
Offline
So the saga of the rust rotted wheel wells continues with some great progress.
First let me say that I haven't worked on the car for several weeks. Who am I kidding, months! But once I got back into the swing of it and I see some progress I am getting more excited to get the C back on the road.
I've been working on cutting out the rusted wheel well section that you've already seen and then replacing with a fabricated patch panel. Since I don't have a welder nor do I wish to purchase one and learn to weld I decided that since the section that needs replacing isn't a structural part I could use JB Weld epoxy adhesive to glue the panel in place.
If they can glue parts of a 747 together using epoxy surely my C wheel well panel will stay together.
When you look at the pictures of my progress keep in mind that I'm working with a very limited budget and a standard set of hand tools, wrenches, clippers, grinders, etc. etc.
Welding the patch panel in place may be the ideal way to fix the rust issue, but don't judge until you see the outcome. If I offend any professional body and fender guys with my weld-less panel fix I apologize and I invite you to come on down and show me the right way to do it. At your expense of course. LOL.
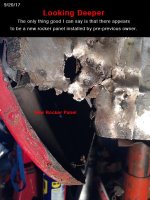
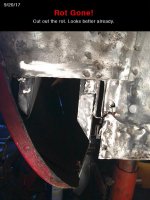
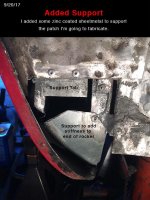
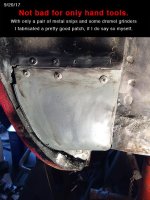
First let me say that I haven't worked on the car for several weeks. Who am I kidding, months! But once I got back into the swing of it and I see some progress I am getting more excited to get the C back on the road.
I've been working on cutting out the rusted wheel well section that you've already seen and then replacing with a fabricated patch panel. Since I don't have a welder nor do I wish to purchase one and learn to weld I decided that since the section that needs replacing isn't a structural part I could use JB Weld epoxy adhesive to glue the panel in place.
If they can glue parts of a 747 together using epoxy surely my C wheel well panel will stay together.
When you look at the pictures of my progress keep in mind that I'm working with a very limited budget and a standard set of hand tools, wrenches, clippers, grinders, etc. etc.
Welding the patch panel in place may be the ideal way to fix the rust issue, but don't judge until you see the outcome. If I offend any professional body and fender guys with my weld-less panel fix I apologize and I invite you to come on down and show me the right way to do it. At your expense of course. LOL.
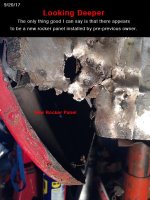
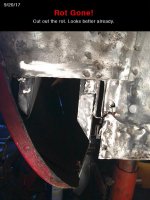
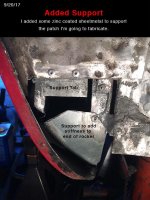
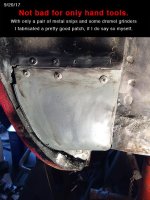