2wrench
Luke Skywalker

Offline
Excited now, Forum Members. I have properly degreed my
cam and placed the timing chain on along with the timing
gears. Yahooooo! Calls for four bananas for this one!
:banana: :banana: :banana: :banana:
Also, while I recognize all supportng members, I want
to mention a Mr. D. K. Lawson, who sent me a computer
printable version of a degree wheel. I used his because
it was a full 8-inch version (sometimtes size matters)
and I could read the thing better than any others. Thanks,
DK.
First, I installed the crank gear and bolted on the cam
gear torqued to spec temporarily to align and verify that
the gears line up well....and they do:
Next I dropped a lifter (cam follower) into the number one
intake valve (second back from the front of the engine)
and dropped in a properly oriented push rod:
Next I placed my magnetic-based dial gauge indicator on top
of the push rod and rotated the cam gear until that push
rod was pushed to its highest point. As I rotated, it would
hit the high spot, then begin to descend; so rotate back
up again until I felt in my wrist/the cam gear, and also
watching by eye, that the push rod was up at its peak.
This is where we want to be. Leave it right there.
So far, so good:
The next step was to make a pointer that would be attached
to the engine that would remain solid and static for reading
the degree cam protractor (the one received from Lawson).
I went the the wife's kitchen (opps, did I say that?)....
I mean, my old tool box and pulled out a shish-ka-bob
skewer. The one I used encircled itself at one of its
ends, so I used this end to put a bolt through with a
washer and snugged it into place with one of the bolts
from the timing chain cover, then bent the metal into its
closest position pointing to top dead center:
A visit to Orchard Supply Hardware produced a smaller-in-length
but properly threaded bolt that will temporarily be placed
into the end of the crank holding the paper-made protractor
which I printed from my computer and pasted onto cardboard.
Here I show myself snuggin the bolt down with the protractor
set a 0 degrees top dead center; numbers one and six pistons
at top dead center:
Now a close-up with everything snugged and fine tuned and
ready to twist the crank to its proper orientation:
Now a pause: As every cam that is other than OEM spec,
a performance cam (albeit gentle) such as mine is going
to be set to different specifications. My cam is a
new (not reground) BP270 purchased from British Parts Northwest. (Good guys). They did forget to send the
installation instructions, but I got them immediately
via internet once I contacted them. No big sweat.
So my specs called for turning the crank (now that we are
at the point shown in the pictures) to the position of
112 degress ATDC, which stands for: After top dead center.
That means the crank was rotated clockwise, now, slowly
watching the pointer untill the protractor showed 112
degrees to the left side of zero, which is after top dead center. I darkened this degree line in for easy reference.
I noticed, when doing this, that two other pistons shifted
into position of top dead center. Instead of one and six
there, two and five moved up to top dead center.
This is proper orientation for cam to crank. Each,
respectively, are left where they are and the timing
gear is installed.
What actually happens is that as the chain is put into
place, (remove the cam gear; start by placing onto the
crank first, then placing onto the cam gear...), a slight
movement of the cam one gear tooth left or right must take
place (unless of course you have an adjustable cam gear).
I was told this amount of loss in perfection is negligable
and adjustable gears are mostly used for racing engines.
So, on went the timing chain and I'm a happy camper.
Now, I need to rest, but you know I'm such a blabber
that I'll be back on soon with more to say, more than
likely.
Now I'll sit to think about what is coming...and I do
have questions to ask. I need to organize my thoughts.
Cheers,
cam and placed the timing chain on along with the timing
gears. Yahooooo! Calls for four bananas for this one!
:banana: :banana: :banana: :banana:
Also, while I recognize all supportng members, I want
to mention a Mr. D. K. Lawson, who sent me a computer
printable version of a degree wheel. I used his because
it was a full 8-inch version (sometimtes size matters)
and I could read the thing better than any others. Thanks,
DK.
First, I installed the crank gear and bolted on the cam
gear torqued to spec temporarily to align and verify that
the gears line up well....and they do:
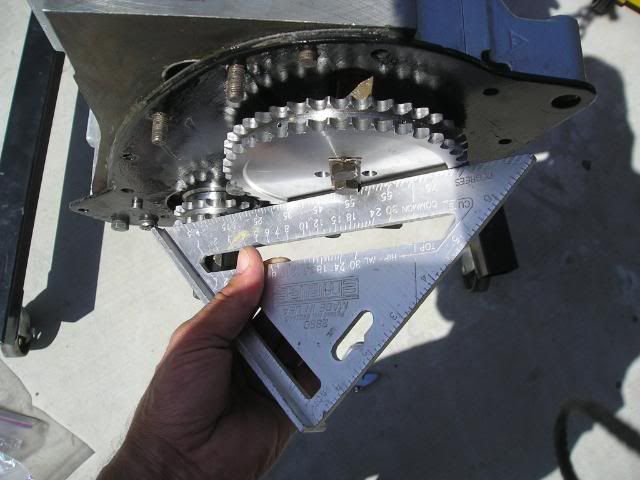
Next I dropped a lifter (cam follower) into the number one
intake valve (second back from the front of the engine)
and dropped in a properly oriented push rod:
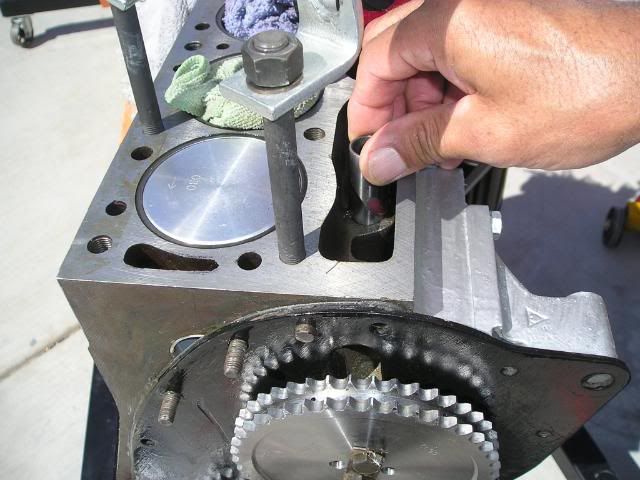
Next I placed my magnetic-based dial gauge indicator on top
of the push rod and rotated the cam gear until that push
rod was pushed to its highest point. As I rotated, it would
hit the high spot, then begin to descend; so rotate back
up again until I felt in my wrist/the cam gear, and also
watching by eye, that the push rod was up at its peak.
This is where we want to be. Leave it right there.
So far, so good:
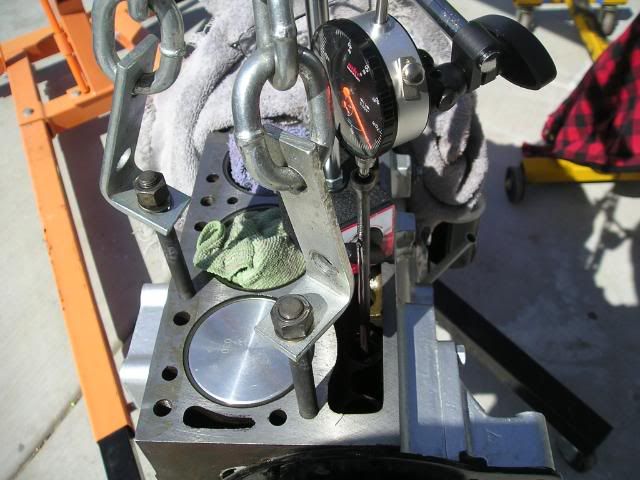
The next step was to make a pointer that would be attached
to the engine that would remain solid and static for reading
the degree cam protractor (the one received from Lawson).
I went the the wife's kitchen (opps, did I say that?)....
I mean, my old tool box and pulled out a shish-ka-bob
skewer. The one I used encircled itself at one of its
ends, so I used this end to put a bolt through with a
washer and snugged it into place with one of the bolts
from the timing chain cover, then bent the metal into its
closest position pointing to top dead center:

A visit to Orchard Supply Hardware produced a smaller-in-length
but properly threaded bolt that will temporarily be placed
into the end of the crank holding the paper-made protractor
which I printed from my computer and pasted onto cardboard.
Here I show myself snuggin the bolt down with the protractor
set a 0 degrees top dead center; numbers one and six pistons
at top dead center:

Now a close-up with everything snugged and fine tuned and
ready to twist the crank to its proper orientation:
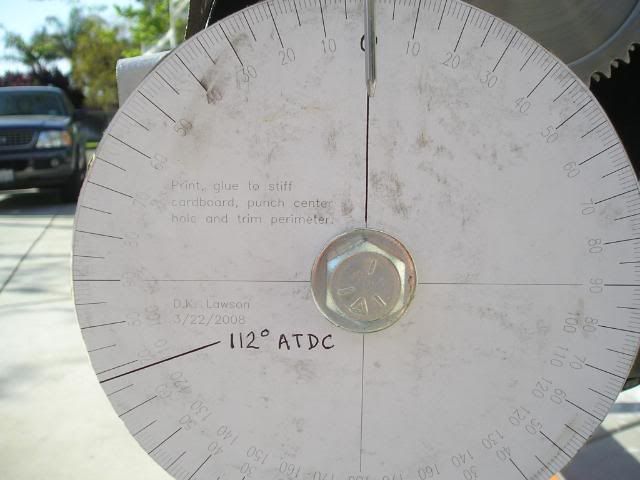
Now a pause: As every cam that is other than OEM spec,
a performance cam (albeit gentle) such as mine is going
to be set to different specifications. My cam is a
new (not reground) BP270 purchased from British Parts Northwest. (Good guys). They did forget to send the
installation instructions, but I got them immediately
via internet once I contacted them. No big sweat.
So my specs called for turning the crank (now that we are
at the point shown in the pictures) to the position of
112 degress ATDC, which stands for: After top dead center.
That means the crank was rotated clockwise, now, slowly
watching the pointer untill the protractor showed 112
degrees to the left side of zero, which is after top dead center. I darkened this degree line in for easy reference.
I noticed, when doing this, that two other pistons shifted
into position of top dead center. Instead of one and six
there, two and five moved up to top dead center.
This is proper orientation for cam to crank. Each,
respectively, are left where they are and the timing
gear is installed.
What actually happens is that as the chain is put into
place, (remove the cam gear; start by placing onto the
crank first, then placing onto the cam gear...), a slight
movement of the cam one gear tooth left or right must take
place (unless of course you have an adjustable cam gear).
I was told this amount of loss in perfection is negligable
and adjustable gears are mostly used for racing engines.
So, on went the timing chain and I'm a happy camper.
Now, I need to rest, but you know I'm such a blabber
that I'll be back on soon with more to say, more than
likely.
Now I'll sit to think about what is coming...and I do
have questions to ask. I need to organize my thoughts.
Cheers,