On to the weeks work, the spare tire cover.
SHRINKING METAL
So, frequently in body work you run into stretched metal. You know the panel is stretched when you cannot get a high spot down where it belongs. Frequently you tap a high spot, and it moves over a few inches. You tap the "new" high spot, and it moves over again. After making a fool of you for several tries, you finally realize there is too much metal to lay flat! Bummer!
This is common since when you are in an accident, another car or something smacks your body very hard. You then try to straighten it out with a hammer, and somewhere along the way the metal gets stretched. Another symptom of a stretched panel is the infamous "oil canning". This is when you press a panel and it goes "pop", and sticks inward. You push from behind, and it once again goes "pop' and comes back out. It is stretched out of shape and must be shrunk back to proper size and shape.
My tire cover was stretched, and provides a great lesson on shrinking metal.
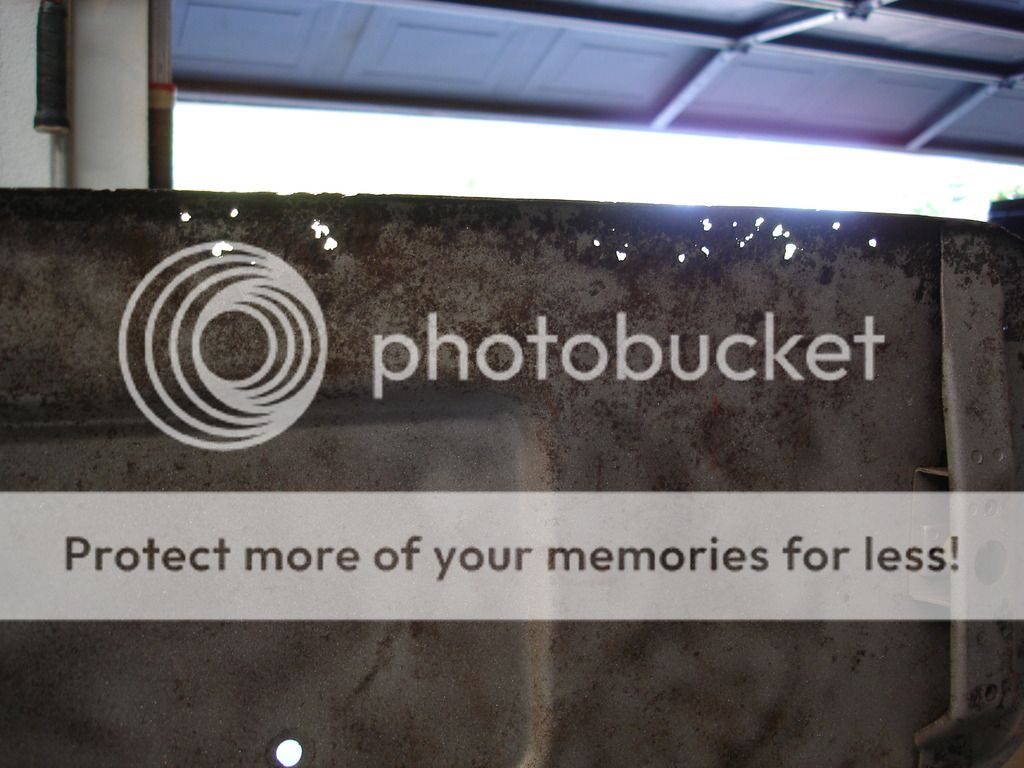
This view shows my original tire cover after sand blasting. Amazingly, there was not a single through hole prior to the blasting. Isn't it phenomenal what paint can cover!?! I considered using Marv's spare car cover for material to weld into the bad area...but it was just too extensive. I will have to use the spare TR3 cover for my base.
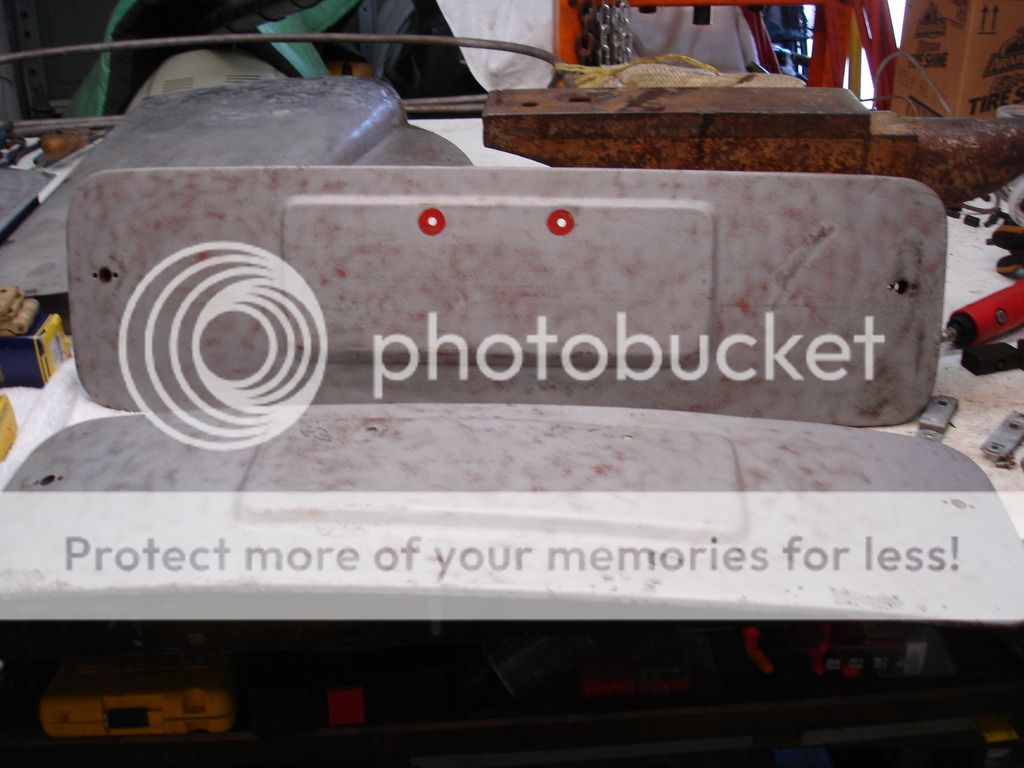
The TR2 cover is lower in the pic. Although the shape of the covers is identical, the holes for the license plate are different. I will have to re-drill the cover and fill the TR3 located holes.
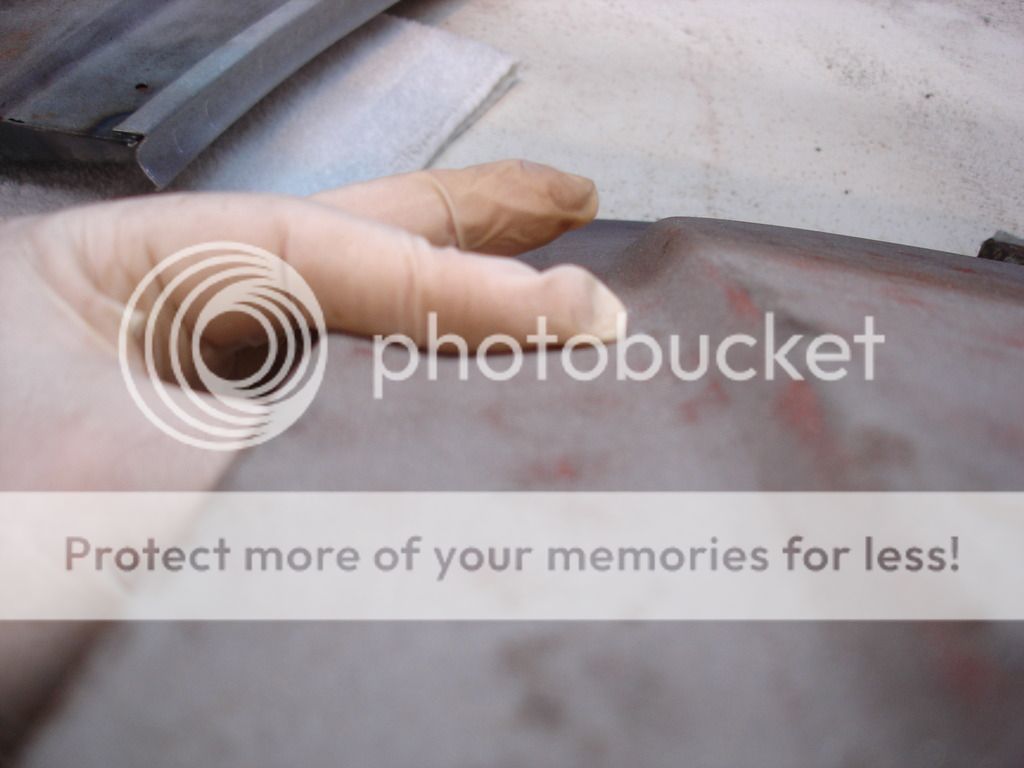
The upper edge of the newer cover is dented in, so that will have to be worked up.
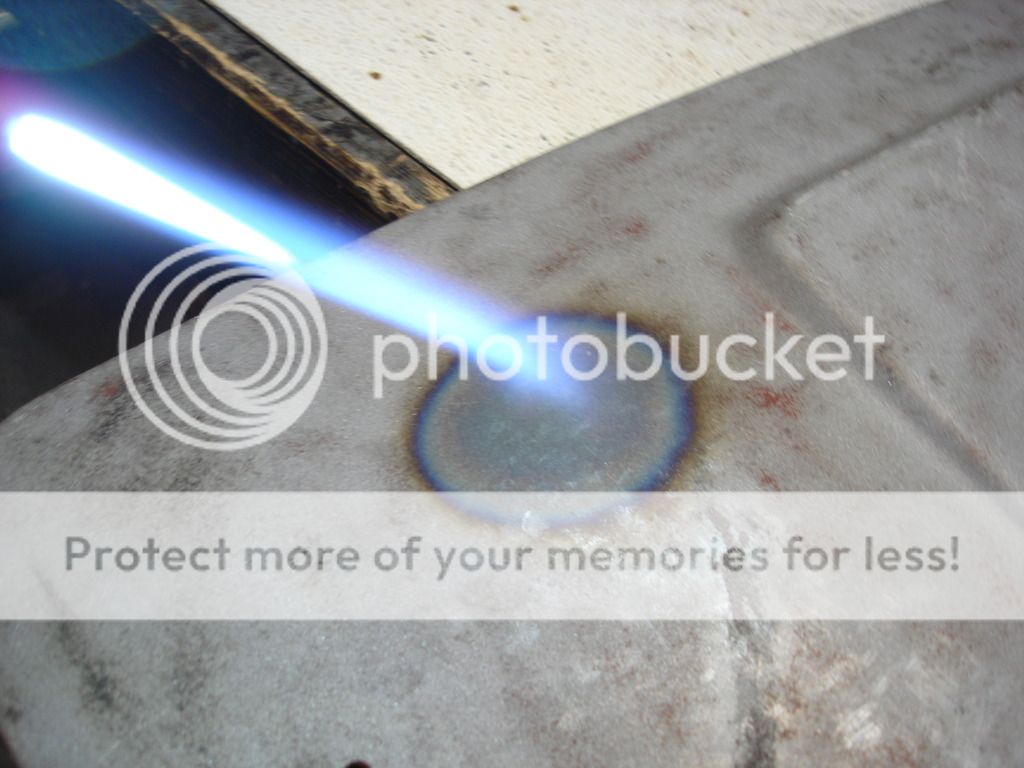
When I worked the dent up, there was one area that did not fit back into place, so here is the process I used to shrink the metal. First, I locate the center of the high spot using my hand as a detector. Then, I heat the spot red hot with a torch. I am using Oxy-acetylene, but even a propane torch gets hot enough for this work. When you heat, it is frightening how much the heat expands the metal in one spot and causes a bump to form!
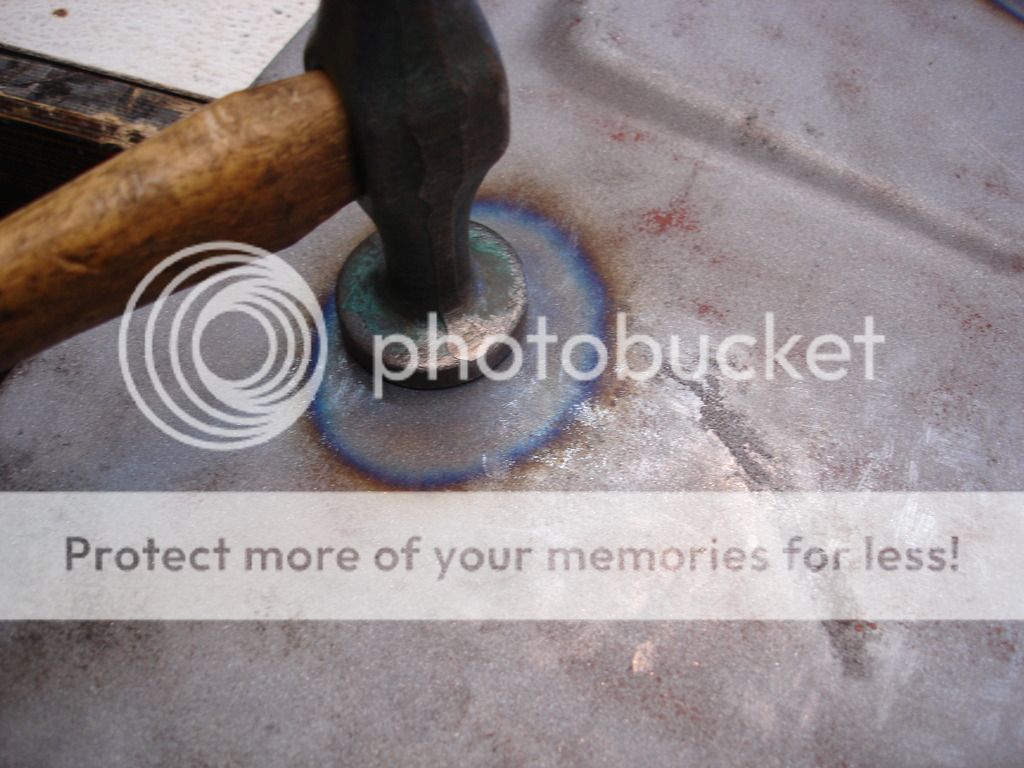
Then quickly, while the steel is still glowing red, use your hammer and dolly to gently tap the "bump" back flat. The tapping while it is red hot is "jamming" the steel against itself, so it forces it to shape. Once it cools, the "bump" will actually shrink enough to become a flat surface.
So, the process is heat the metal red hot to form a red hot bump. Flatten the bump to near flat using a hammer and dolly, so now you have a red hot, very small, bump. Allow to cool. Then finish shaping with the hammer and dolly. That's it.
If you plan to work the metal more, let it air cool. That keeps the panel relatively soft and ductile. If you have a problem area, that needs a lot of shrinking and possibly several iterations of this procedure...or it oil cans still...use a wet rag to rapid cool the spot. That hardens the metal to prevent oil canning later.
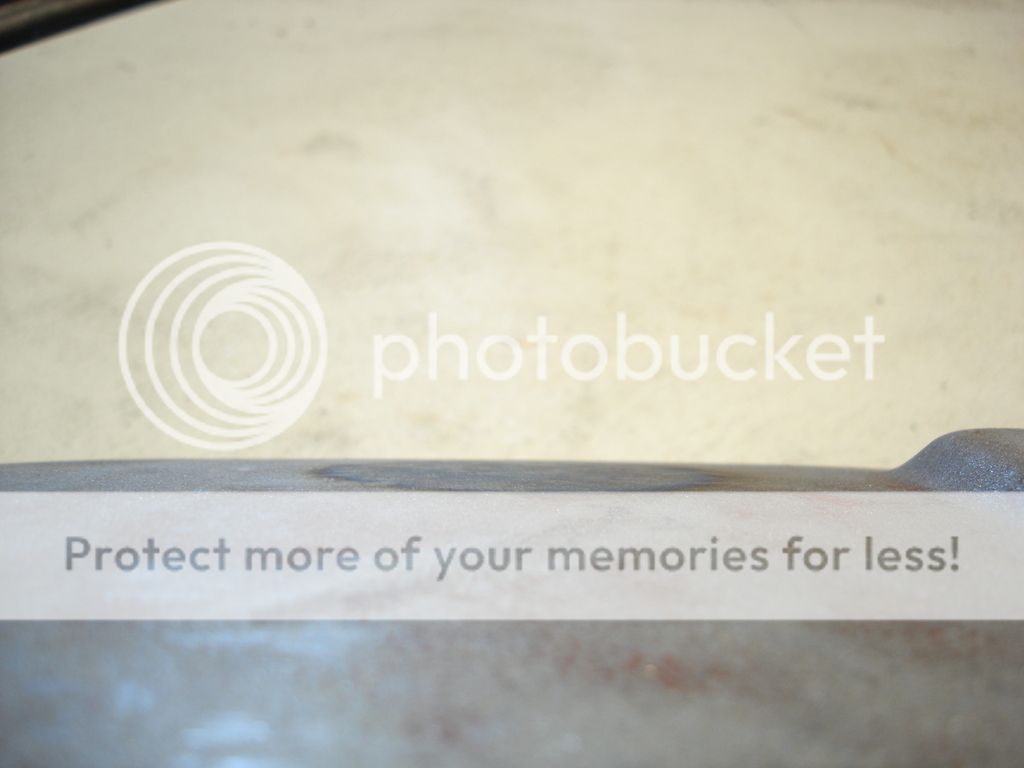
This is an edge pic of the spot after air cooling. The bump is gone, and the panel is actually too flat now. That just takes work with a hammer and dolly to stretch it back out the correct amount. Stretching is easy...shrinking is not.
Worth noting...as you can see, after heating the metal red hot, it retains that "blue" discoloration, even after the cooling. You have to learn to entirely ignore the color as you work the metal. I frequently get distracted by the different shading, so I close my eyes as I pass my hand over the area to look for high and low spots. You learn to believe your hand and ignore the visual cues. If the discoloration bothers you a lot, you can always run the sand blaster back over it it to remove the discoloration. I don't bother, as long as I know the shape is true.

Don't be afraid to do the same thing anywhere you have high spots that won't work out. Here the adjacent area is still to stretched. It is best to work in several smaller areas, rather than trying to do the entire panel at once.
And that is shrinking...101.
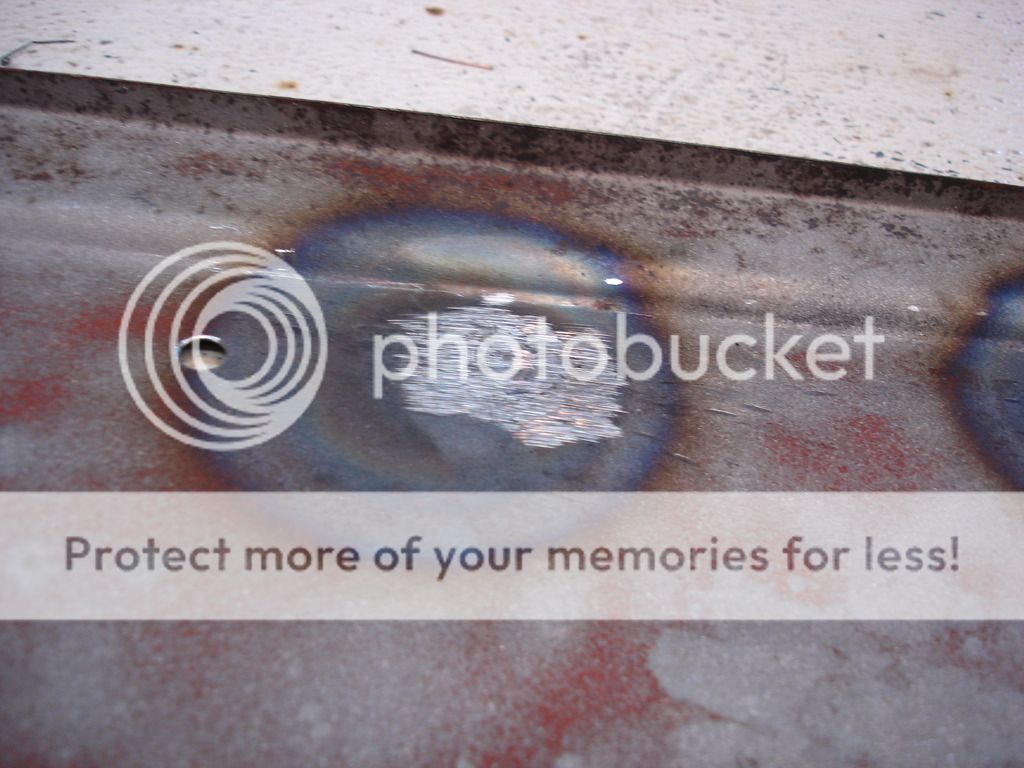
Here is a quick tip using a body grinder. The license plate holes that were filled with weld were ground down, hammered flat, and here I am checking the final surface by using the body grinder to just skim the area with the disc held very flat. It immediately tells you if and where the high and low spots are. This hole looks perfect and is done.
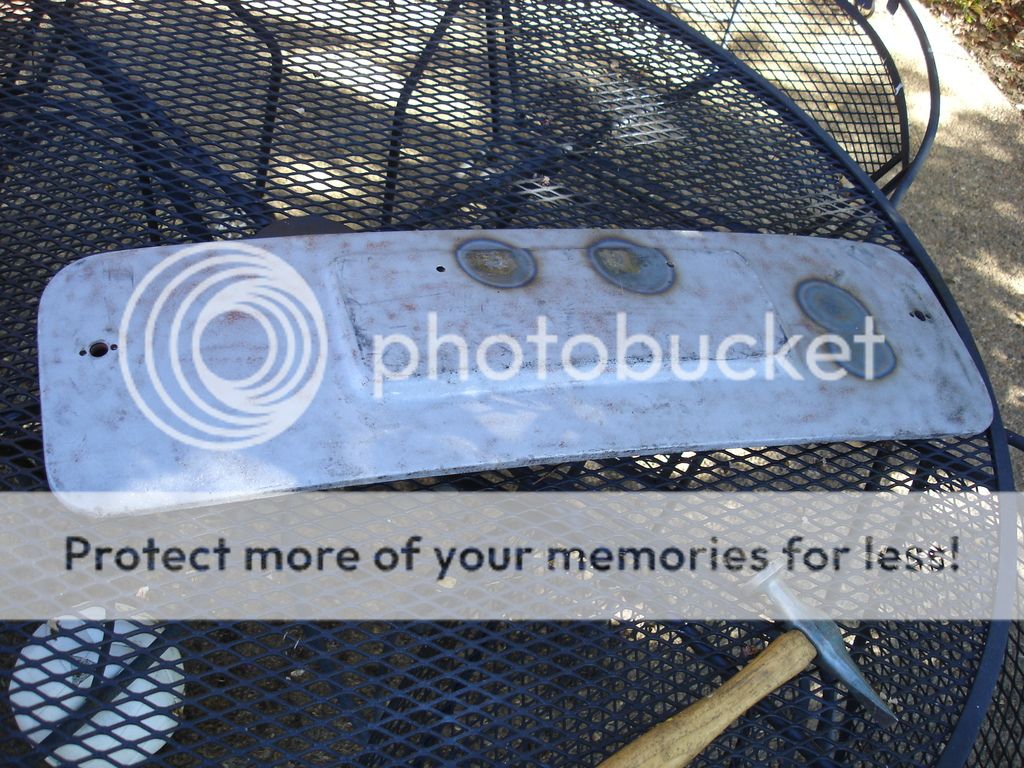
And the final cover, ready for fitting.
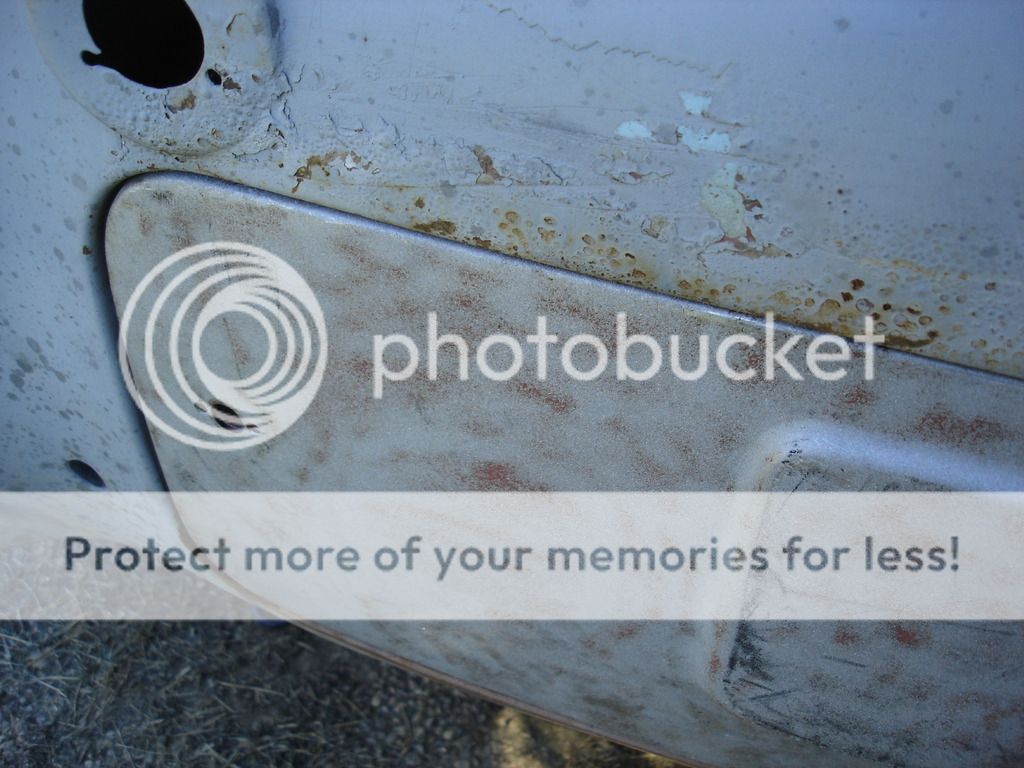
It looks like it fit perfectly. I assure that was not the case initially. This pic is after I spent another 2 hours carefully massaging the final curvature to get it to perfectly fit the rear valence. Normally I would fully test the latches and weatherstrip at this point. As you can see, I have to remove the TR3 turn lights from the rear valence, so it would be a waste at this point to get the fit too perfect. That will come later.
And that ends week 4...
Cheers!