My right rear wing started to show some distress with all the hammering. There was a little spot where the tail light mounts that kept "popping" upward. Too much metal from the previous repairs! The usual technique would be to shrink it back to flat. I felt lazy at the end of the day, and not up to removing the 20 bolts holding the wing to work on it...so I sliced the bump, hammered it flat, and welded it back together. The trick was to weld in short bursts to prevent welding the wing to the tub. I'll find out later if I was successful or not?!?
I'm now happy with the boot lid...and the right wing patch.
I spent several hours re-fitting the spare tire cover. No pics, but you'll notice it matches better than before. All a matter of sitting there checking, removing, hammering, rechecking...etc. It sits funny as it needs the seal to hold it in position properly. I am certain it will take more tweaking when I add the seal.
In preparation for the front valence and bonnet, I decided to install the blanking plate and pedal box to stiffen up the firewall. I primed the contact area, and will bolt them in place. The factory painted with these installed. I plan to do the same...so this will be the final installation of these parts...the first parts of their kind!
Funny...I primed and set aside the parts 3 years ago. We're into an archaeological timeline now!
The first permanently installed body parts!!
Getting ready for the valence and bonnet...the front bonnet bumpers go in the forward bolt positions.
i prepped the hinges by lock titing in the studs. It's a pain when you have to remove the nuts 50 times and the studs keep coming out. Threading them in tightly is NOT an option, as the hinges are just pot metal and will not take much torque at all.
First bonnet fitting. Uhg. I realize that the bonnet fitting will try my patience to no end.
This is the upper rear edge of the bonnet. In the TR2's and early 3's, there is no rolled edge...just a bare straight edge. This edge has scared me from the first time I saw it...and now is the time to deal with it. The issue is that a straight 18 gage edge will never be stable. It is flimsy, and yet needs to align with the scuttle.
And the left fit...cringe!
This is the mark I placed on the wing to show where the front apron extends. I guess you see the problem here?!? The bonnet and apron are fighting for the space available. The only good thing I can say is I would rather too much metal than not enough. Let's remove the bonnet and start with the apron...
I installed the aluminum stiffner across the rear of the apron. These bolts use those little star lock washers. Now, a point of order...
Whenever a designer uses star lock washers, he is trying to tell you the doesn't want the bolts torqued tightly, but he still wants them to stay in place. You are torquing a thin metal edge to a thin aluminum bar. Barely more than finger tight is enough! Remember how much I had to straighten the metal tab last year? snug is good!
"Apron Ho!" The apron must align with the front bottom edge of the wings. So it will be installed backwards from the rear wings...start at the front and work back with the bolts. DO NOT tighten any of the out wing to inner wing bolts until the apron is set...the apron determines the spacing between the wings.
Next problem...this is the bracket that holds the aluminum apron bar at the back. It doesn't line up. Bummer. this will be a pain...
Uhgg!
Double ughh!!
This is likely how the factory placed these brackets. It is mounted to the apron, and now the apron will be installed, allowing the bracket to find it's place on the inner wing.
1 hour later...
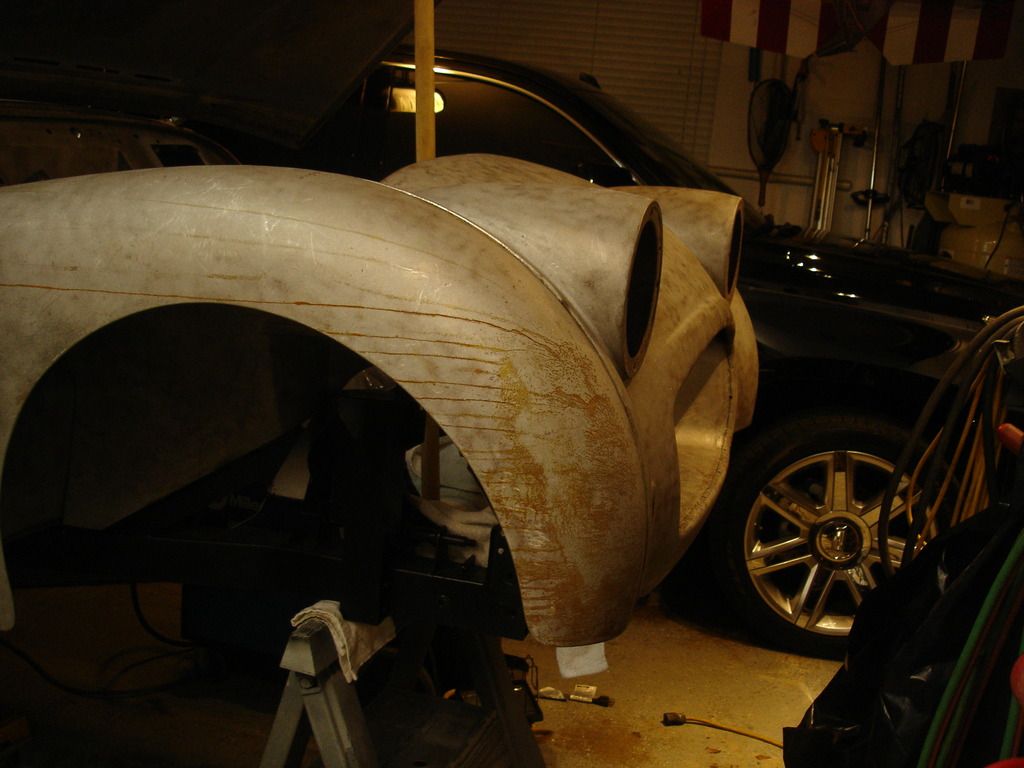