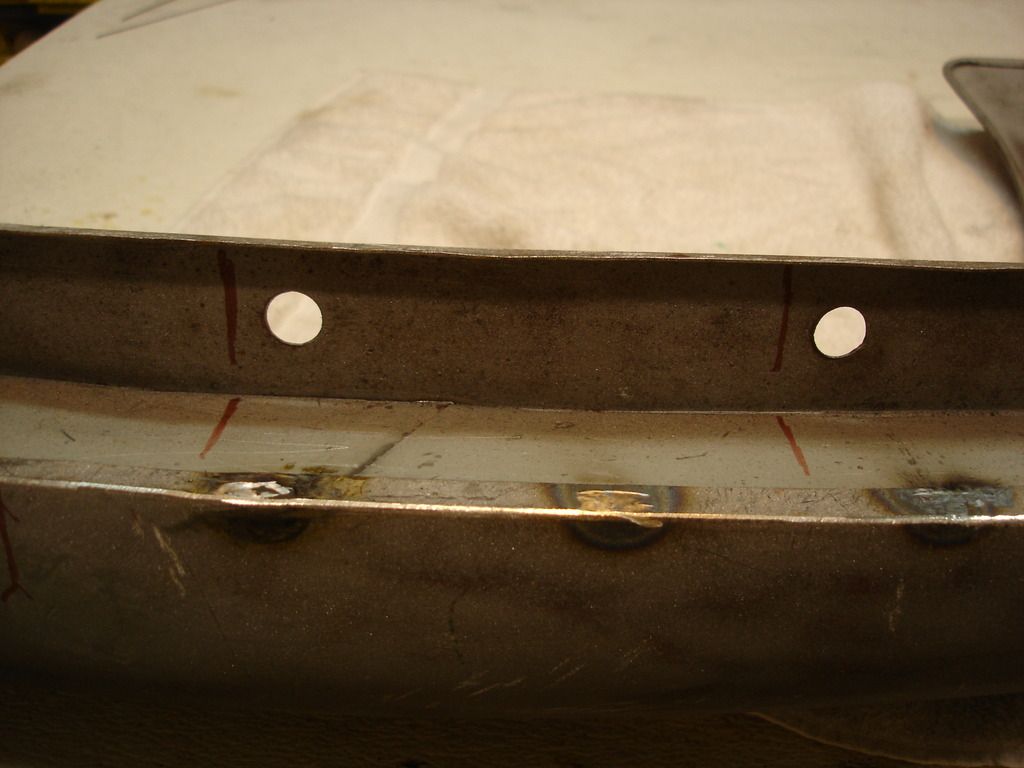
This is the wing sitting back on the work bench. The outside is down, and the mounting flange is comprised of 2 parts. The one that sits vertically is seen in the middle, and the upper flange is the horizontal flange that bolts to the inner wing. The middle, vertical flange sets the curvature of the upper edge of the outer wing, and it is perfect. I do not want to alter it. But, as you can see by the pen marks, the horizontal flange has the holes off, and each by a slightly different amount.
To fix this mess, I will have to break the horizontal flange off, cut it, splice in patches to lengthen the spacing between the holes, and then tack it back in place.
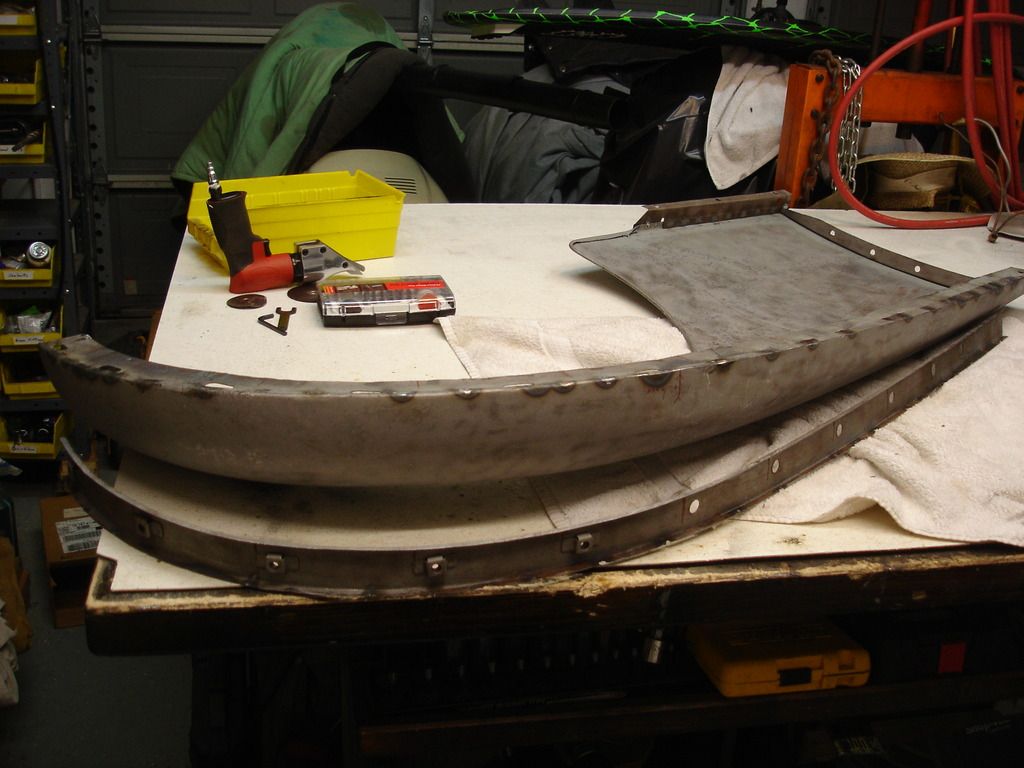
This is the result of the work to break the flange off. It sounds simple, but remember that the welds were towards the wing skin, so you are working in limited space and with a difficult angle of sight. It took a couple hours, but finally came off.
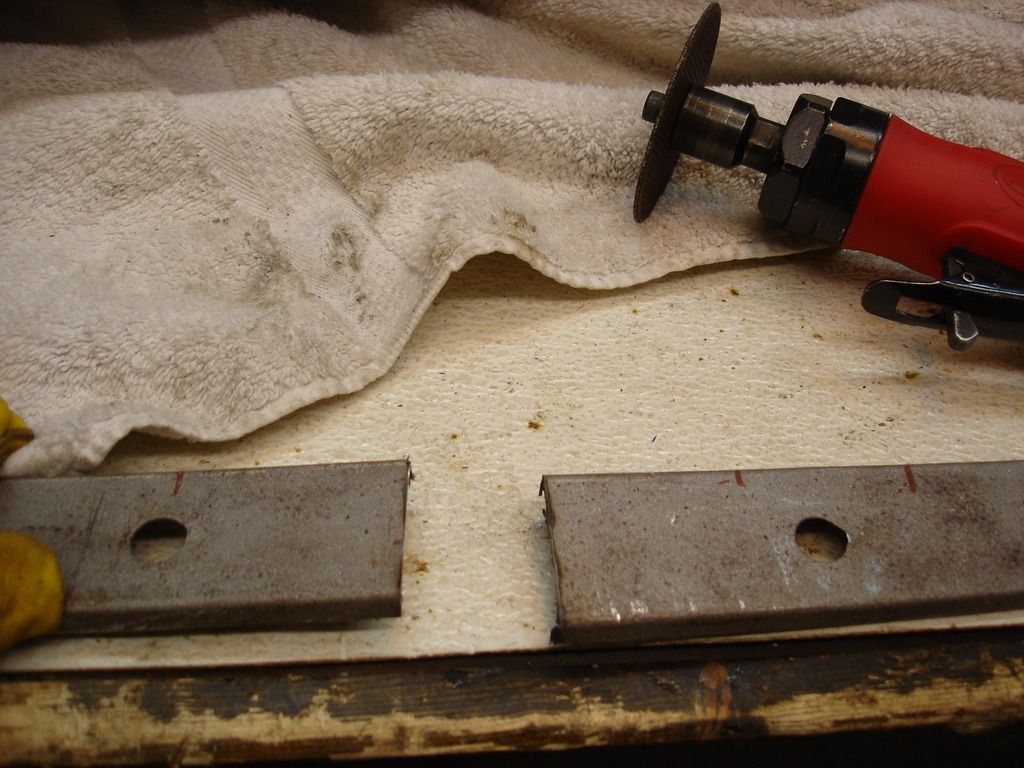
First, the flange gets cut where it is needed to increase the spacing between the holes.
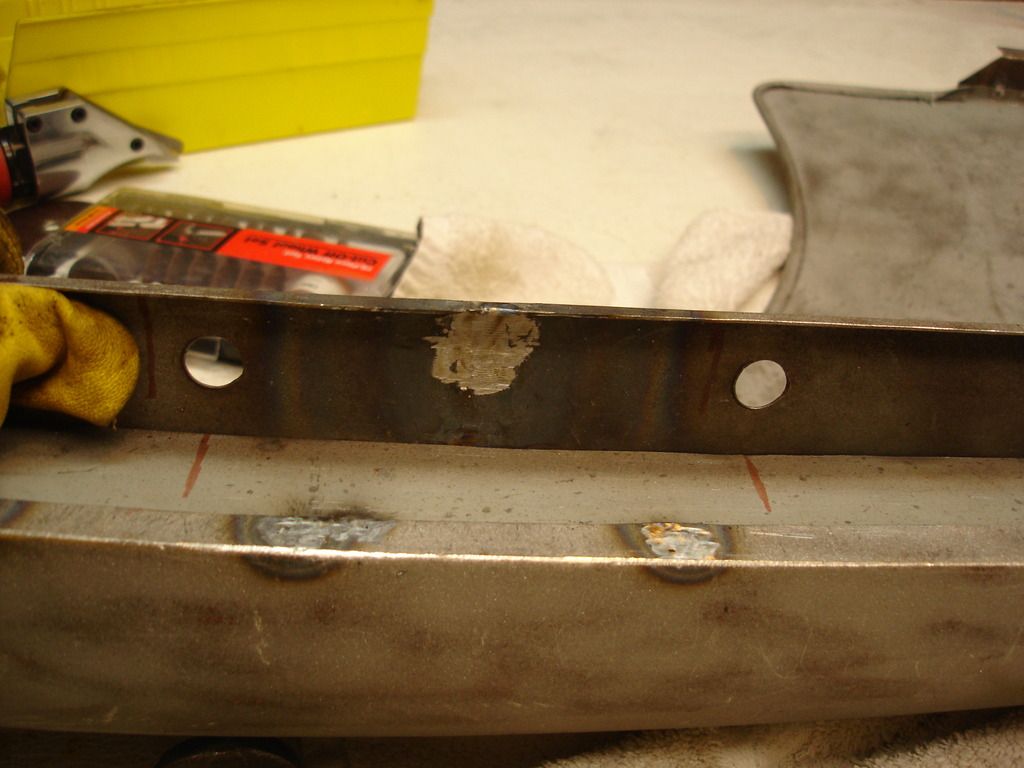
By holding up the flange, I gradually cut and patch to get the holes to line up where they need to.
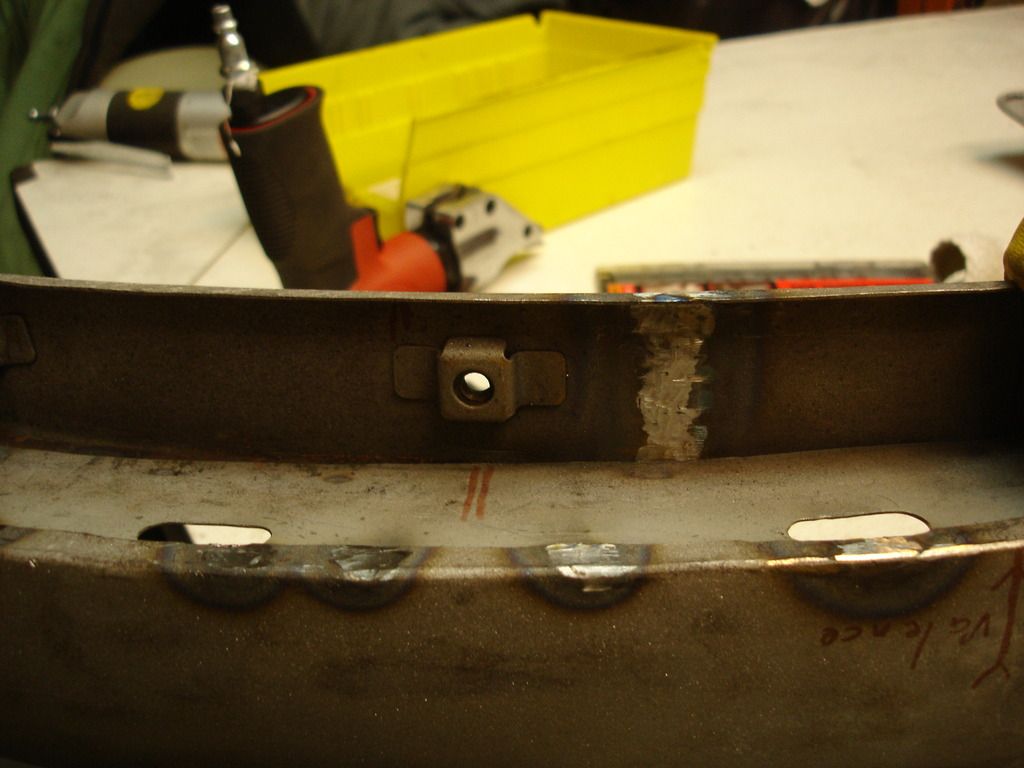
Near the front, the holes change to caged nuts. You can see the splice to the right of this cage where I had to weld in a 1/4" splice. It's a real pain dealing with patches that small.
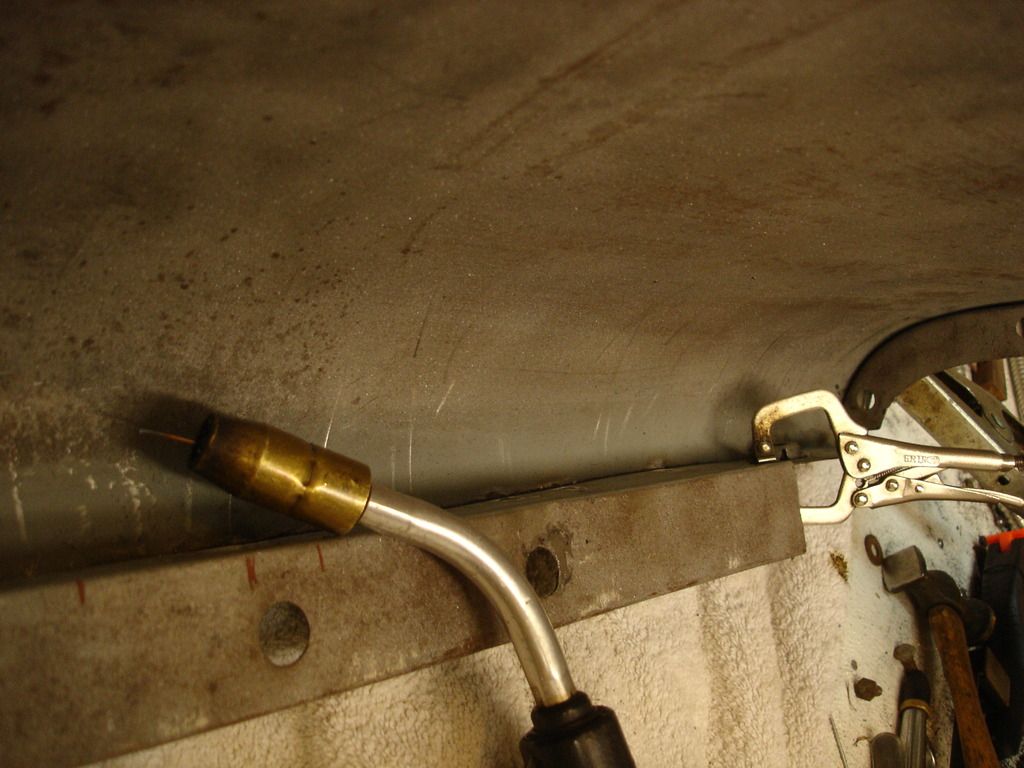
Once extended and patched back up, it's time to put the flange back on. This pic shows the problem with that. To prevent the weld tacks from showing on the top when the bonnet is up, I have to do the tacks on the back/underside. My fat head doesn't fit in that tight space...especially with a welding helmet on.
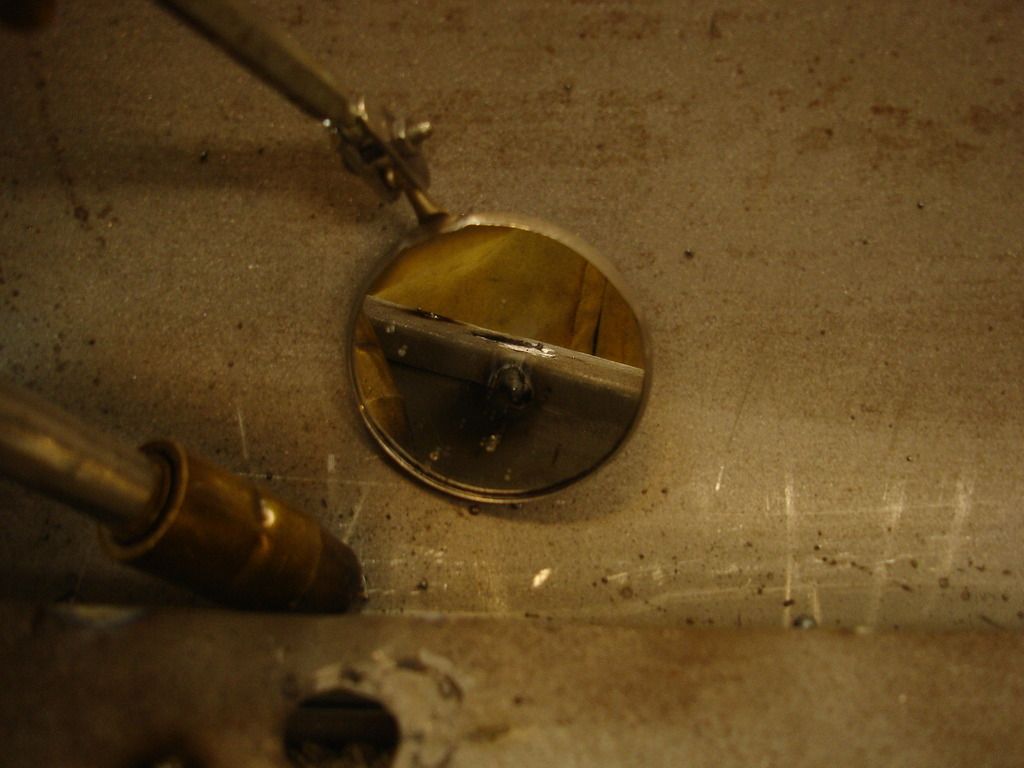
Here is the solution. I had to hold a mirror with my left hand, the welder with my right, and tack the flange while looking at the mirror...like a dentist. Sound like fun? Not so much. But, I did get the flange tacked back on, and the welds are not at all noticeable.
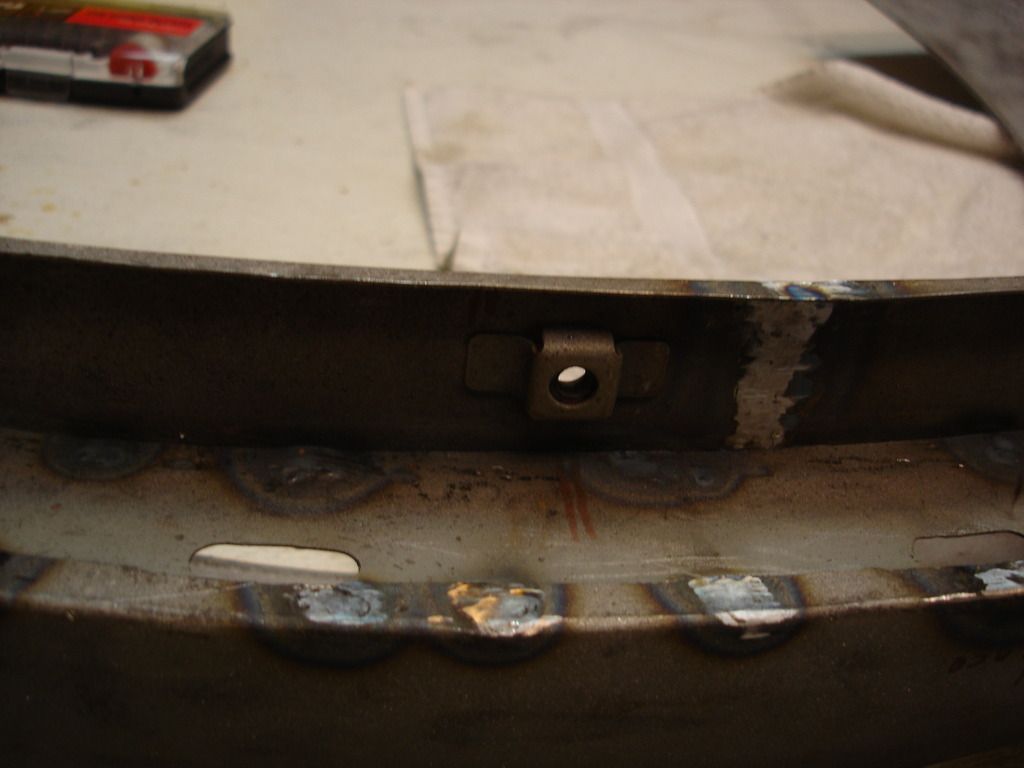
Here the flange is back on, and the holes line up perfectly.
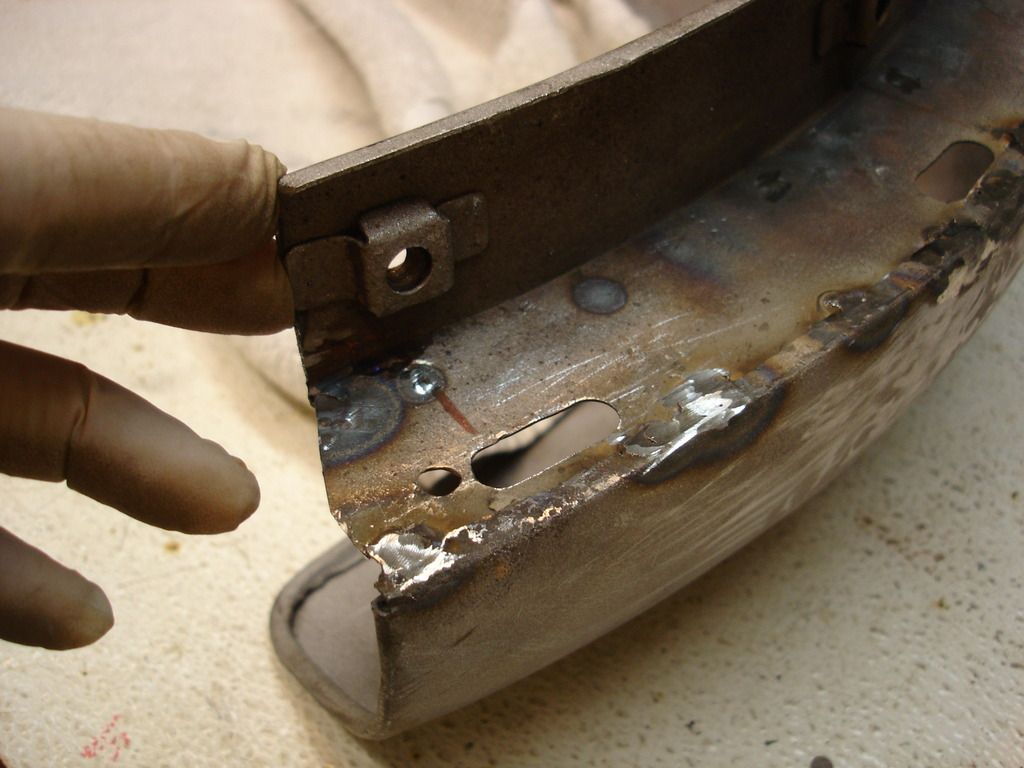
The next issue...the flange hangs down too far at the front. This is an easy one. I just trimmed the extra off.
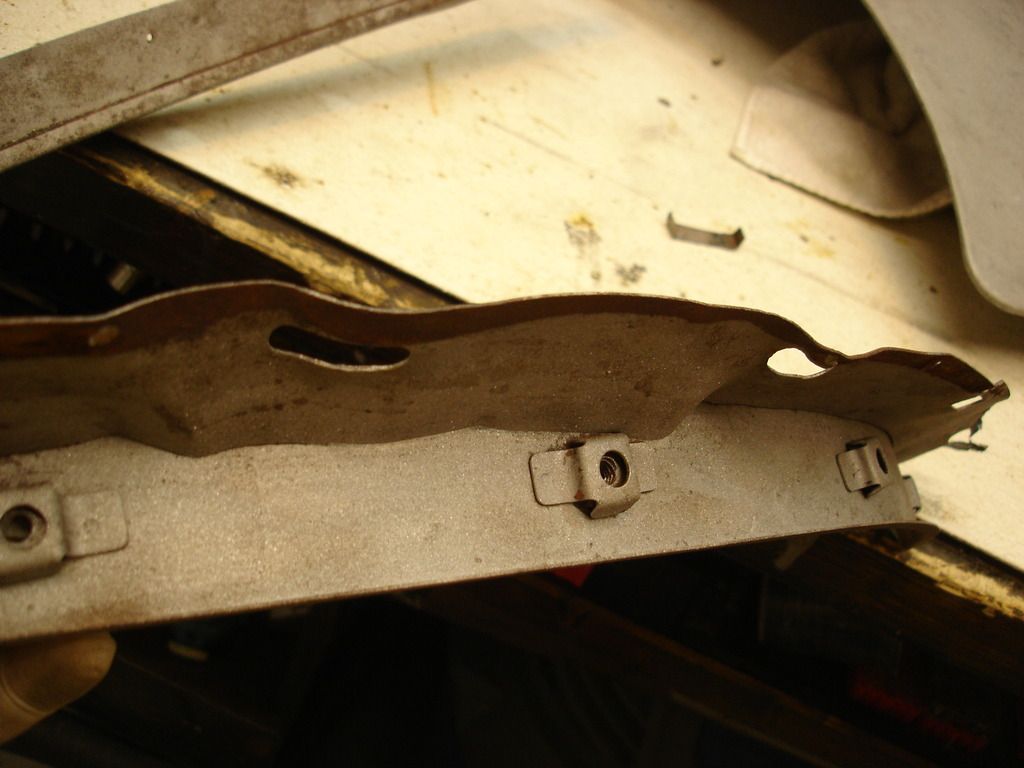
This is a pic of the original flange that was on the wing skin I am using. You can see that the vertical flange part is stretched a whole lot compared to the horizontal flange. I have to assume that my alignment issue was caused by the body work that resulted in the flange stretching like this. No matter...it's fixed right this time.
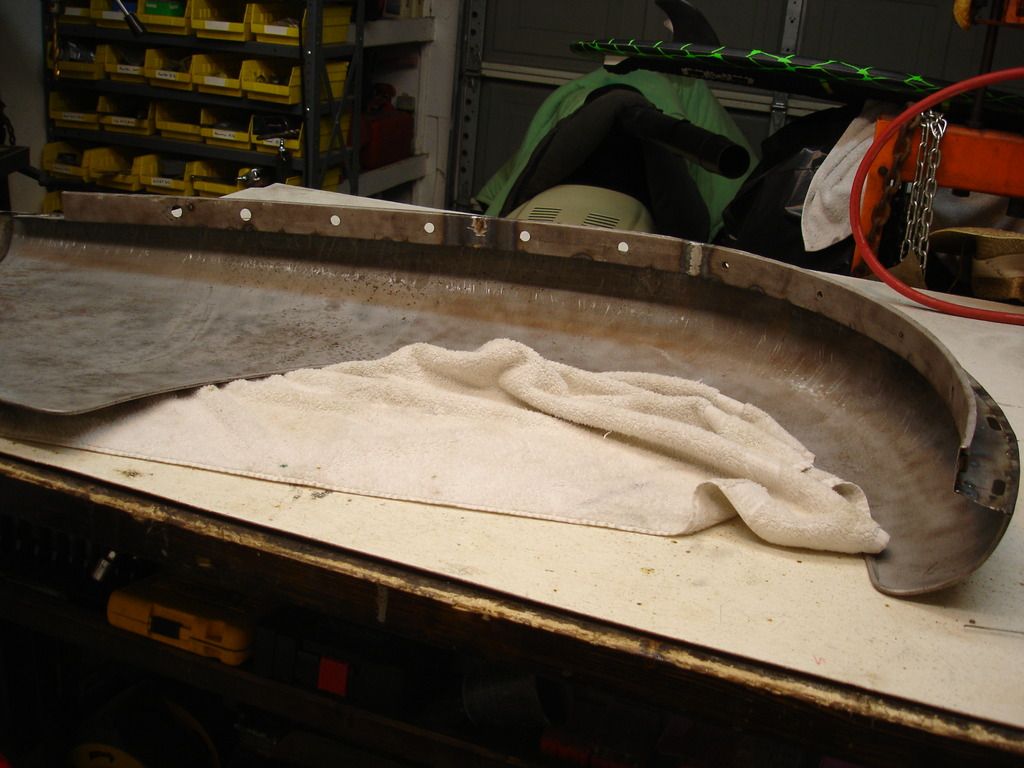
And...once again...the left front wing is finished. Funny, much like the bonnet, I spent the last week on it, and it looks just like it did last week. The thankless job of body work! Everyone notices bad body work, but nobody can tell how many hours went into getting body work right. In the last pic you can see the 2 spots on the flange that took up all the time fixing.
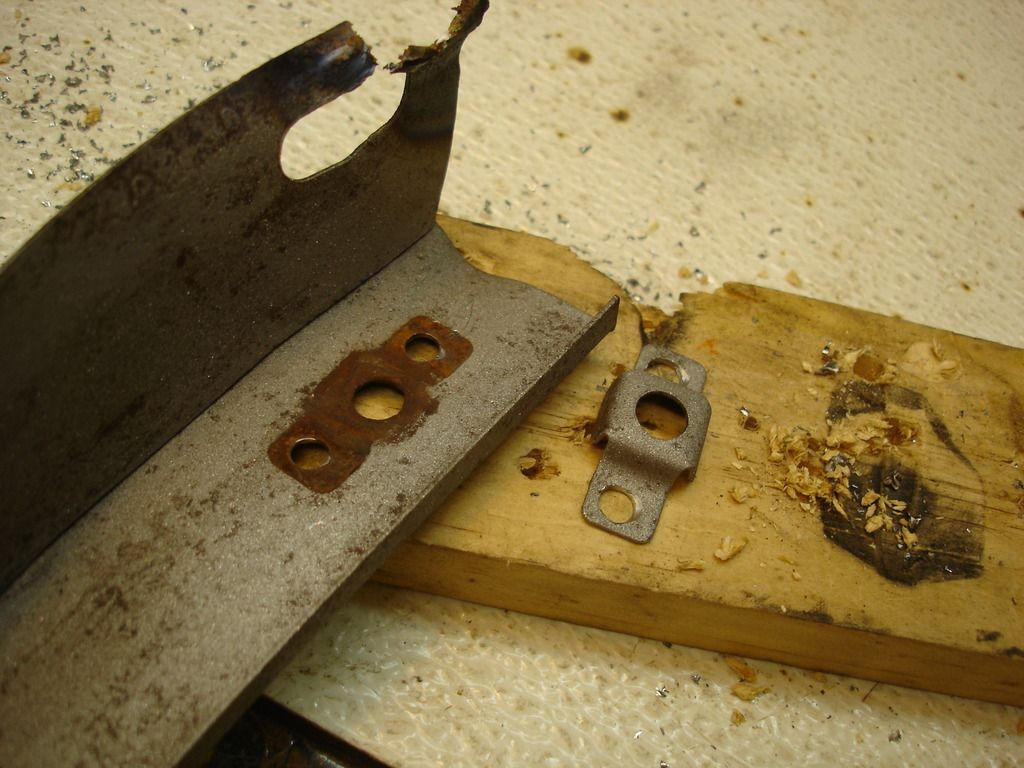
My last project this week was to remove the usable cages and nuts from the spare wing flange before I tossed it. These will, no doubt, come in handy later...