CJD
Yoda

Offline
Now on to more inspections during a rebuild. Here are 3 3rd gears.
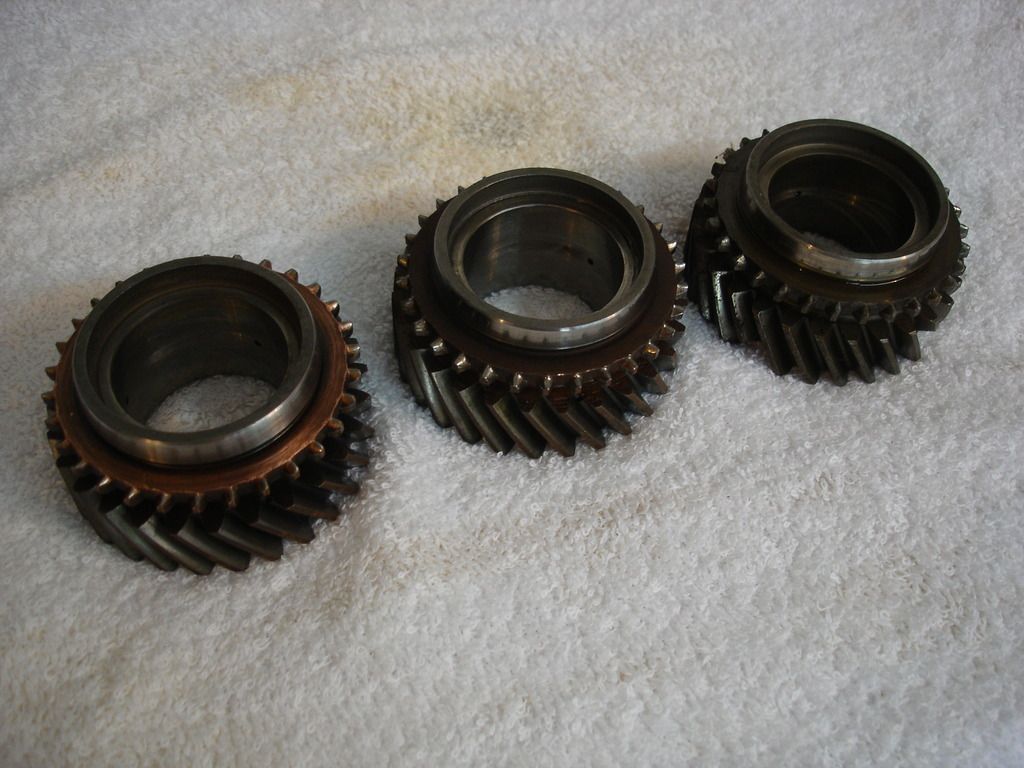
At first glance they look about the same, but these are the areas you are looking for...
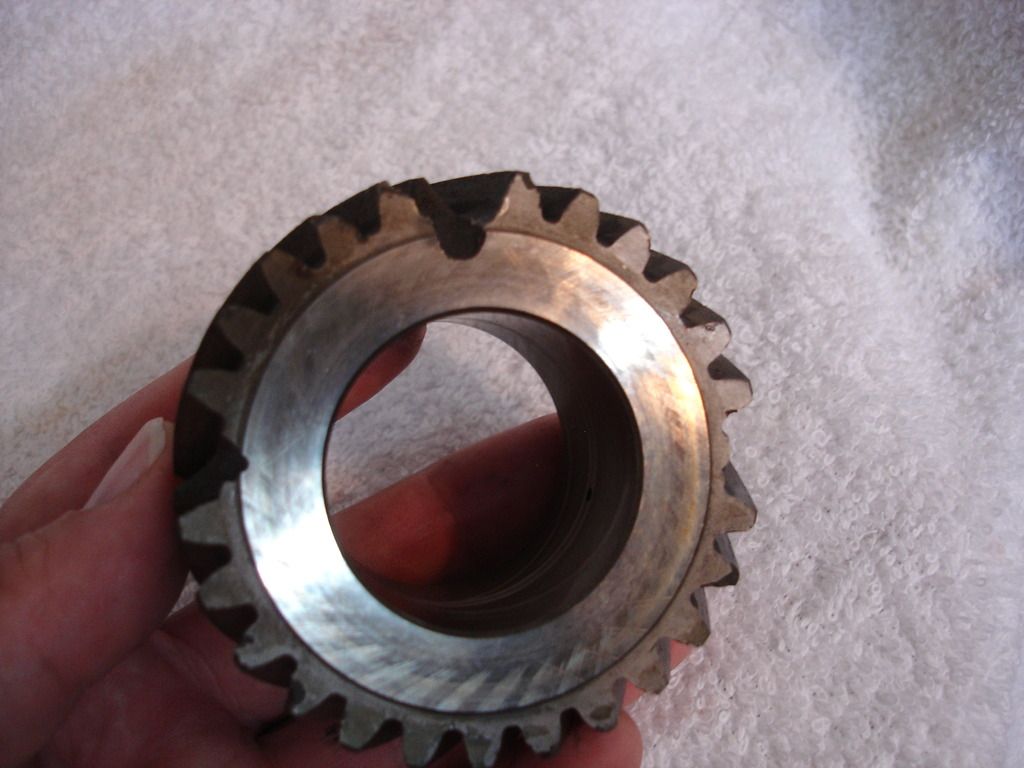
Bad...missing teeth.
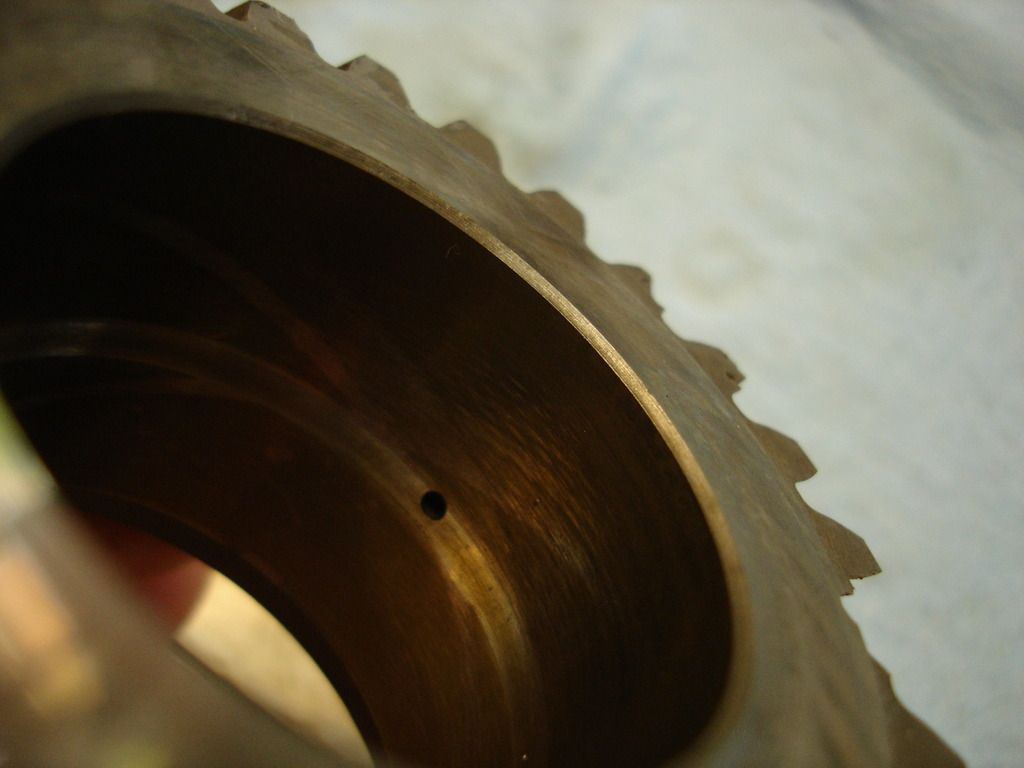
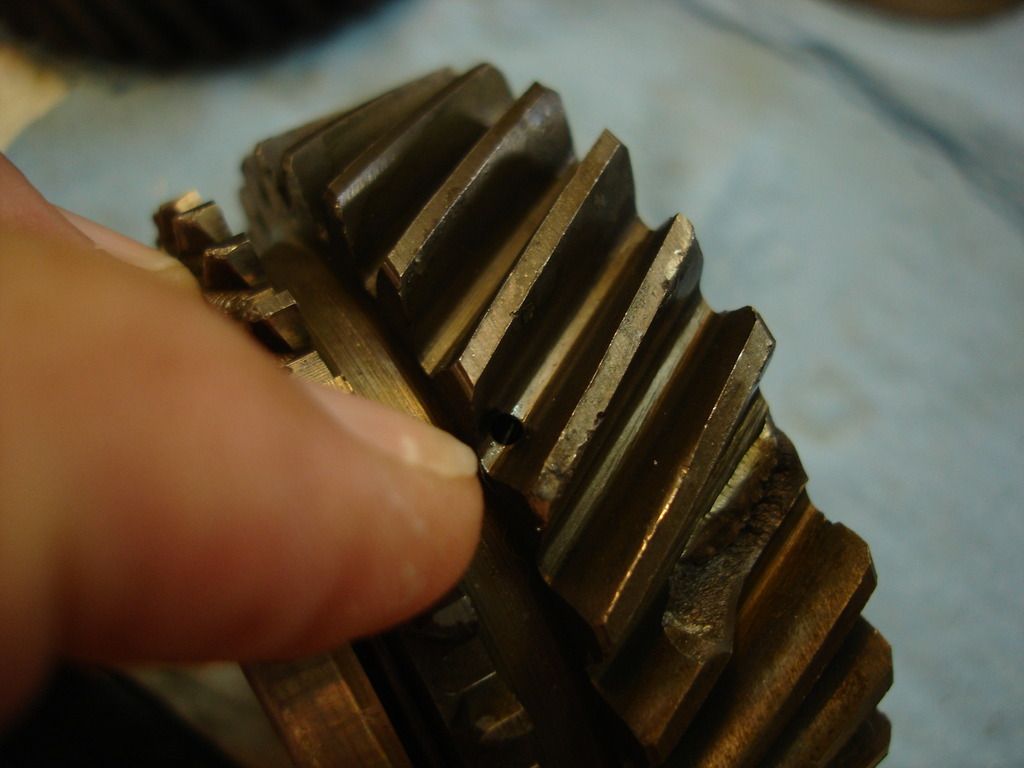
Oil holes free and clear on both sides.
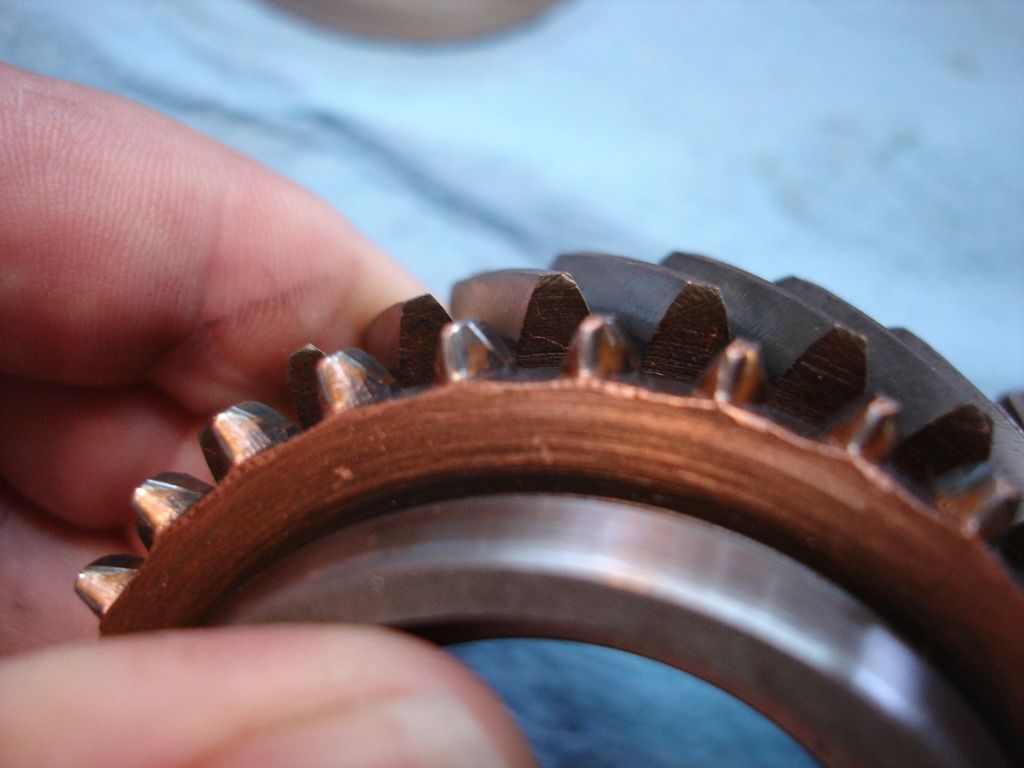
Dog teeth. This gear has relatively rounded dog teeth, so I would expect it to jam when shifting every so often. The teeth should be sharp and well defined at the front.
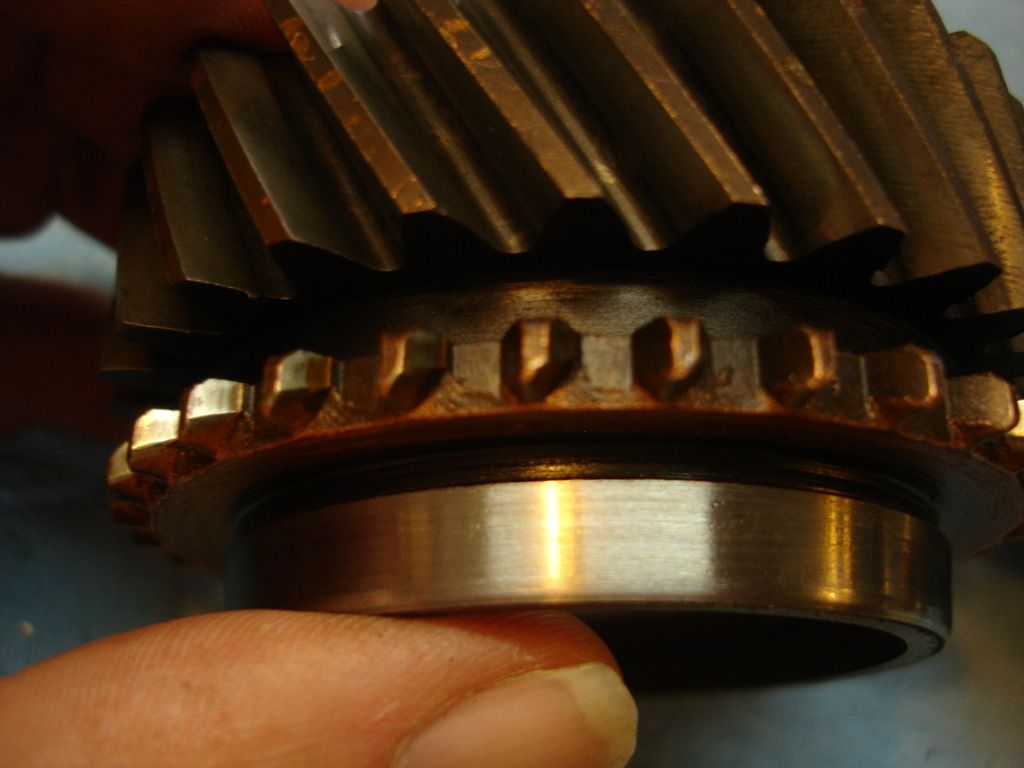
These dog teeth are actually worn so the teeth look like they were cut at an angle. They were not...this is from many grinding engagements.
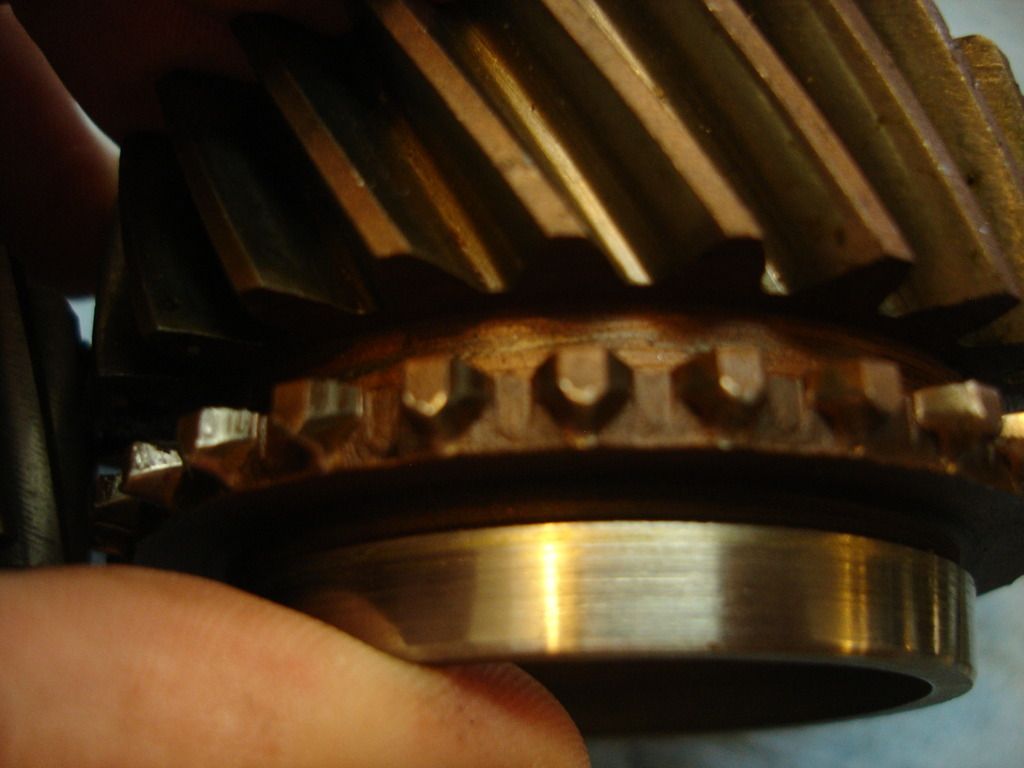
This example is about as bad as I would consider putting back in the box. They can be mildly dressed and made to work perfectly. Any worse and it's best to find a new gear.
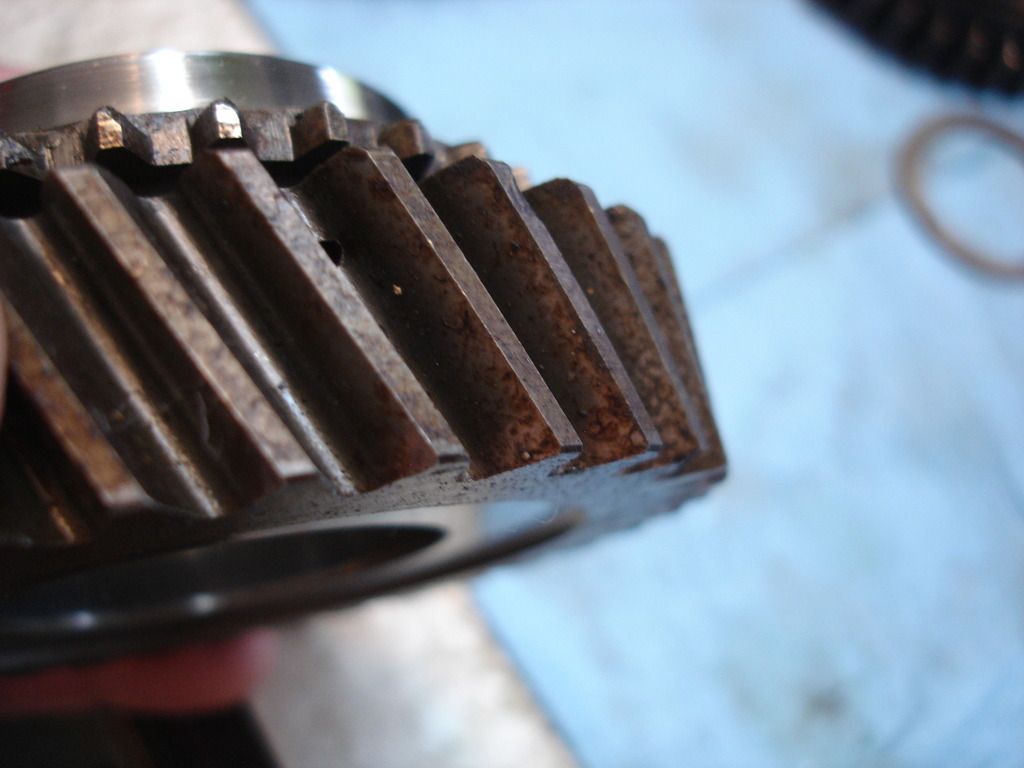
Don't forget to watch for corrosion. At rest, only the lower 1/4 of a gearbox is covered in oil. If a car sits for long periods, many of the gears are out of oil and exposed to condensation, and corrosion. This gear is pitted and marginal for re-use.
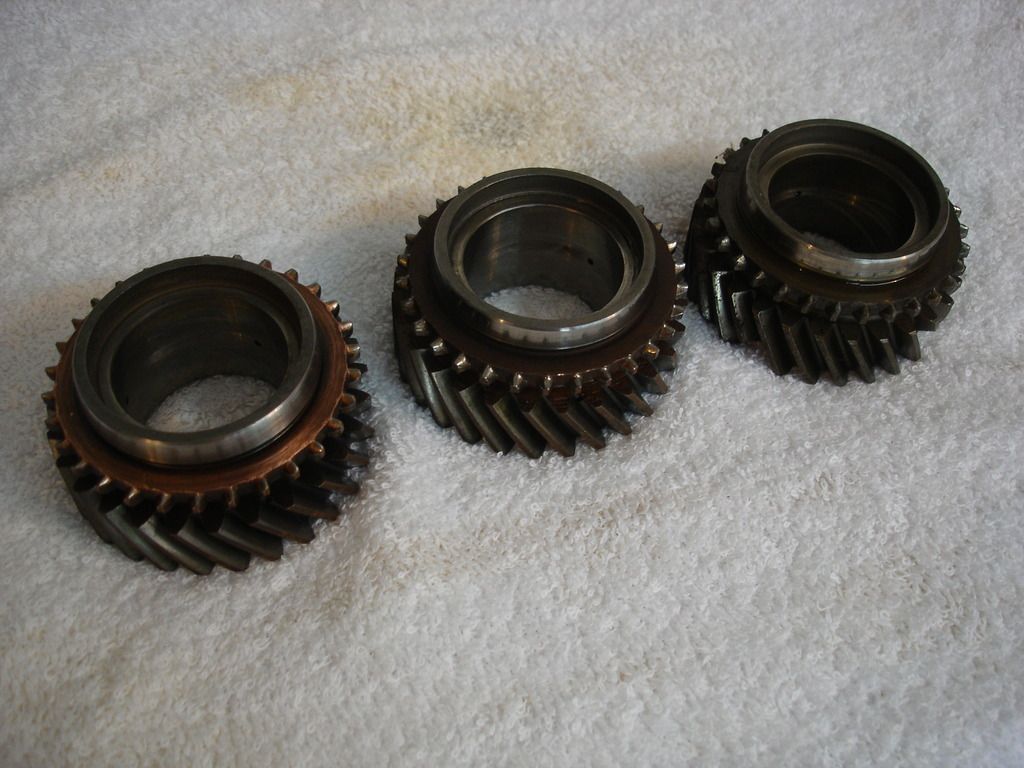
At first glance they look about the same, but these are the areas you are looking for...
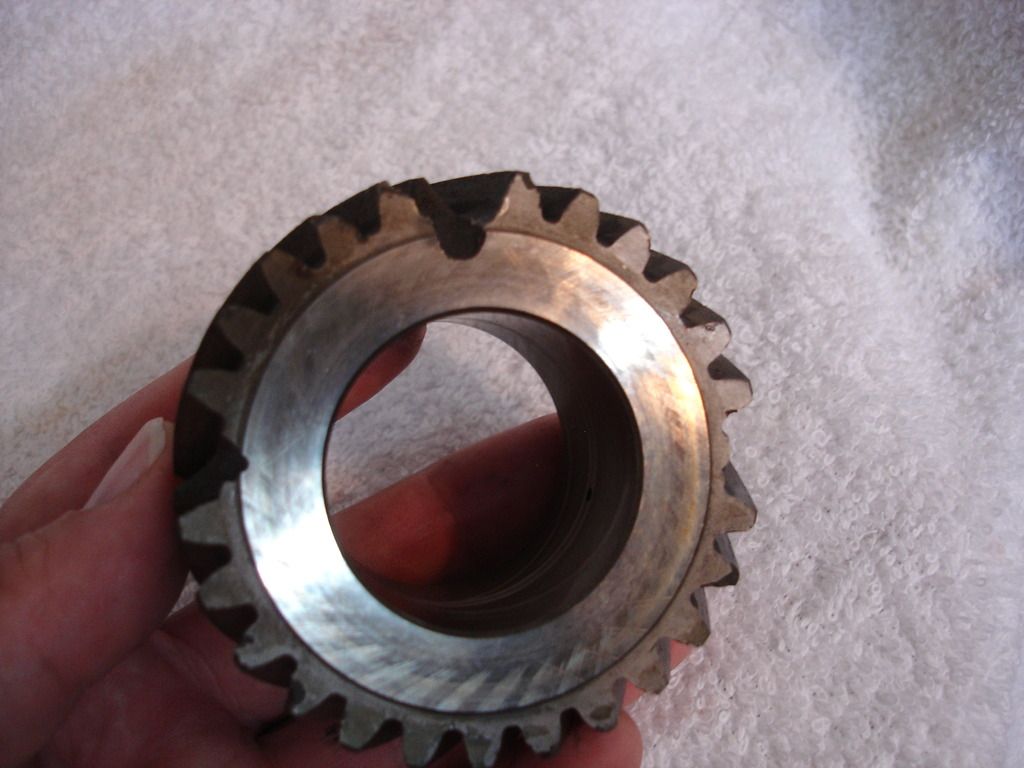
Bad...missing teeth.
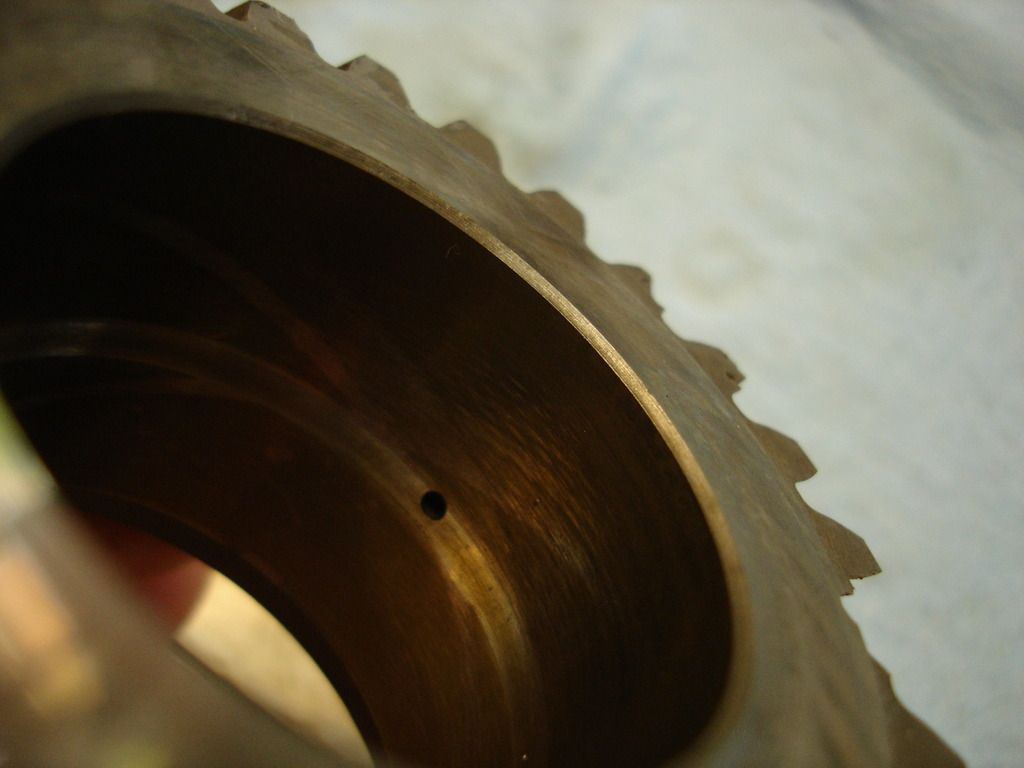
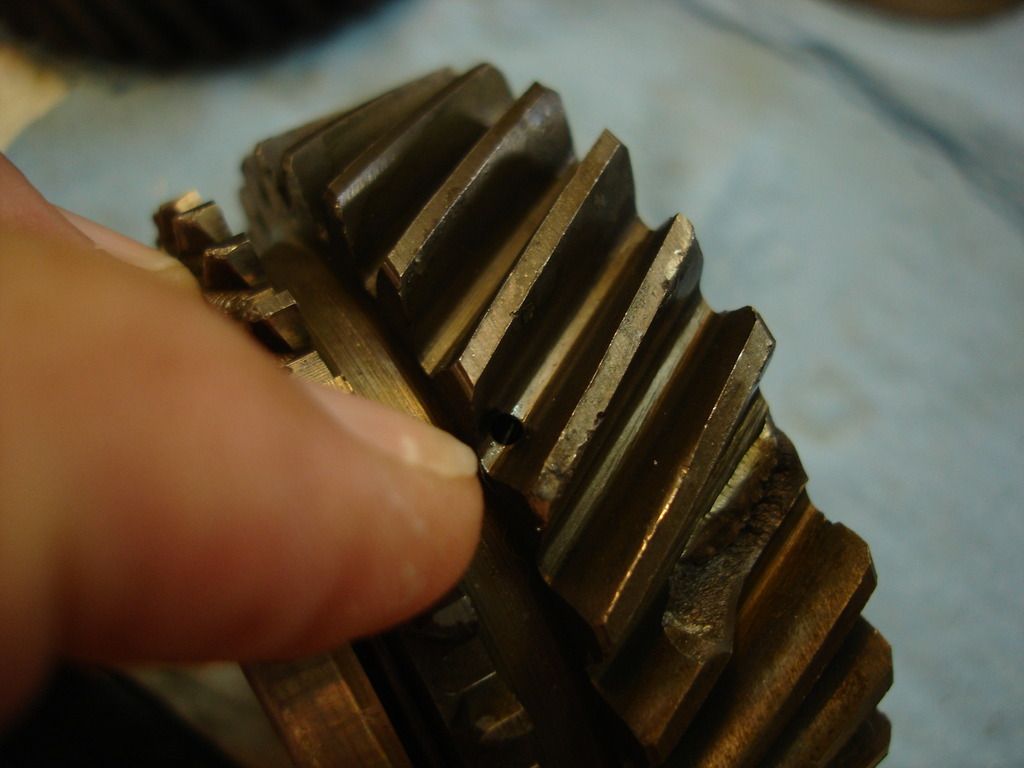
Oil holes free and clear on both sides.
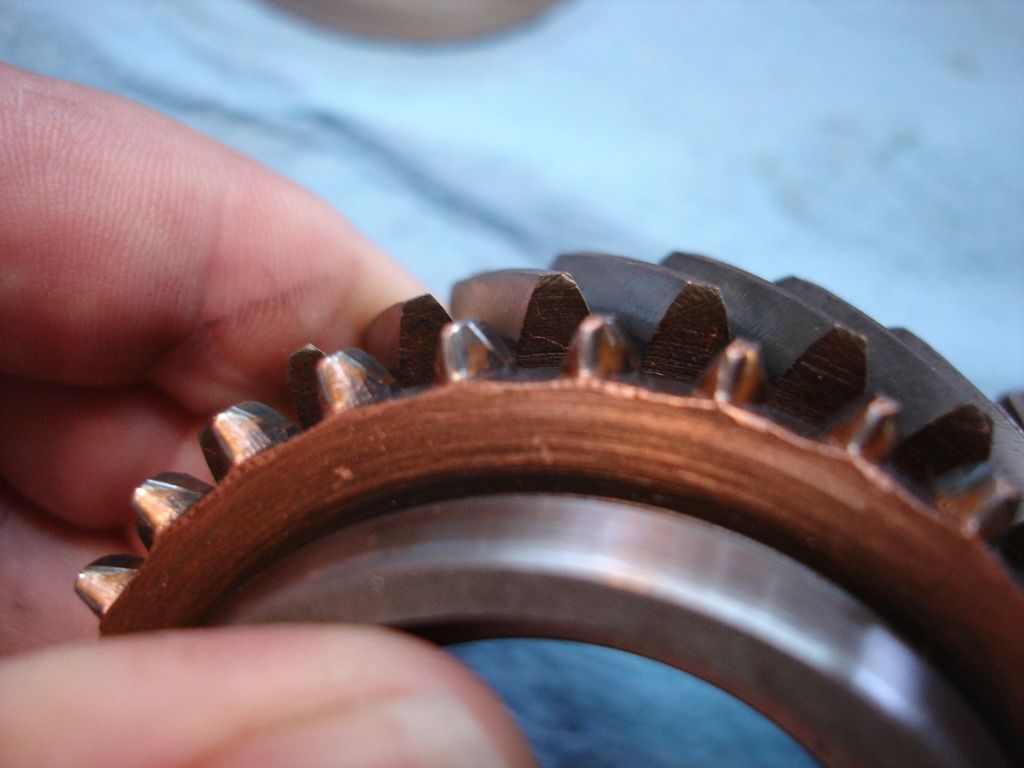
Dog teeth. This gear has relatively rounded dog teeth, so I would expect it to jam when shifting every so often. The teeth should be sharp and well defined at the front.
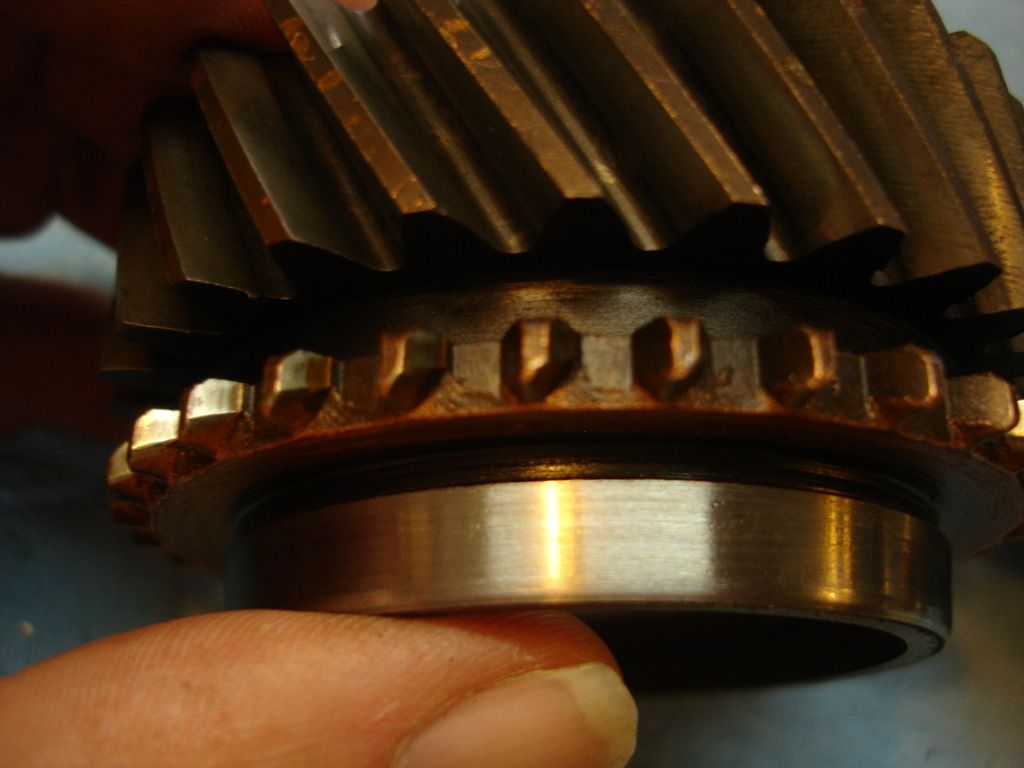
These dog teeth are actually worn so the teeth look like they were cut at an angle. They were not...this is from many grinding engagements.
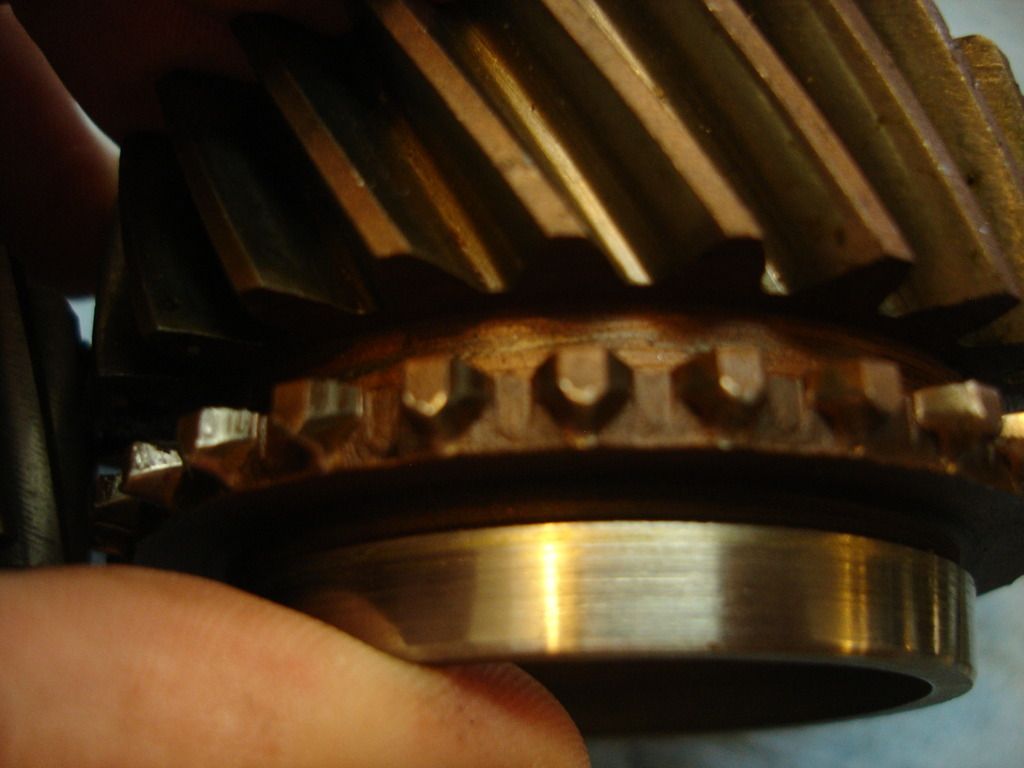
This example is about as bad as I would consider putting back in the box. They can be mildly dressed and made to work perfectly. Any worse and it's best to find a new gear.
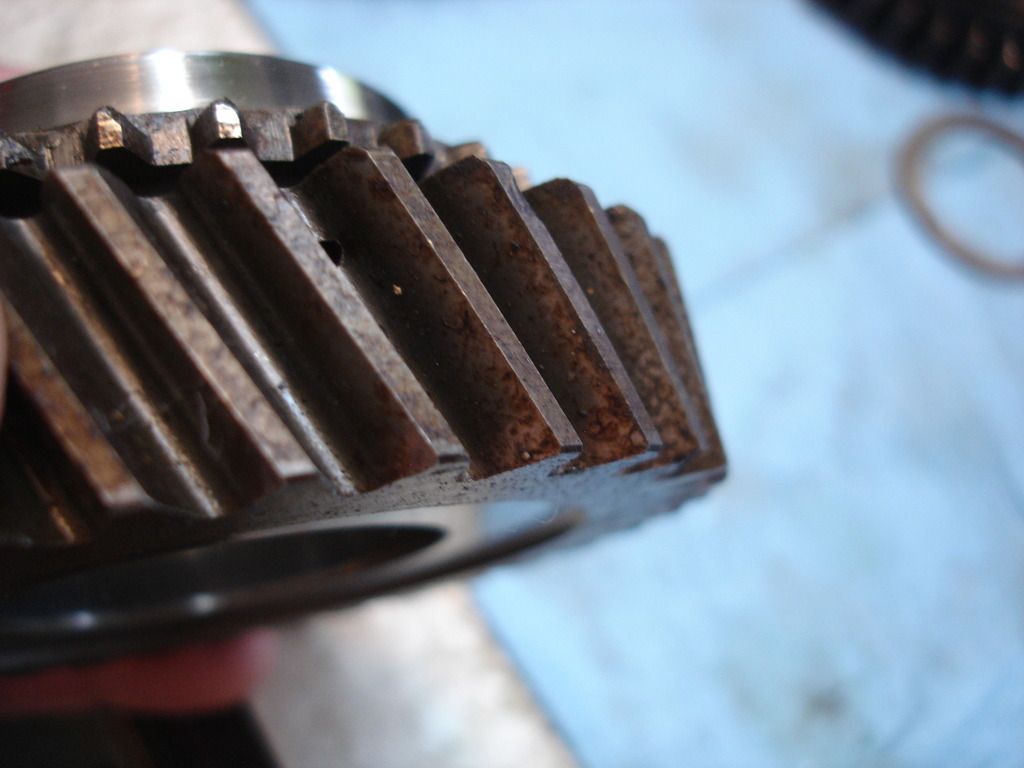
Don't forget to watch for corrosion. At rest, only the lower 1/4 of a gearbox is covered in oil. If a car sits for long periods, many of the gears are out of oil and exposed to condensation, and corrosion. This gear is pitted and marginal for re-use.