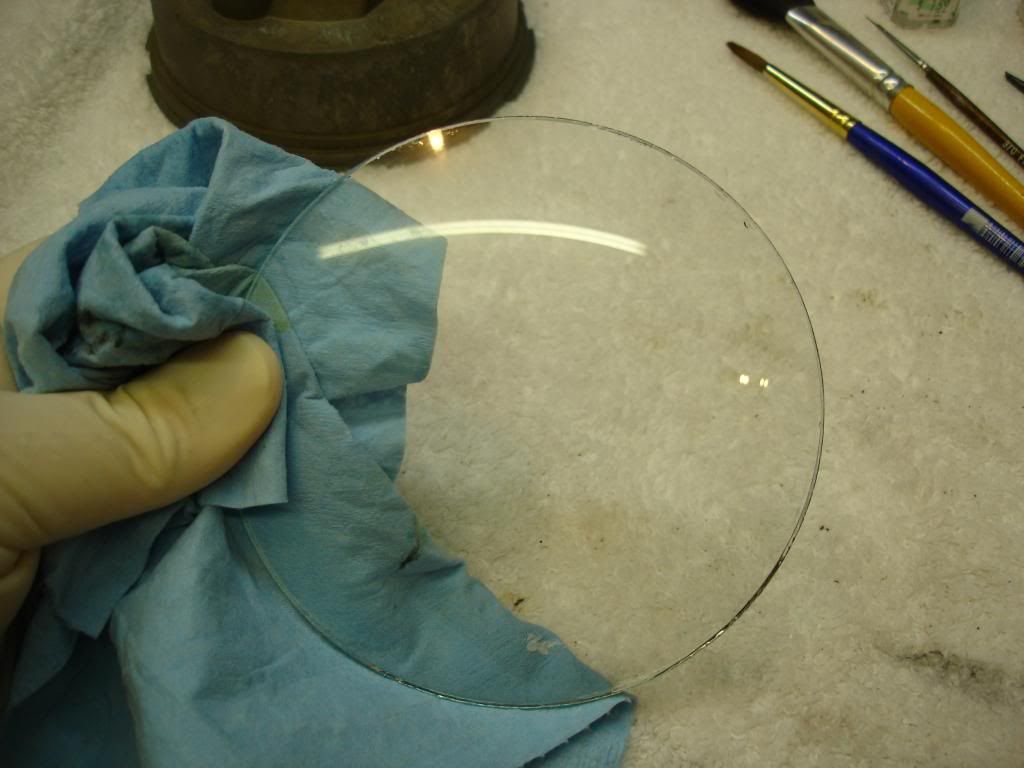
Now I broke out the new bezel and seal from Nisonger's. They charged $120 for the 6 bezels and seals. Highway robbery for what you get...but they have a corner on the market, so I had to fork over the dough. Maybe one of you guys have a cheaper source you can let us know about.

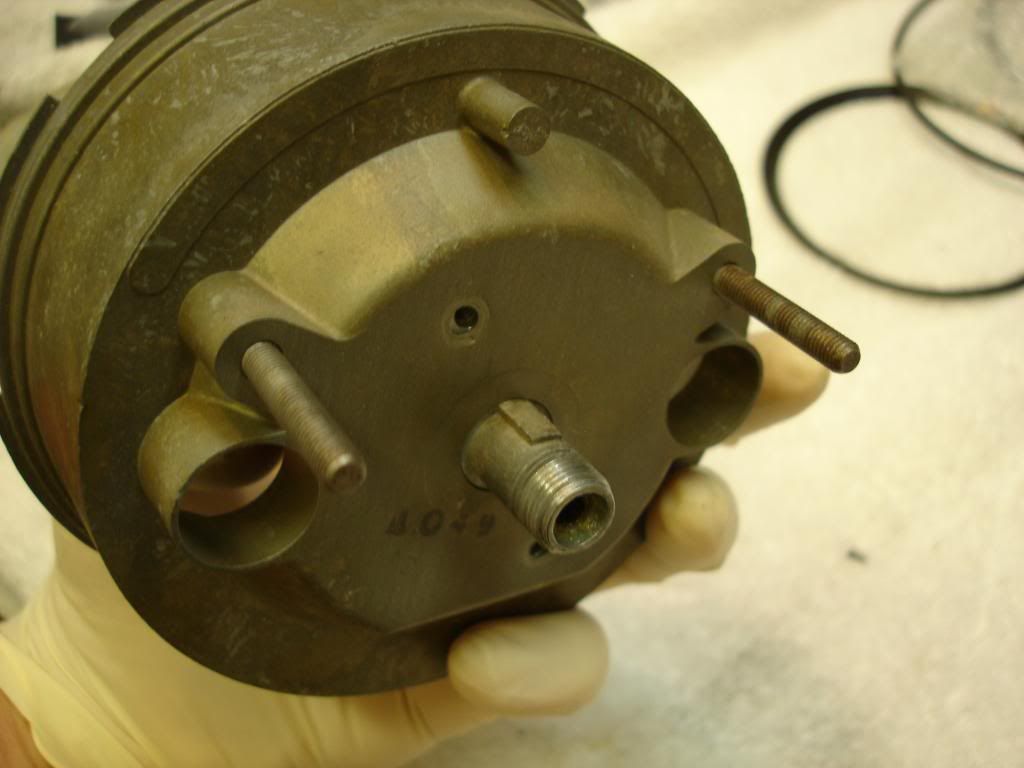
First, the assembly we have been calibrating goes back in the case. You will likely be confused, like me, as it can go in both the right way...and upside down. The key on the drive dog goes upward, as shown. The case mounting studs also go to the top.
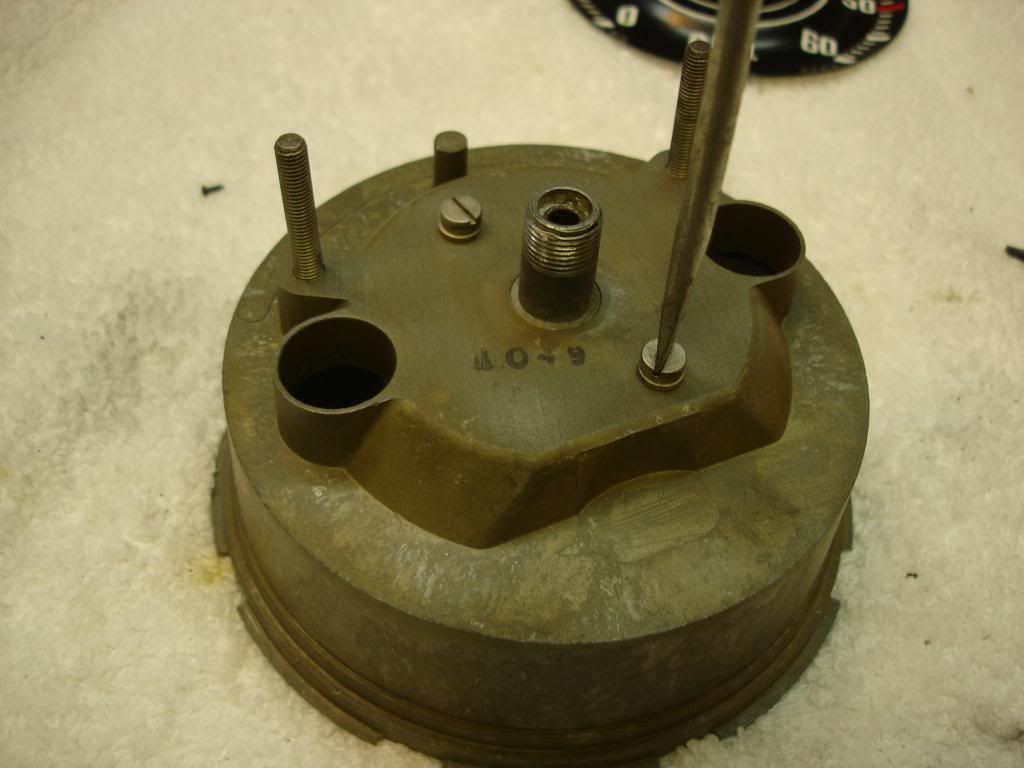
Secure the two screws with washers to hold the frame in the case.
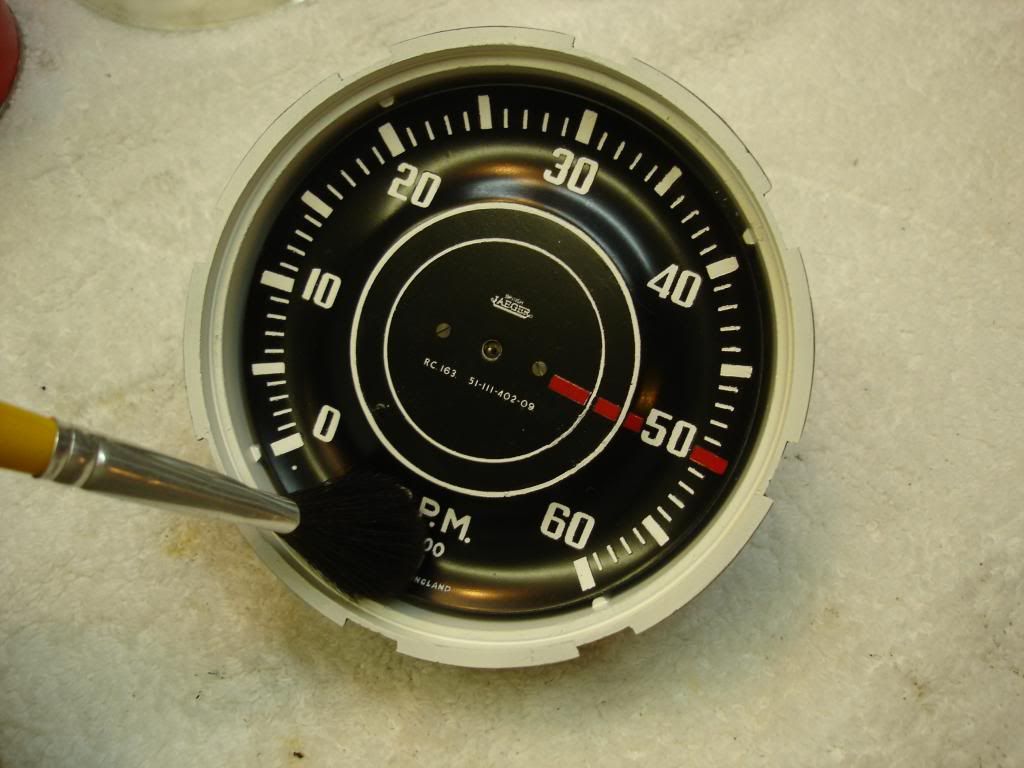
This is the last chance you will have to make sure the unit is dust free. I blew with air and then dusted the face with a very soft brush. Ignore the fact I have no needle on at this point...yours should be on.
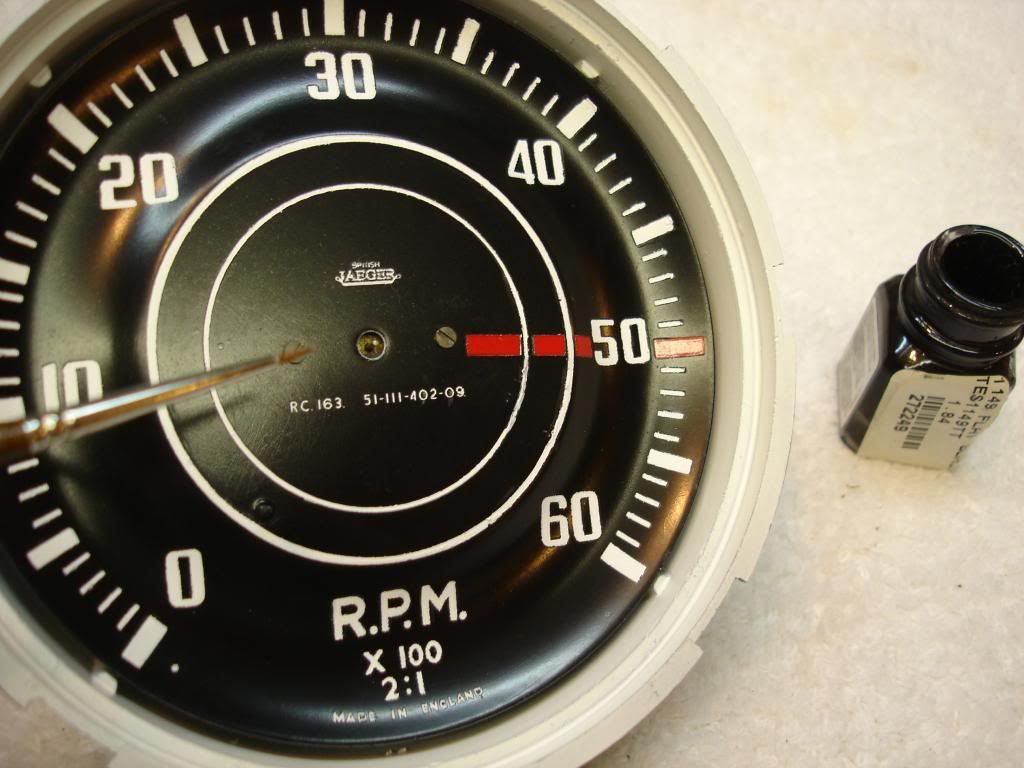
I did a final touch up on anything that needed paint. The face mounting screws were a bit tarnished, so they got a dab of black paint, along with the needle stop post.

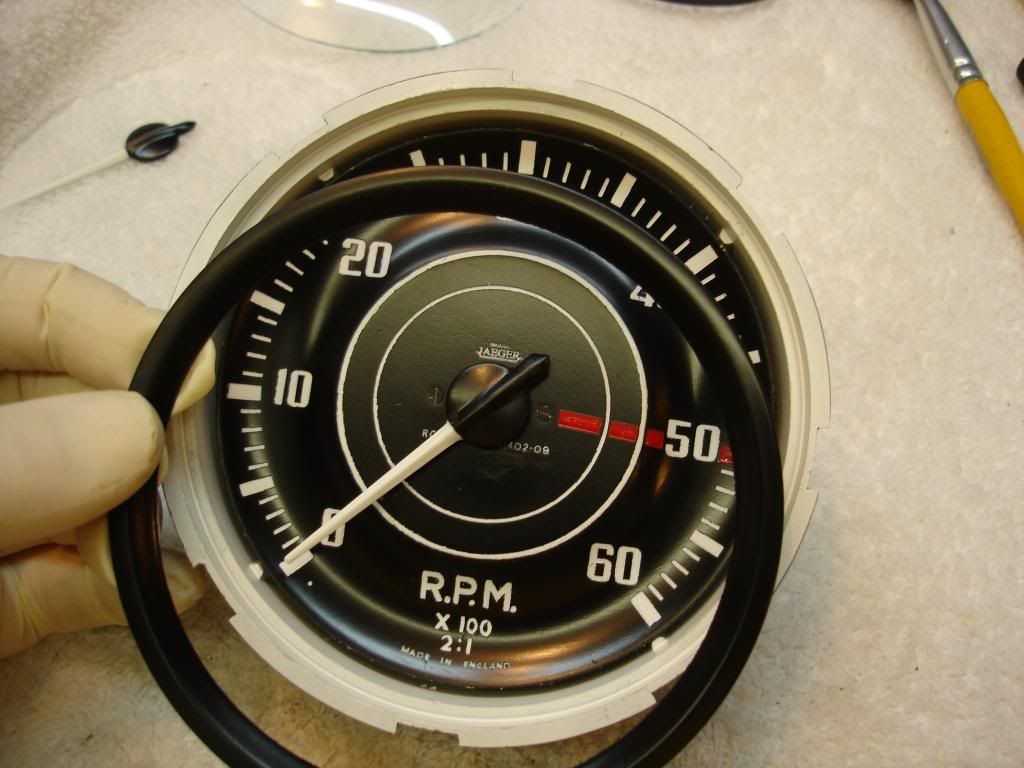

This is the reflector ring that goes in against the face. Make sure the back side is white, or little light will make it to the instrument face. Now we have to clean the glass.
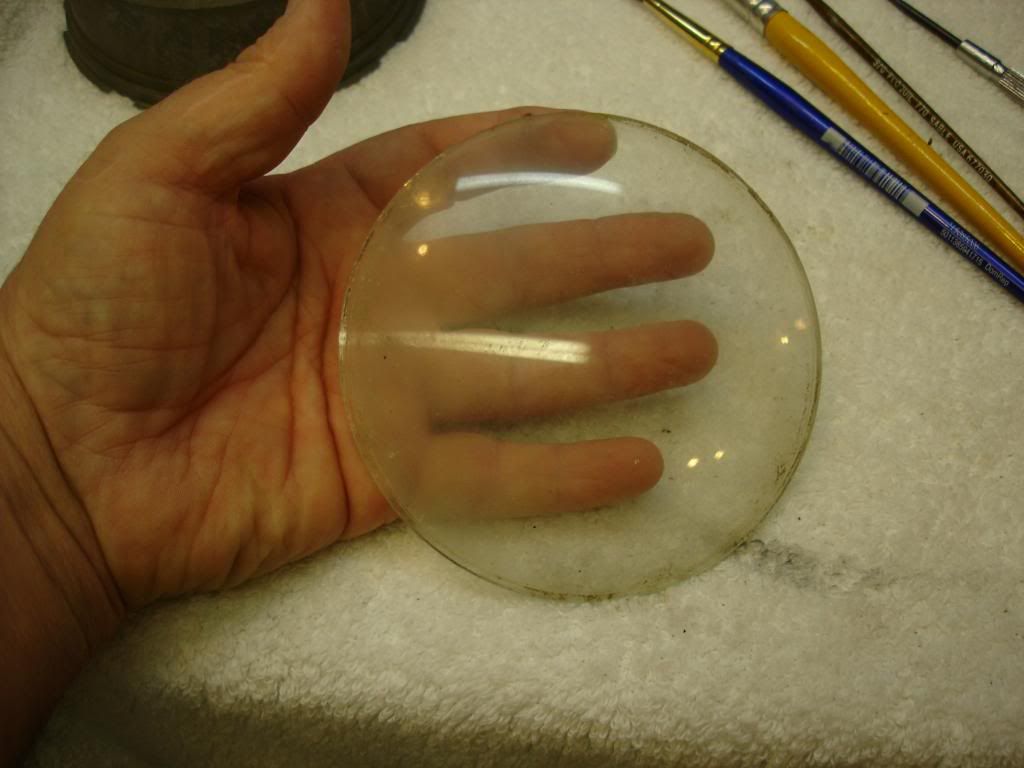
Mine started really nasty. The car sat outdoors for 25 years, and there were water marks showing the tach had filled at some point. I removed the scale with very fine steel wool. I polished a few scratches with a buffing wheel on a drill press, and then finished with windex.

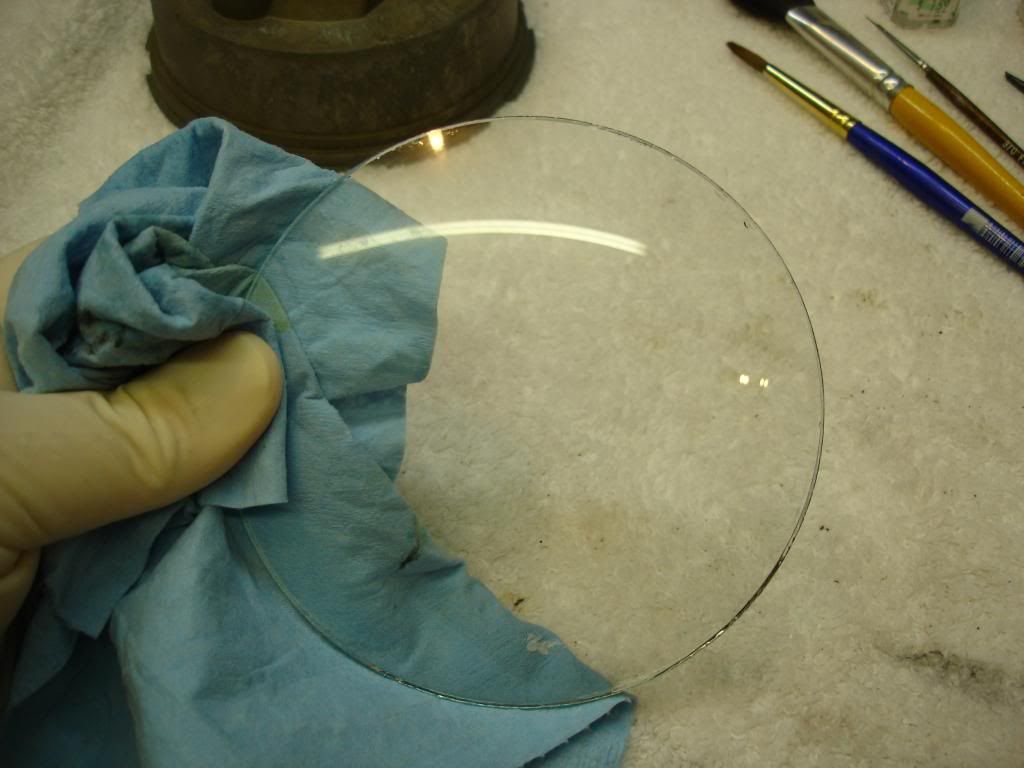
Now I broke out the new bezel and seal from Nisonger's. They charged $120 for the 6 bezels and seals. Highway robbery for what you get...but they have a corner on the market, so I had to fork over the dough. Maybe one of you guys have a cheaper source you can let us know about.
