It's hard to believe that it's been over a year since I posted here. Sorry about that to anyone following the progress.
I thought I was going to have to sell the car due to some unfortunate events with mine and my wifes employment but those worked themselves out and work is continuing.
These are some pics of the current condition of the car.
The floorpan fitment is going pretty well along with the trial fitting of the inner and outer sills. I stall have a few places where the rust had started in the seam and rusted not only the floor pan but the adjoining panel as well so i have to make pieces to fill those gaps and restore the flanges for the floor to attach to.
But it is definitely coming along and I am happy with the results so far.
As always, thanks for looking.
IMG_20220721_125211 by Firebird2, on
IMG_20220721_125119 by Firebird2, on Flickr
IMG_20220721_125114 by Firebird2, on Flickr
IMG_20220721_125143 by Firebird2, on Flickr
I thought I was going to have to sell the car due to some unfortunate events with mine and my wifes employment but those worked themselves out and work is continuing.
These are some pics of the current condition of the car.
The floorpan fitment is going pretty well along with the trial fitting of the inner and outer sills. I stall have a few places where the rust had started in the seam and rusted not only the floor pan but the adjoining panel as well so i have to make pieces to fill those gaps and restore the flanges for the floor to attach to.
But it is definitely coming along and I am happy with the results so far.
As always, thanks for looking.
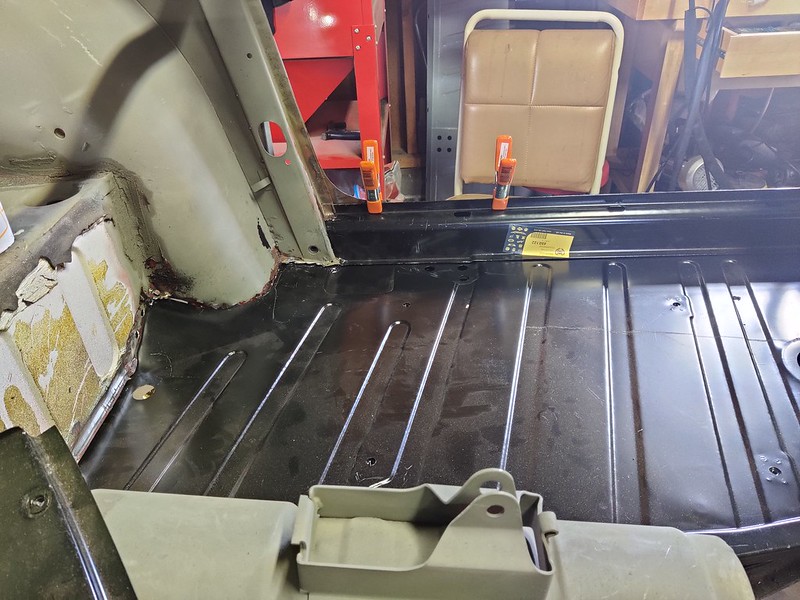


