John I thought about aluminium but had some left over steel sheet plus I had been working on my tig welding of steel so went down the traditional pathway. Not like I am going to be racing the car either as just getting it together will be an accomplishment.
Thanks for the support Graham and also for the opportunity to check out your car the other day. A top notch job.
Continued with the front part of the mudguard. Actually considered stopping and starting again this morning as I was having a lot of trouble shrinking the outer circumference of the panel. In retrospect it would have been easier to do the outer part separately to the inner and weld the two together. I did this with the rear inner wheel arches as they were too deep for me to shrink them to shape. I try not to stretch too much and thin the metal. Prefer to increase the thickness by shrinking.
Anyway I persevered and then it started to come together. I ended up cheating and resorting to using the shrinker to get the last rough profile to shape. Also decided to make myself a tuck fork to get some shrinking deep in the panel. Together, they did the job.
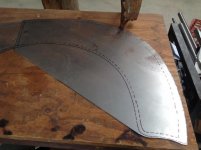
The following photo shows the mangled piece of metal after hammering on the block to shrink the outer edge. At this stage I was having difficulty getting the shrink deep enough into the panel and so I took time of to make a tuck shrinking fork which is shown in a later photo. This allowed me to reach in further from the edge of the panel and start my shrinks deeper in. At this stage, it always looks really ugly. Sometimes I roll it on the wheel just to make it look better and I feel that it is progressing
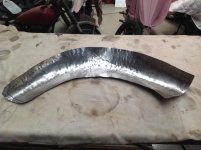
By the following photo I had spent quite some time using the sandbag to create the main shape and the wheel to raise some areas and also smooth it. To get the metal to fit the pattern, I had to resort to the shrinker to tighten the profile.
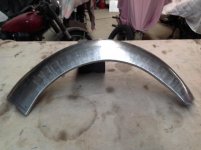
I used the bead roller to break the flanges and then hammer and dolly to complete the bend and tighten the radius of the bend. When the flange is bent over there is either too much metal or too little metal depending on whether it is on an inner or outer curve. This totally stuffs the lovely profile that previously existed. The shrinker stretcher is used on the flanges to get the correct curve back into the outer and inner radii of the panel. So at this stage it is a necessary to present it to the car body to get the correct outer radius and line along the body panel. Also it has to be compared with profiles to get the correct curve back in the body of the panel.
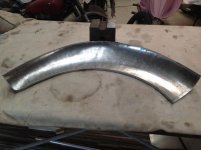
It turned out OK. You can see in the following photo the tuck fork I made to get deeper shrinks on the panel.
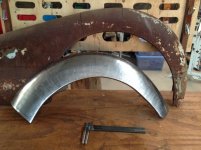
Rather than spend a lot of time building a full buck to make the panel, I made a paper pattern and then supplemented it with a number of profiles I copied from the panel. These profiles match what the professionals refer to as stations on the buck. I marked the panel and the sheet I was forming and used the profiles to determine how I raised or lowered the metal at several locations. You may be able to see on the above photo lines where each profile relates to the panel. They can be seen on the old fender as well.
Now to join the two halves together. You can see that I deliberately split the two halves at the thinnest section of the fender. My welding is not my strong point so I try to minimise the length of my welds. Another reason I wanted to do the guard in two pieces rather than three.