So when removing the splash guard from my earlier post the bolt snapped.
Tips and techniques for removing it?
This is what is left from the bottom inner fender bolt head that secures the splash guard to the wheel well. Even California cars get wet some times. Metal here will be cleaned up or replaced prior to reassembly...
Tips and techniques for removing it?
This is what is left from the bottom inner fender bolt head that secures the splash guard to the wheel well. Even California cars get wet some times. Metal here will be cleaned up or replaced prior to reassembly...
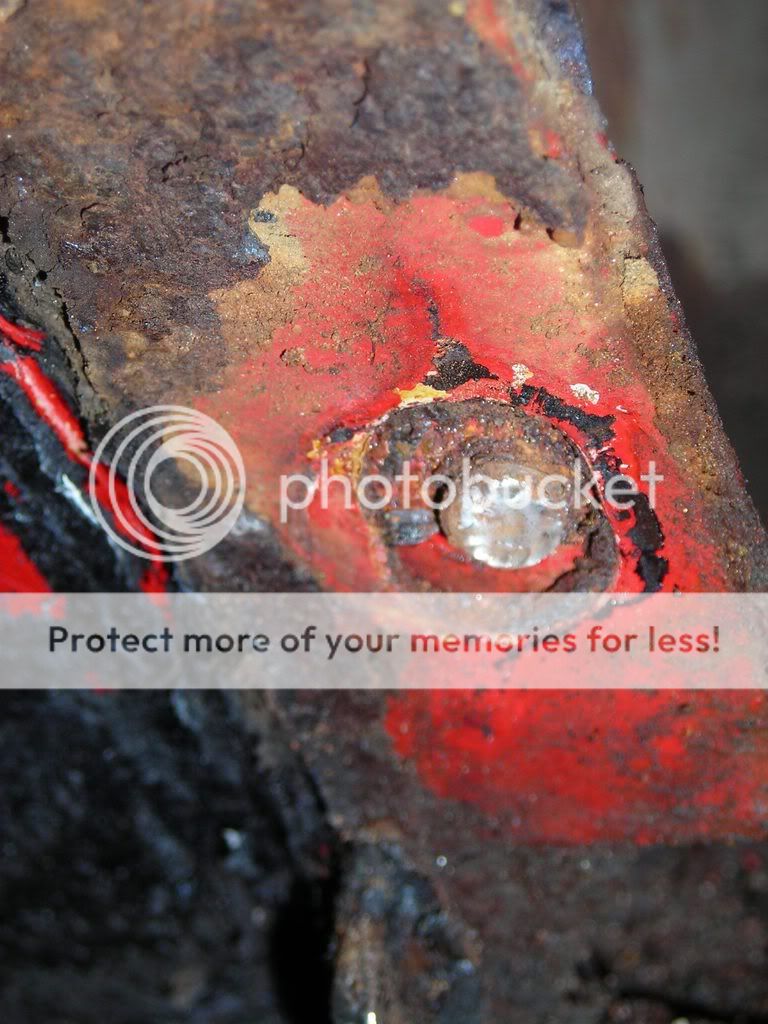