I put the gearbox in 4 gear then clamped both the input and output of the gearbox with the hope that if nothing moved it should just side back together. Setting it up on a stand so it would not roll around.
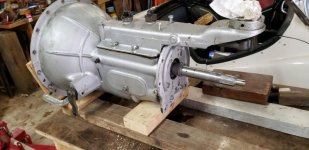
This was after the OD was removed obviously.
Started to get it separated but was a little suppressed that it took a lot of effort to get it apart. Removed the 4 nuts on the short bolts then started to back off the nuts on the long bolts. I was expecting the springs to push the OD away from the gearbox. It did not move so I did a little tapping then got a block of wood and tapped on the OD. Still nothing so finally I got a tool like a putty knife and tapped it into the join between the adaptor plate and the OD. A gap started to open up and with a little help the springs pushed it apart.
The gray sealant (Yamabond) I think stuck the parts together and some was in the bolt holes.
This is a photo of the adaptor surface to OD. You can see it was not making good contact. Either the face is badly distorted or the sealant dried before it was closed up.
Cleaned everything up then applied Permatex 51813 to both surfaces if the gasket between the new adaptor plate and gear box. Bolted it up having put some blue locktite n the bolts.
Luckly the OD pump cam was sitting in its minimum pumping position when I took it apart. I have seen where you have to hold the pump plunger down with a wire so the roller will clear the cam on the main shaft.
I had found a site that posted photos of a tool that is poked through the hole located under the brass plug and hooked onto the pump shaft.
Having cleaned up the OD face I applied Permxtex to both faces of the gasket and slid the OD on the shaft. It seemed to line up OK and as I pushed it together I checked the springs were located on the cast points on the adaptor plate. The short springs can be slid along the pins to do that.
Using a board against the end of the OD I pushed it together till I got nuts on the long bolts. I continued pushing and taking up the slack till I was about 1/2" from closed up.
At this point it went tight so I thought the splines were engages so I took my clamps off and turned the input shaft a bit. It freed up so I closed it up more turning and tightening. Turned mu tool to release the pump plunger and finished tightening the bolts. I did remember the top nuts that have to go on before the long bolts are completely tight.
I plan to run it with a motor for several hours to check for leaks.