Jim_Gruber
Yoda

Offline
Pics of Bugsy, rear quarter panel repair. Panels on both sides plus panel behind door were simple tack welded in place. I'm thinking I need to finish welding these panels with a stitch well and then lots of grinding. I don't think seam sealer is called for. Lots of small welds with the MIG and then grind flat. Here's what I've got. Need some advice. Thanks
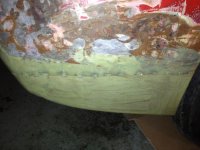
Green stuff is aviation restoration primer, red stuff, well rust on surface.
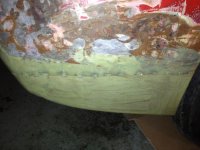
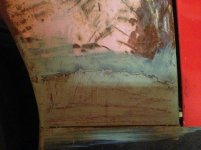