2wrench
Luke Skywalker

Offline
I received a line drawing with engine parts for my engine
rebuild. I took a photo for reference. It will follow.
Note in big letters: "DO NOT USE LOWER SPRING SEAT," with
an arrow pointing to the part not to install.
Now, I did shave the head down to increase compression.
Got different springs for the head (which are larger than
were stock) to go with the upgrade.
See the line drawing now to show what not to install
when the larger upgraded springs are installed in lieu
of the OEM's:
Out of abundance of caution, I visited the machine shop to
view the head and verify that these parts were not on my
head.
Now the plot thickens as follows:
"2WRENCH Question: So what happens if these little do-dads
(spring seats) get installed with the longer springs?"
"MACHINIST Answer: Excessive pressure from the springs
causing excessive wear on the cam shaft and valve train
parts."
Okay. I aint gonna say this is it, but doesn't this sound
familiar to anybody.....say.....Bill, maybe?
So the line drawing spring seat looks different than the
originals that came off my head (poor drawing? Different design?) Don't know.
Here is a photo of my rebuilt head (no lower spring seats).
Just the new upgraded springs.
I am holding an old spring with the spring seat to show
the heights are equal from old install to new install.
Possible Conclusion?
If new upgraded (larger springs) are installed and the
old lower spring seat is reinstalled as well....could
result in too much spring pressure and undesirable/excessive
wear to cam shaft and valve train parts.
Something to consider.
rebuild. I took a photo for reference. It will follow.
Note in big letters: "DO NOT USE LOWER SPRING SEAT," with
an arrow pointing to the part not to install.
Now, I did shave the head down to increase compression.
Got different springs for the head (which are larger than
were stock) to go with the upgrade.
See the line drawing now to show what not to install
when the larger upgraded springs are installed in lieu
of the OEM's:
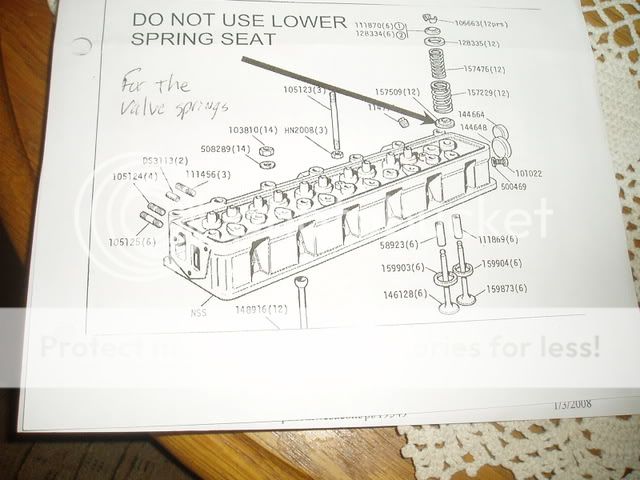
Out of abundance of caution, I visited the machine shop to
view the head and verify that these parts were not on my
head.
Now the plot thickens as follows:
"2WRENCH Question: So what happens if these little do-dads
(spring seats) get installed with the longer springs?"
"MACHINIST Answer: Excessive pressure from the springs
causing excessive wear on the cam shaft and valve train
parts."
Okay. I aint gonna say this is it, but doesn't this sound
familiar to anybody.....say.....Bill, maybe?
So the line drawing spring seat looks different than the
originals that came off my head (poor drawing? Different design?) Don't know.
Here is a photo of my rebuilt head (no lower spring seats).
Just the new upgraded springs.
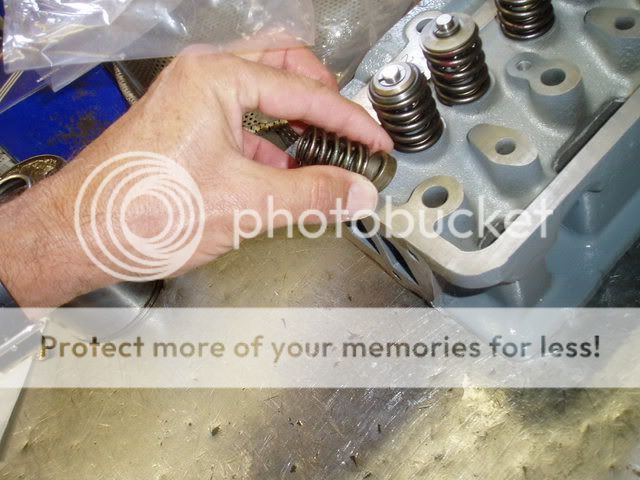
I am holding an old spring with the spring seat to show
the heights are equal from old install to new install.
Possible Conclusion?
If new upgraded (larger springs) are installed and the
old lower spring seat is reinstalled as well....could
result in too much spring pressure and undesirable/excessive
wear to cam shaft and valve train parts.
Something to consider.